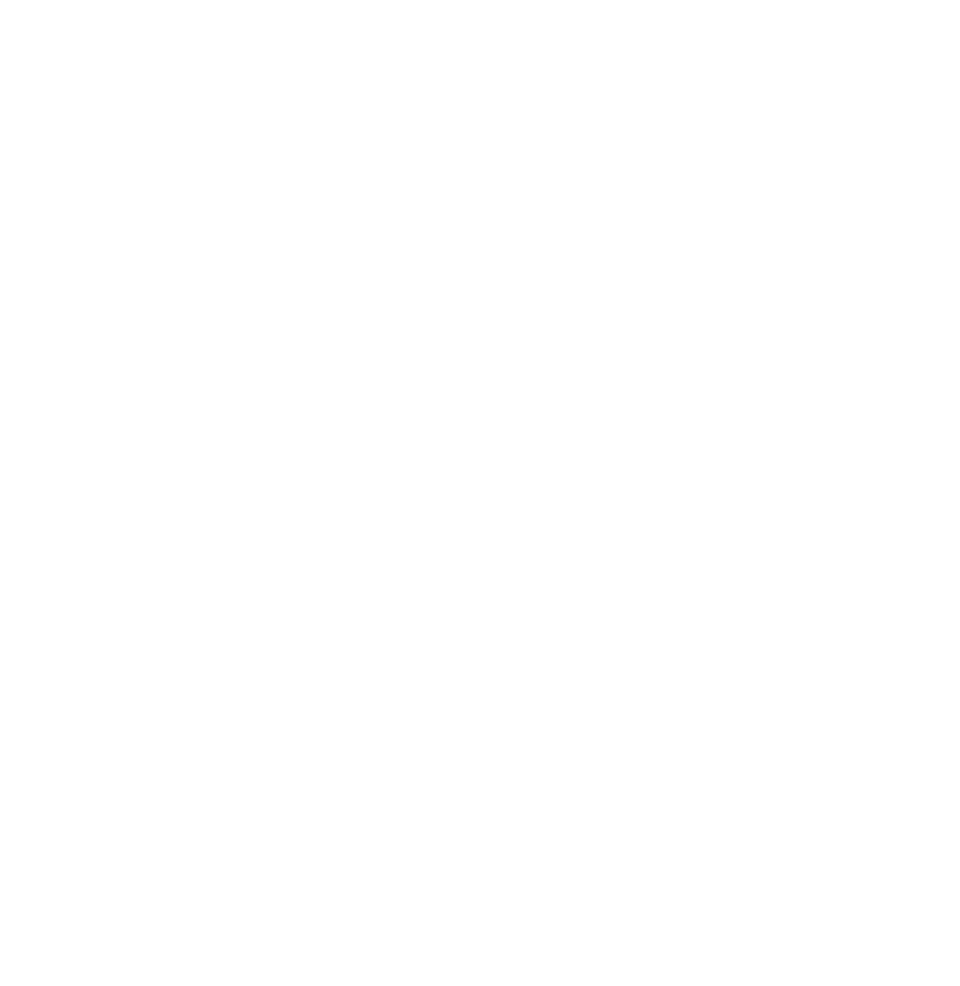
This machine has been set up for the Tele-Link remote service function, and the CNC is the Delem DA-69T type while the offline software is Delem Profile-T 3D. In addition, communication standards compliant with Industry 4.0 Intelligent Factory models have been installed.
The safety system installed is of the Laser DSP-AP type with lowered speed change point and reduced cycle time.
With regard to the choice of clamping systems, the customer decided to equip the press brake with the 110 mm high Gasparini AirSlide upper pneumatic system for European type tools, and the lower pneumatic clamping device. Gasparini AirSlide is an innovative compressed air distribution system that allows intermediates to be moved along the entire length of the ram in any position, without connecting pipes and without tools. They can be removed or added in any combination, without air leakage. In addition, they are self-aligning: the punches are lifted and brought into position.
The backgauge is 5-axis (X-R-Z1-Z2-X6) CNC-controlled, which in addition to the two standard axes also features the Z1 and Z2 axes. It is characterised by the addition of a stop on a backgauge reference for increased contact depth during the bending process.
This press brake is equipped with the E-Reflex deformation compensation system, which monitors the bending of the structure thanks to a network of sensors located inside the machine and in the hydraulic system. The error is measured and compared with the crosshead position and oil pressure.
Furthermore, this press brake was designed with the ECO energy-saving system, thanks to which energy wastage can be significantly reduced, thus improving productivity. The customer chose to equip it with a standard foot pedal, tool cabinet, and ergonomics kit.
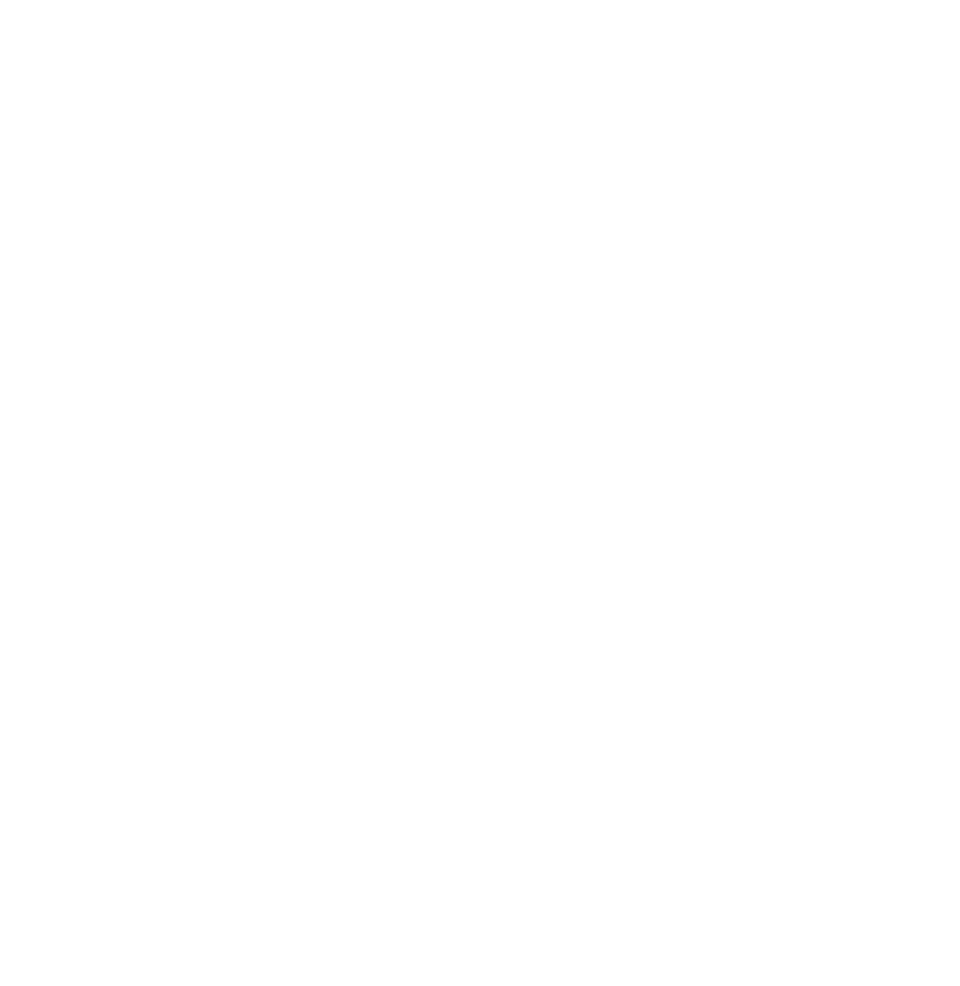
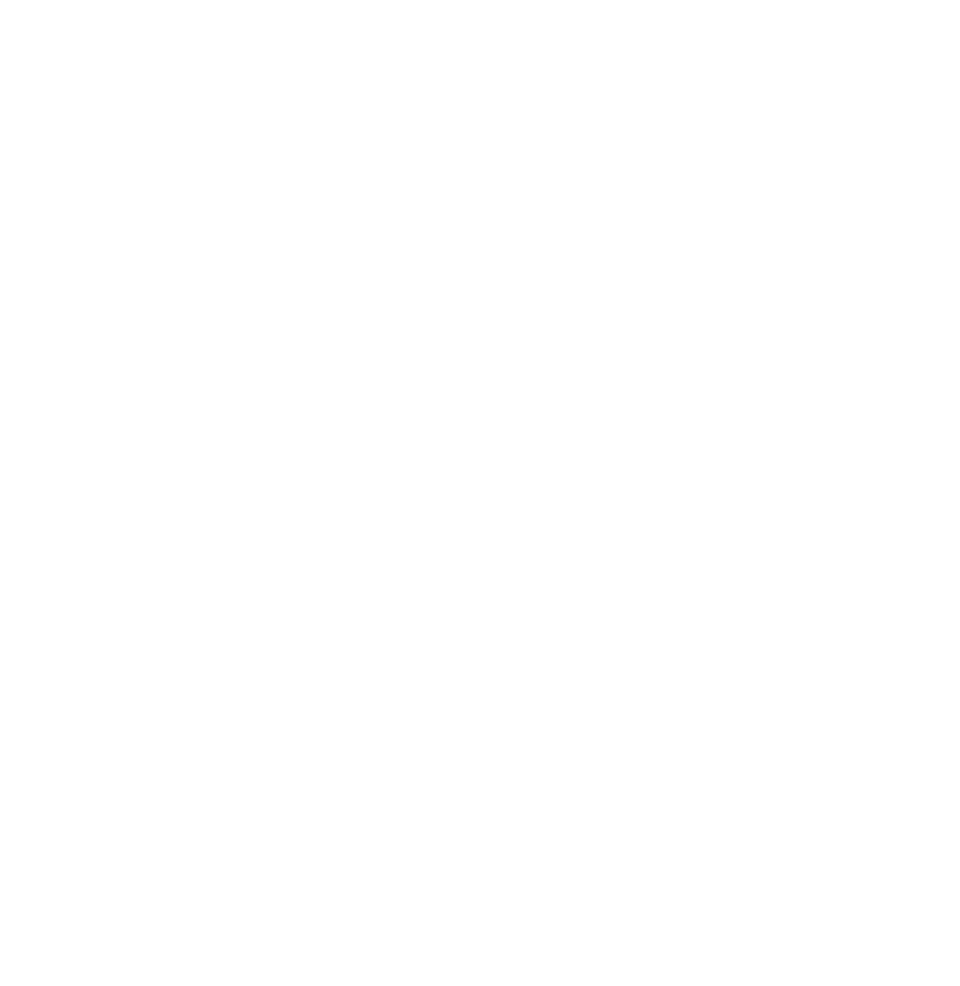
Hydraulic press brake 80/2000
The second press brake built for Gaggio Tech s.r.l., is 80 t with a table length of 2100 mm.
The open-height is 500 mm, with a Y-axis stroke of 300 mm, and the work area has LED lighting.
It was configured similarly to the 30-1250:
- Next Design
- E-Reflex Deformation Compensation System
- ECO energy-saving package
- 5-axis (X-R-Z1-Z2-X6) CNC-controlled backgauge
- Additional stop on a backgauge reference
- Gasparini AirSlide upper pneumatic clamping of 110 mm height for European type tools
- DSP-AP laser safety system with PLC
- Standard foot pedal
- Ready for Tele-Link remote assistance
- CNC Delem DA-69T
- Software offline Delem Profile-T 3D
- Industry 4.0 Package
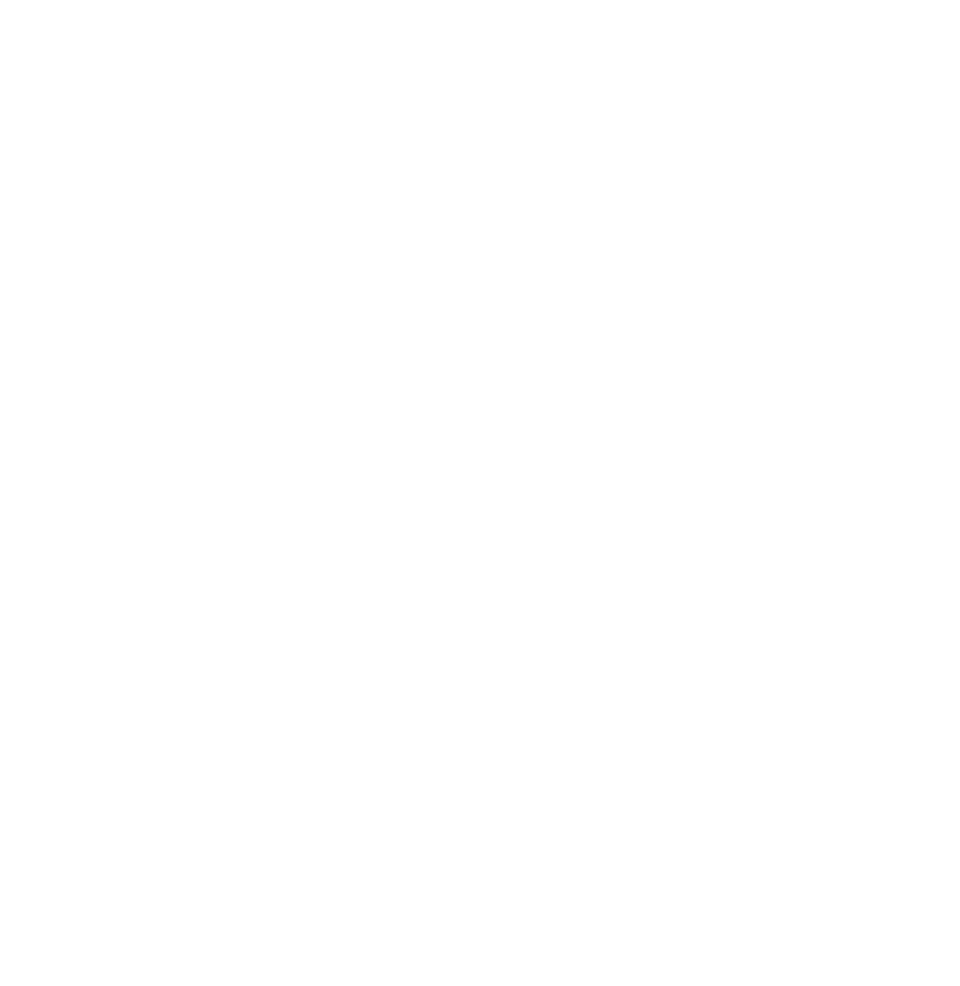
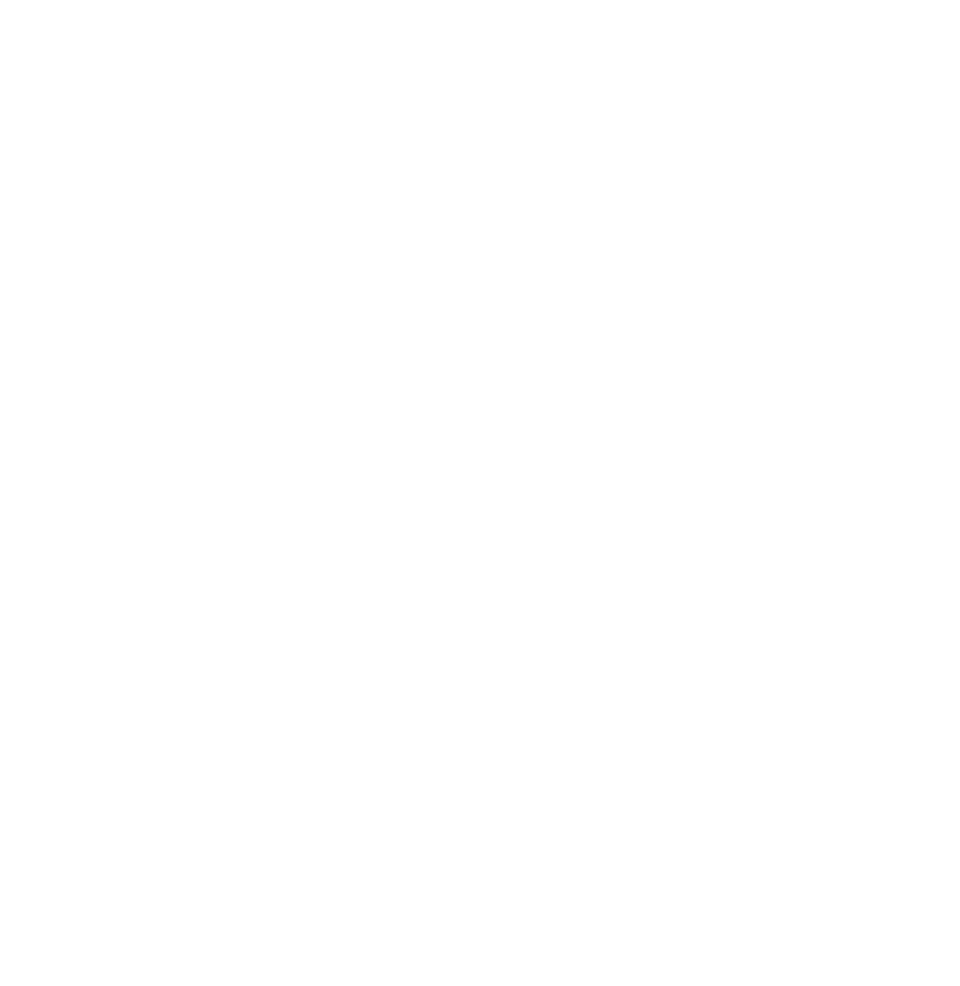
This press brake is characterised by the addition of two retractable sheet supports in the backgauge. These are polyethylene profiles that support even the thinnest sheets without scratching their surfaces.
In addition, unlike the first press brake, it has been equipped with two sliding front supports, adjustable in height and mounted on a linear guide, with a tool tray. They can be easily disengaged from the rail if required, and thanks to their low weight they can be moved with very little effort. The shelf measures 600 x 140 mm, is covered with scratch-resistant polyethylene profiles and can support up to 500 kg.
The other element in which this machine differs from the 30-1250 is the manual lower clamping.
Hydraulic press brake 165/3000
The third press brake built for Gaggio Tech s.r.l. is 165 t with a table length of 3100 mm.
The open-height is 500 mm, with a Y-axis travel of 300 mm.
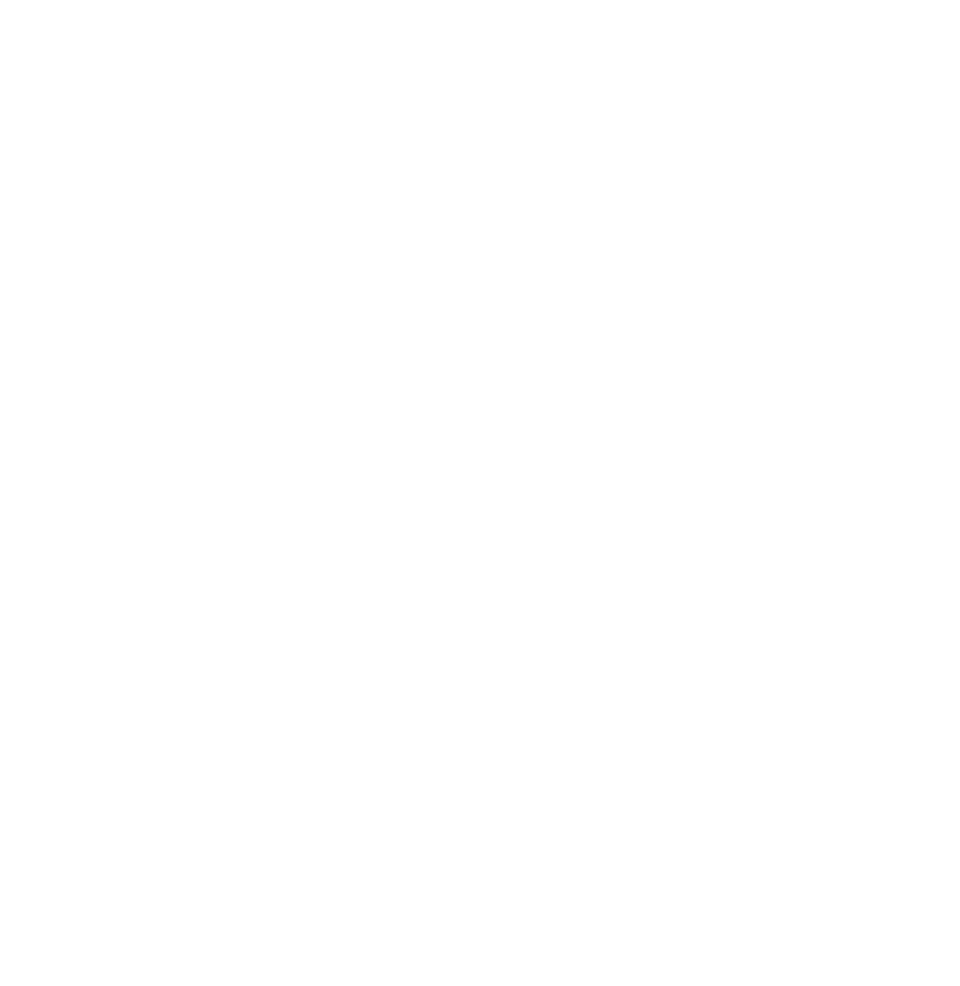
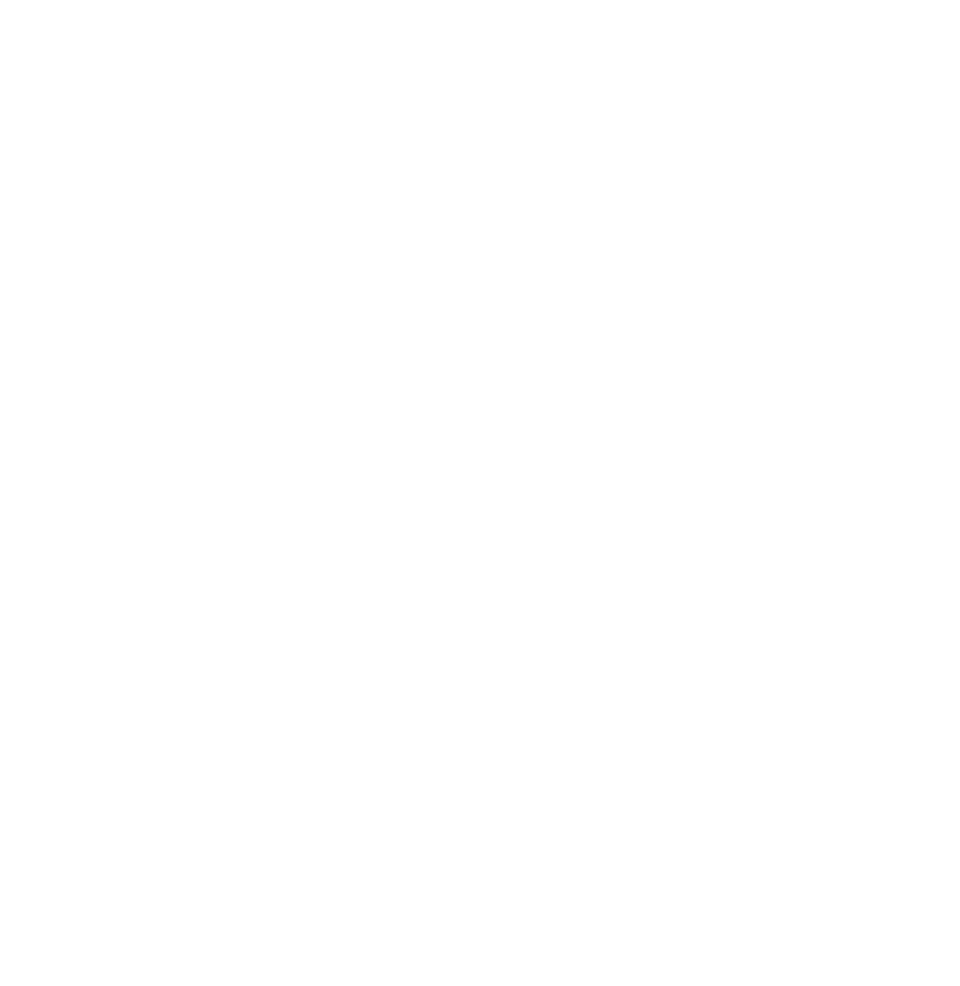
For almost all the systems with which it is made, it has the same characteristics as the 30-1250 and 80-2000:
- Next Design
- E-Reflex Deformation Compensation System
- ECO energy-saving package
- 5-axis (X-R-Z1-Z2-X6) CNC-controlled backgauge
- Additional stop on a backgauge reference
- Gasparini AirSlide upper pneumatic clamping of 110 mm height for European type tools
- DSP-AP laser safety system with PLC
- Standard foot pedal
- Ready for Tele-Link remote assistance
- CNC Delem DA-69T
- Software offline Delem Profile-T 3D
- Industry 4.0 Package
- LED lighting of the work area
As with the 80-2000, this third press brake was designed and built with:
- two retractile back supports in the backgauge
- manual lower clamping
- two sliding front supports
The 165-3000 features the addition of the automatic hydraulic crowning system and the 6-axis (X-R-Z1-Z2-X5-X6) CNC-controlled backgauge.
And it is precisely the addition of the Z1-Z2 axes that allows the rear references to be moved laterally to facilitate the positioning of parts of different lengths or when working by stations. In addition, when the workpiece to be bent has support points on different dimensions, independent travel in the direction of depth with the X6 axis comes into play. In this case, shaped references provide three secure support points, for the correct angle and dimension. By adding this axis, conical bends of up to 75° can be realised.
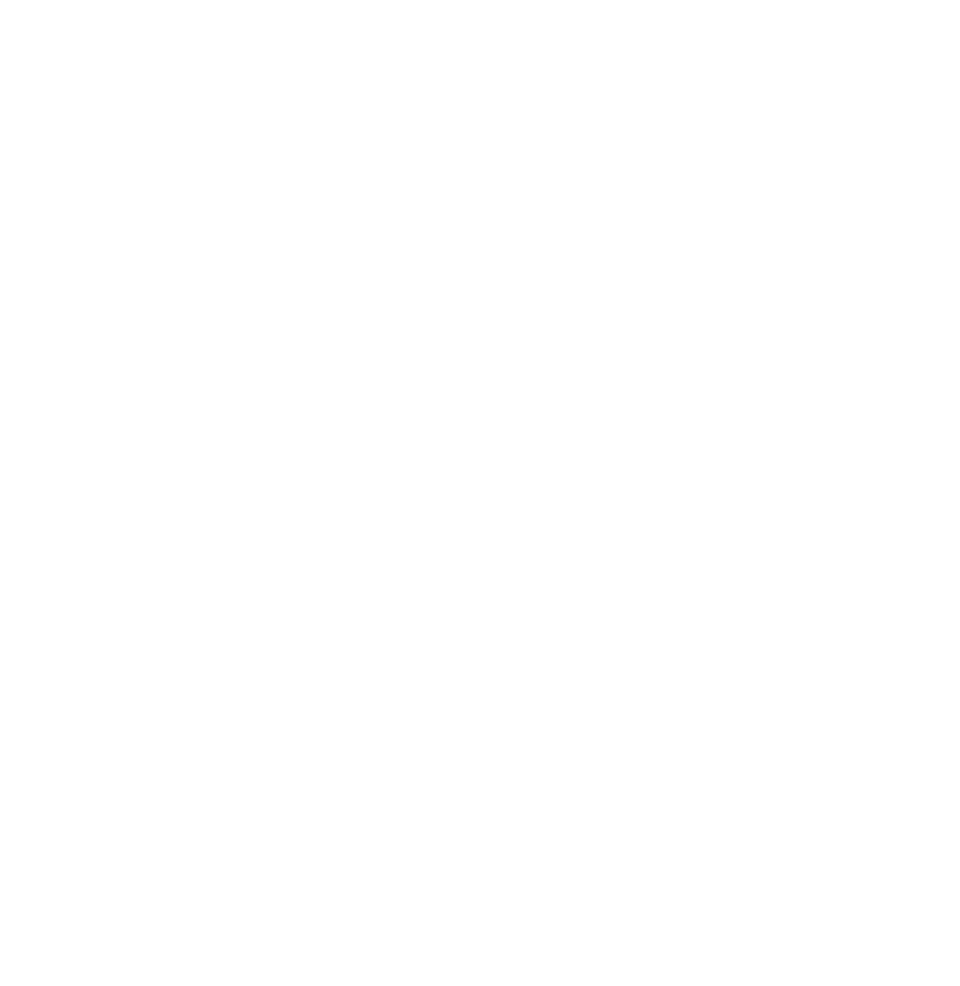