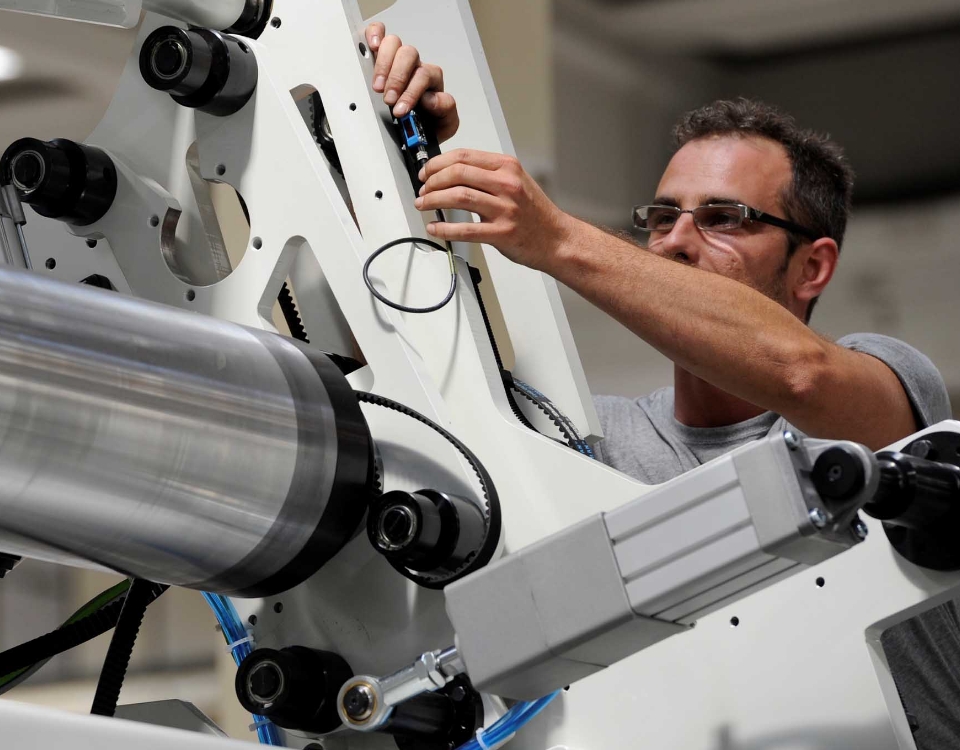
This press brake is equipped with the Gasparini Adaptive Crowning System and the E-Reflex Deformation Compensation System. The combination of these two systems allows excellent results in terms of quality, precision and repeatability of the parts to be bent. Thanks to the camber, in fact, the two rams are perfectly parallel and it is possible to obtain total control of the angle. The E-Reflex then monitors the bending of the structure thanks to a network of sensors in the press brake and hydraulic system. The error is measured and compared with the ram position and oil pressure. We can thus calculate the actual height at which the punch is located, regardless of deformations.
The clamping system of this machine consists of:
- hydraulic self-aligning clamping system type H-GX for punches or intermediates
- 200 mm high Gasparini AirSlide pneumatic upper clamping for European type tools
- manual lower clamping
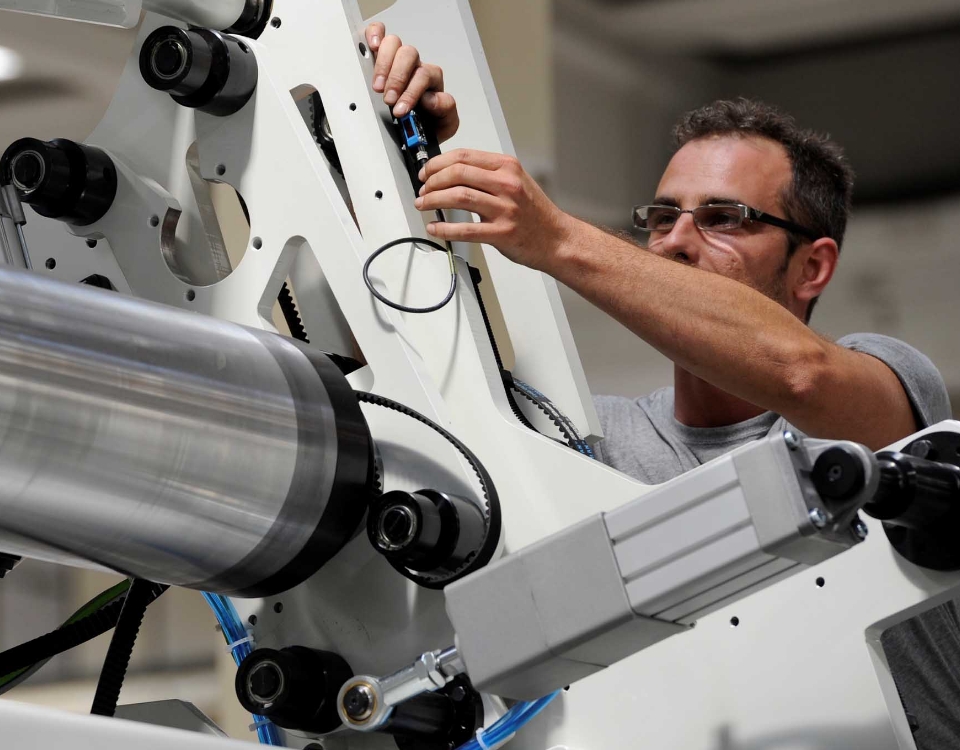
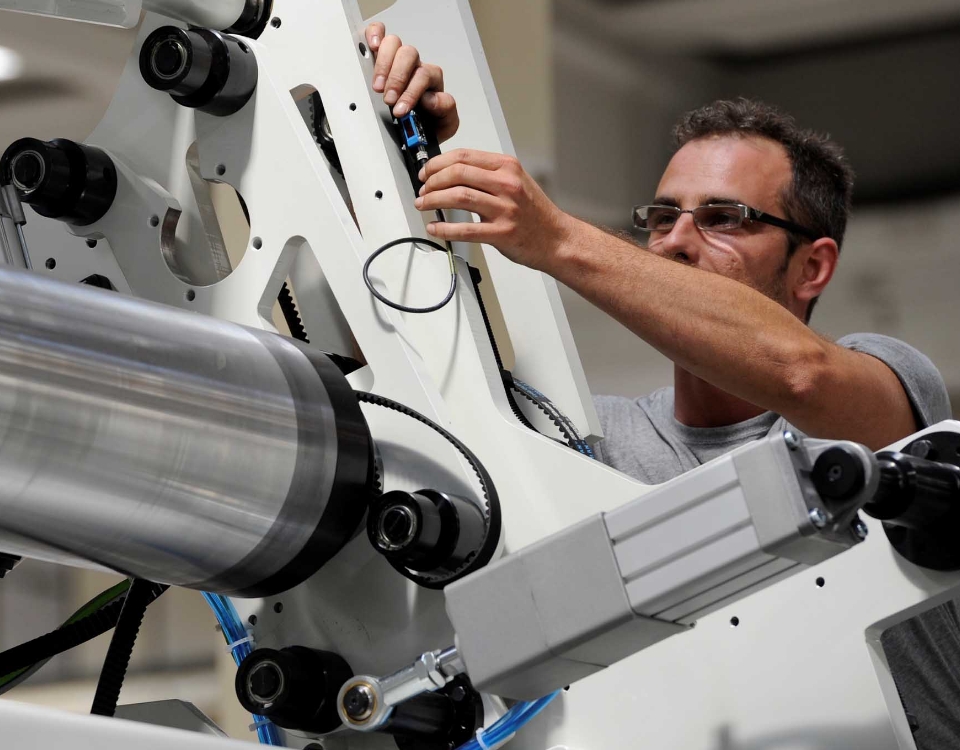
The backgauge has 6 CNC-controlled axes (X-R-Z1-Z2-X5-X6). In addition, it has been implemented with an additional stop and reference and 2 retractile back supports.
This press brake was equipped with the Tele-Link remote service function and the Industry 4.0 package.
<br
It was equipped with the Delem DA-69T CNC, mounted on a mobile console, with Delem Profile-T 3D offline software.
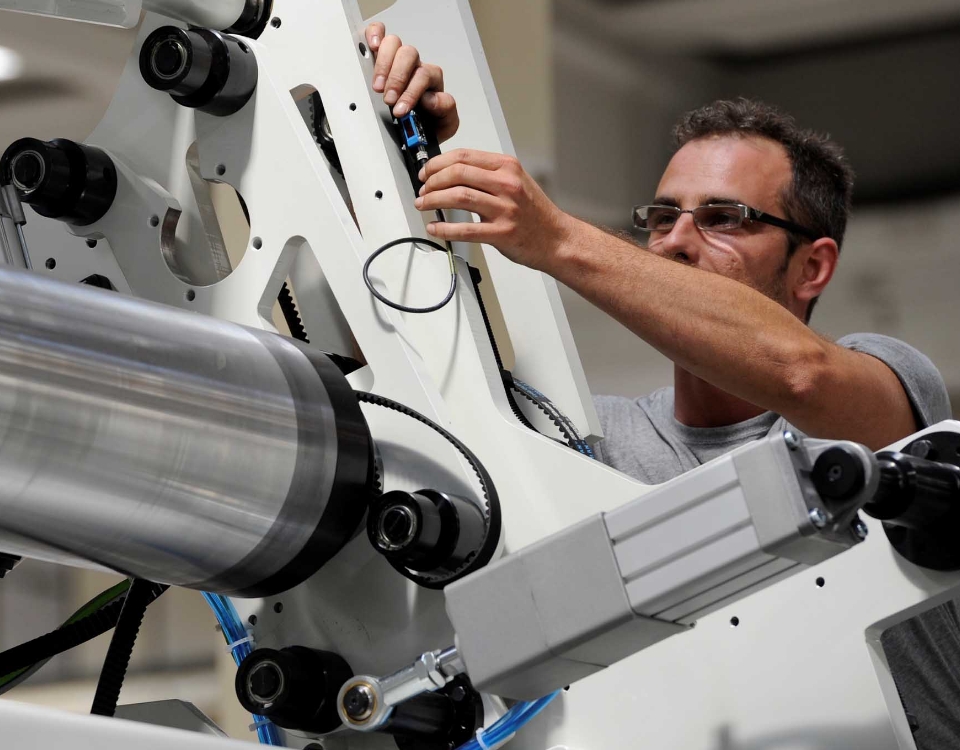
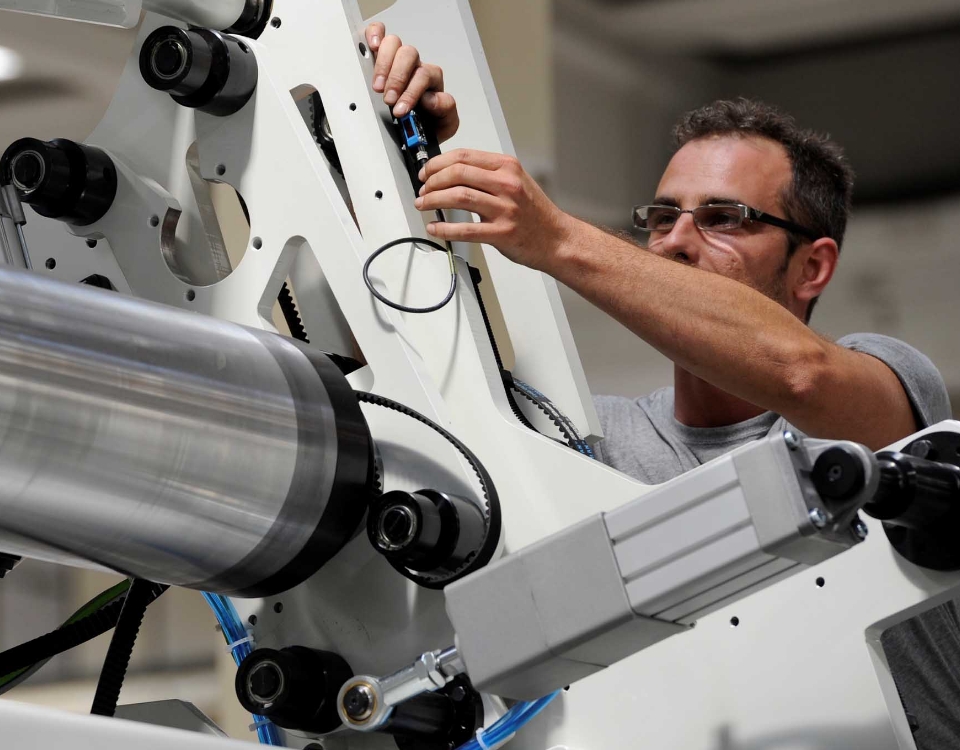
The safety system installed is of the DSP-AP laser type, which generates a visible laser beam conforming to EN12622. The beam protects the operator from the danger of crushing between punch and die.
This device allows the speed change point to be lowered by up to 4 mm from the plate. The result is that the upper cross beam moves at high speed for longer, limiting the part of the bending sequence where speed is reduced to a minimum.
In addition, the system is set up for automatic positioning of the safety photocells.
The customer chose to install:
- ECO energy-saving package
- Predisposition for pneumatic crusher
- Mechanical GPS4 preparation
- Drive bar for tool positioning
- Laser Line for reference-free bending
- Additional customised control panel
- 1 wireless sliding footpedal
- 1 low footpedal
- 2 sheet lifters with manual axis adjustment
- LED lighting of working area