Shear strength and ergonomics during cutting: how we achieved them
The cutting force is controlled by hydraulic plate presses, which are independent of the work cycle. The pressure exerted is properly adjusted so as not to damage the most delicate sheets. Since these are shears for the cutting process by robot, the plexiglass guard has been removed. In its place, a system of photocells placed at the sides of the work area was installed.
To achieve greater ergonomics and convenience, our shears are equipped with LED lighting of the work area, which is 300% more efficient than standard. This system also requires no maintenance and is insensitive to vibration. The light is set at 6000 °K to highlight metal edges and is optimized not to generate annoying heat radiation, reduce fatigue and glare.
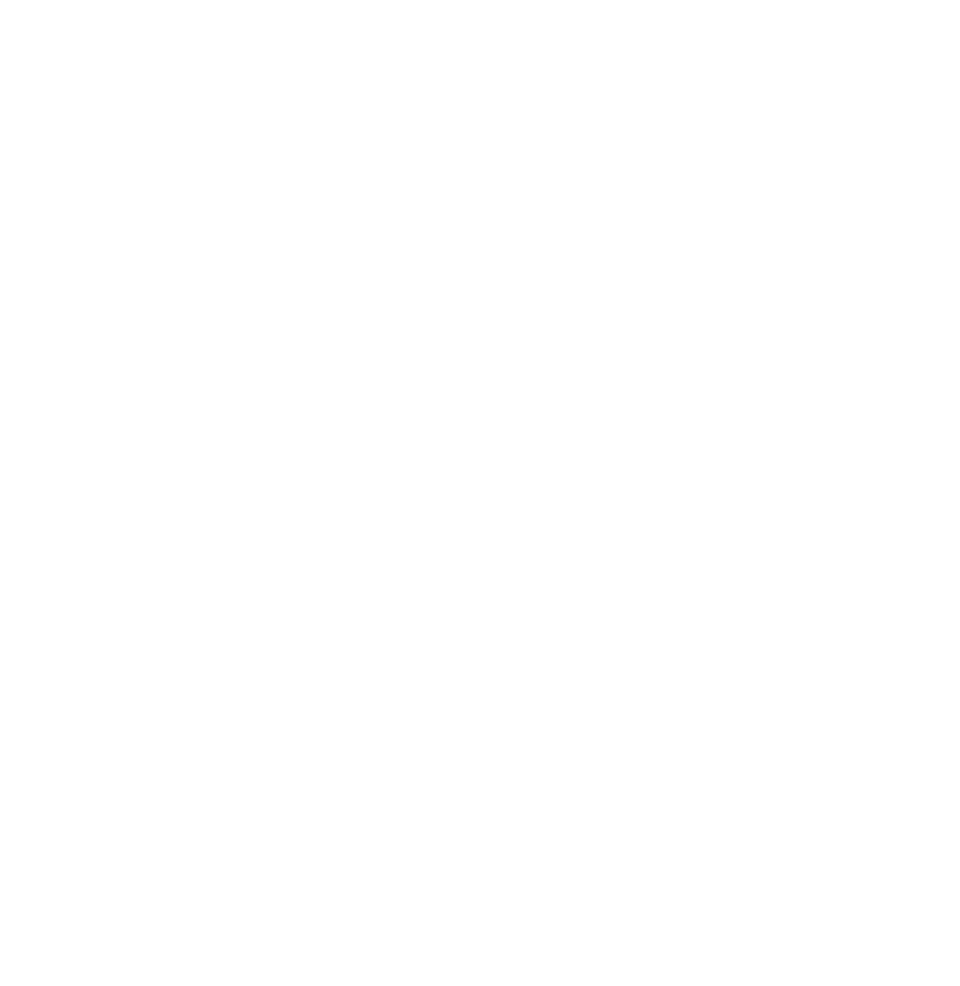
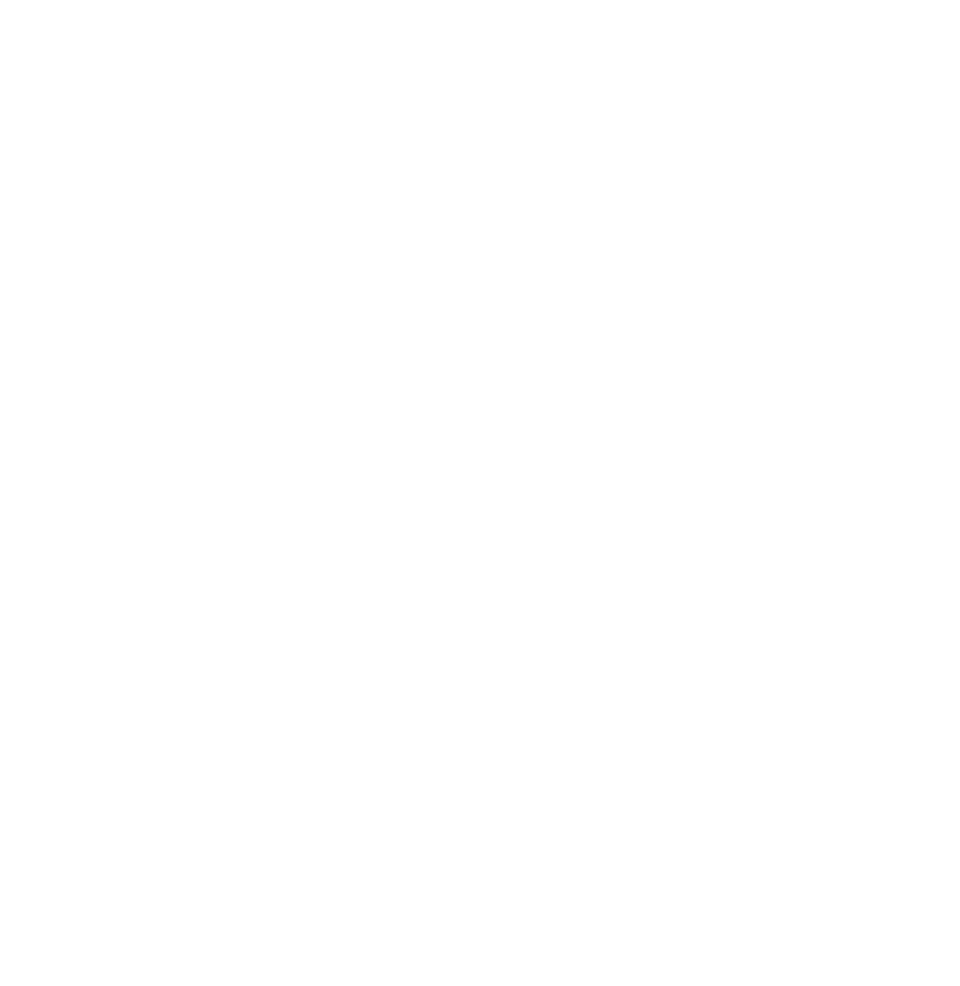
The choice of register
The sensorized back gauge of Gasparini’s two guillotine shears is not affected by the vibrations associated with the movement of the blade-holder beam, because it is anchored to the machine structure. Thanks to this solution, the back gauge is positioned with maximum speed, precision and repeatability. Maintenance is minimized by eliminating continuous adjustments due to the movement of the crosshead, ensuring the same native levels of accuracy over time.
The sensorized backgauge system is an optional feature that enables what is known as “contact cutting”: sensors detect the sheet metal as it enters position and initiate the cutting cycle. It can also be used as a control, preventing cutting if the sheet metal is not in contact with the register.
The CNC was developed by Gasparini and allows easy and intuitive management of every machine parameter through a 12” touchscreen display. It also has a complete material database to automatically adjust cutting angle, blade spacing and shearing force.
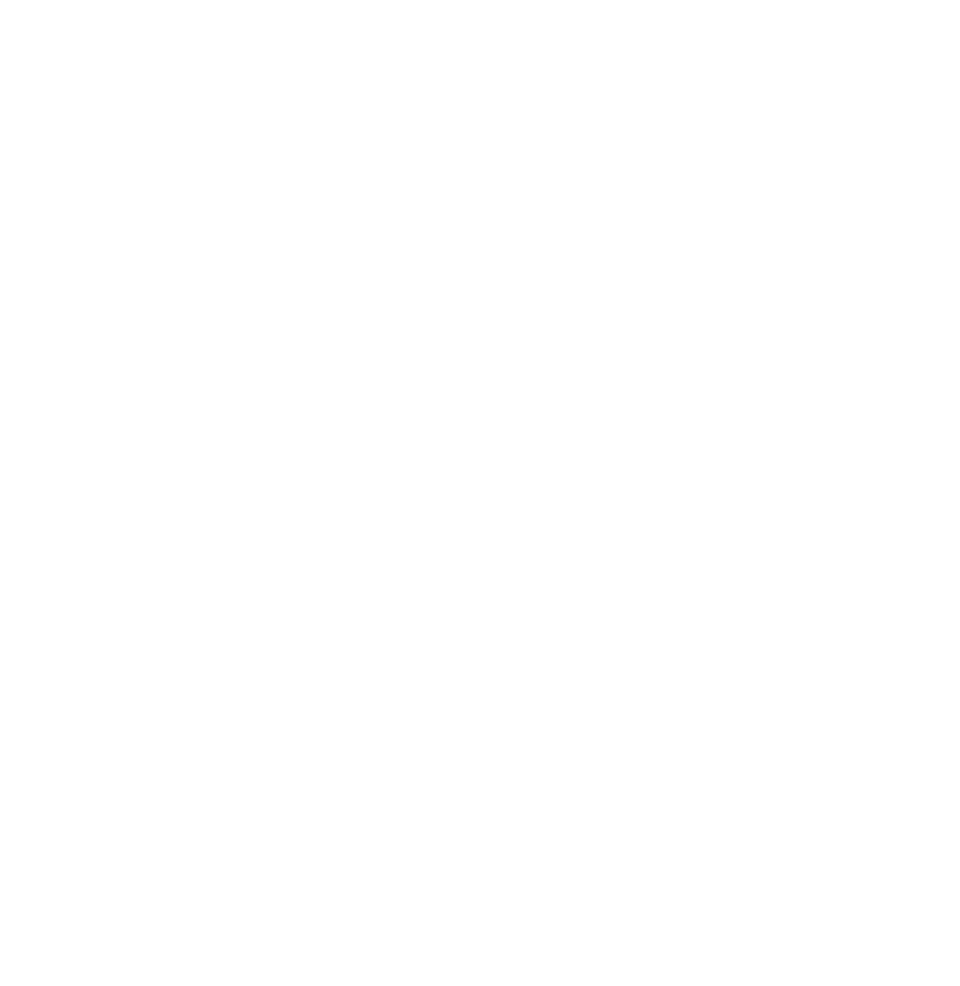