Limited Edition
This press brake has been configured as a Limited Edition version. It features all our most advanced systems, from Gasparini Adaptive Crowning to GPS4. The uniqueness also lies in the design, characterised by the total black finish of beams, casings and every other structural element. The touch of colour is given by the two horizontal lines that outline the work area and represent the identity colours of Gasparini and Blecken (blue and red). All this results in a minimal and elegant impact, for a machine with exceptional performance that is certainly one of a kind.
G4Factory and Artificial Intelligence
The press brake manufactured for the Spanish market is the first to be equipped with both the G4Factory demo package and Artificial Intelligence.
G4Factory is the IoT digital platform developed by Gasparini to monitor production performance and manage maintenance. This ecosystem optimises machine performance through real-time communication between machinery, sensors and software and hardware systems.
The AI readiness will enable the future integration of our innovative Artificial Intelligence system, scheduled for official launch by 2025.
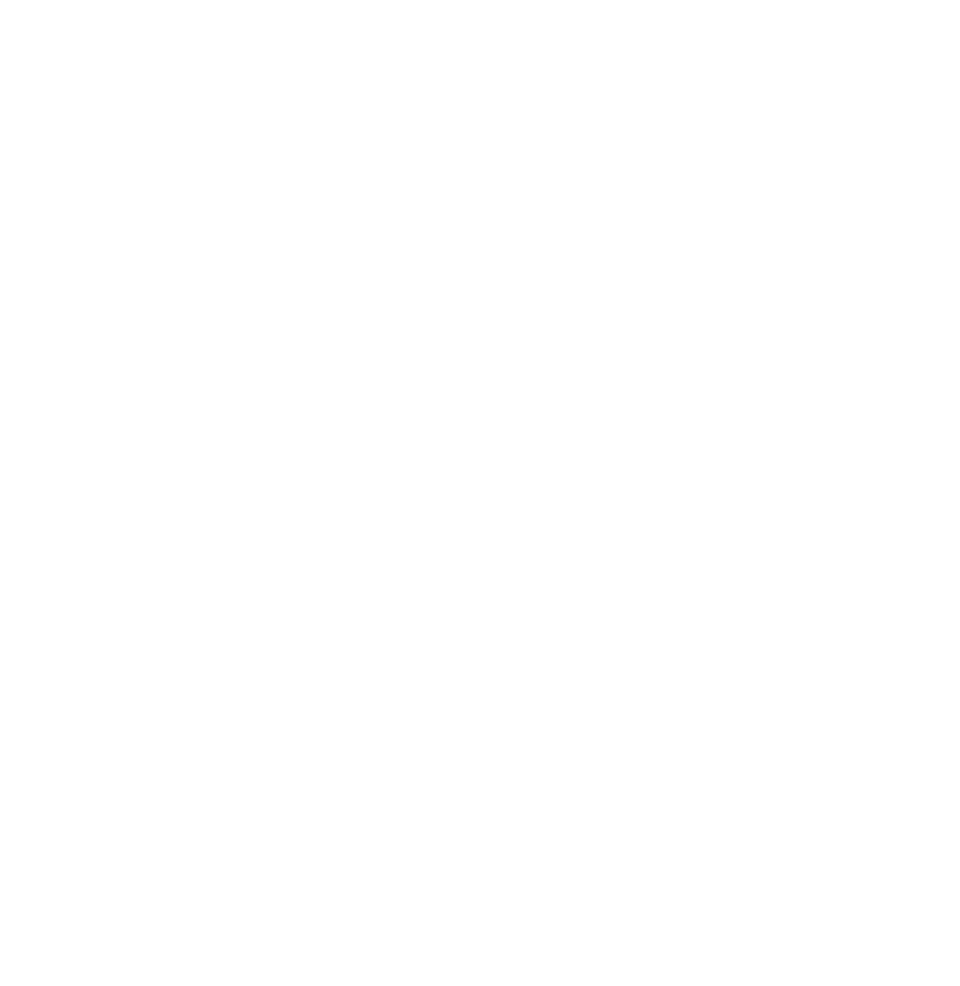
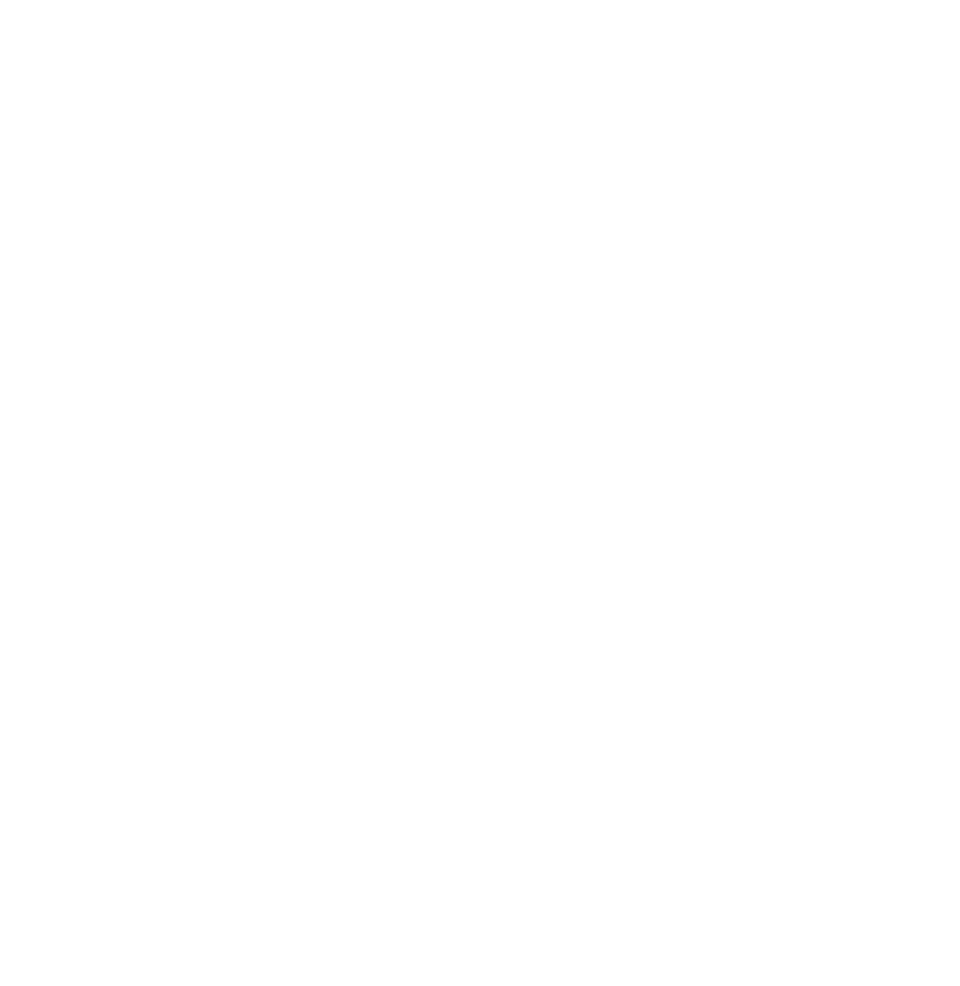
Gasparini Adaptive Crowning System
To compensate for beam bending in real time during bending, Gasparini uses two high-precision sensors that form the core of its Adaptive Bending System.
The first sensor monitors the deformation of the upper beam from the beginning of the bending process. The CNC then controls the pistons positioned in the lower beam, adjusting their action until the data from the second sensor matches that of the first.
This process ensures that the two beams remain perfectly parallel, offering flawless control over the bending angle, with consistent accuracy and repeatability, regardless of the type of material.
There is no need to enter any manual values: the machine autonomously acquires data from its sensors, reacting optimally even when materials change from one workpiece to another.
E-Reflex Deformation Compensation System
The E-Reflex system manages the bending of the press brake structure through a network of sensors distributed in both the machine and the hydraulic system. Error measurements are compared with the position of the beam and oil pressure, allowing the actual punch height to be calculated accurately, regardless of the deformation taking place.
Whether it is variations in length, thickness or positioning of the part, or the properties of the sheet metal, the beam is constantly monitored throughout the bending process, thus ensuring precise and constant control of the bend angle.
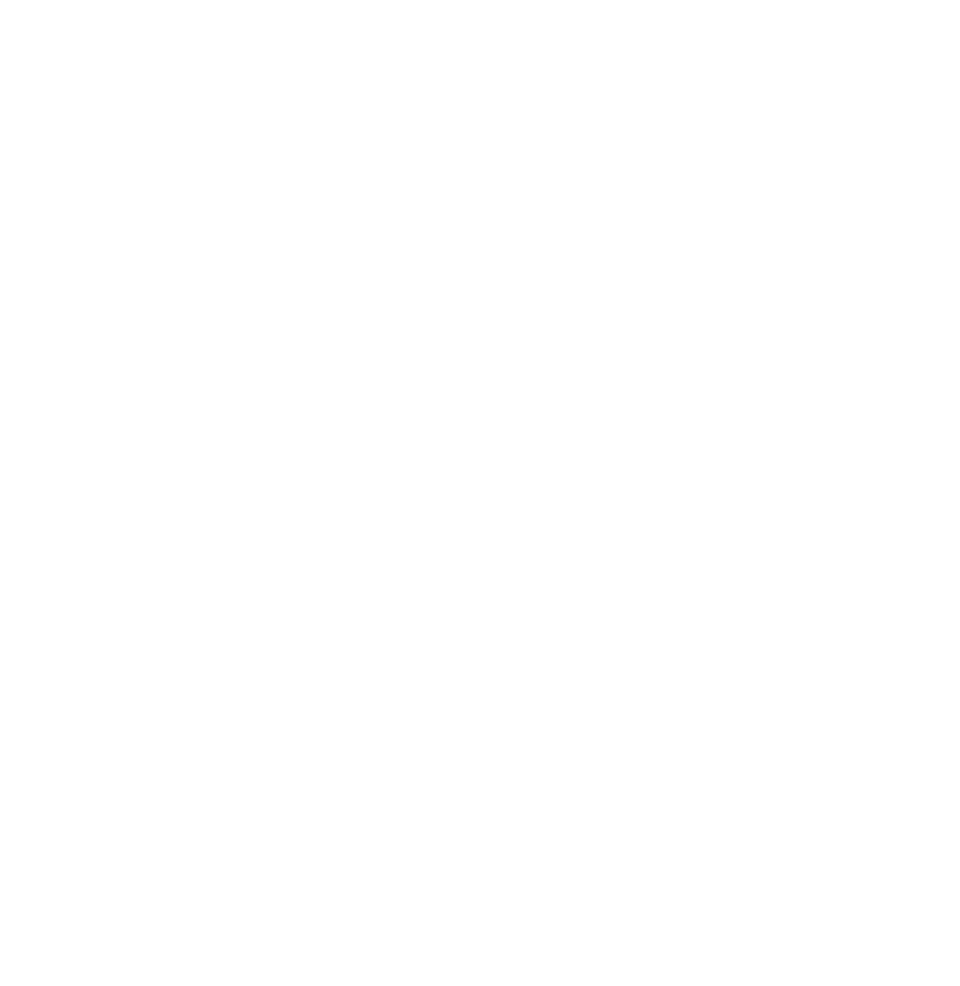
GPS4 angle control system
Springback is an inevitable phenomenon in any material and condition. To achieve perfect folds without the need for testing or manual corrections, a highly accurate angle measurement system is essential.
The GPS4 monitors and corrects the angle during the entire bending process. At the heart of the GPS4 is a double-fork shaped sensor with four points of contact, which measures the bending angle on both sides of the sheet and sends the data to the system for real-time correction.
Programming is extremely simple: there is no need to enter information on thickness, length, material type or bending force. Simply enter the desired angle into the CNC, and the system does the rest. Regardless of variations in the material, the GPS4 ensures that the bend angle is measured and corrected dynamically, ensuring optimal results every time.
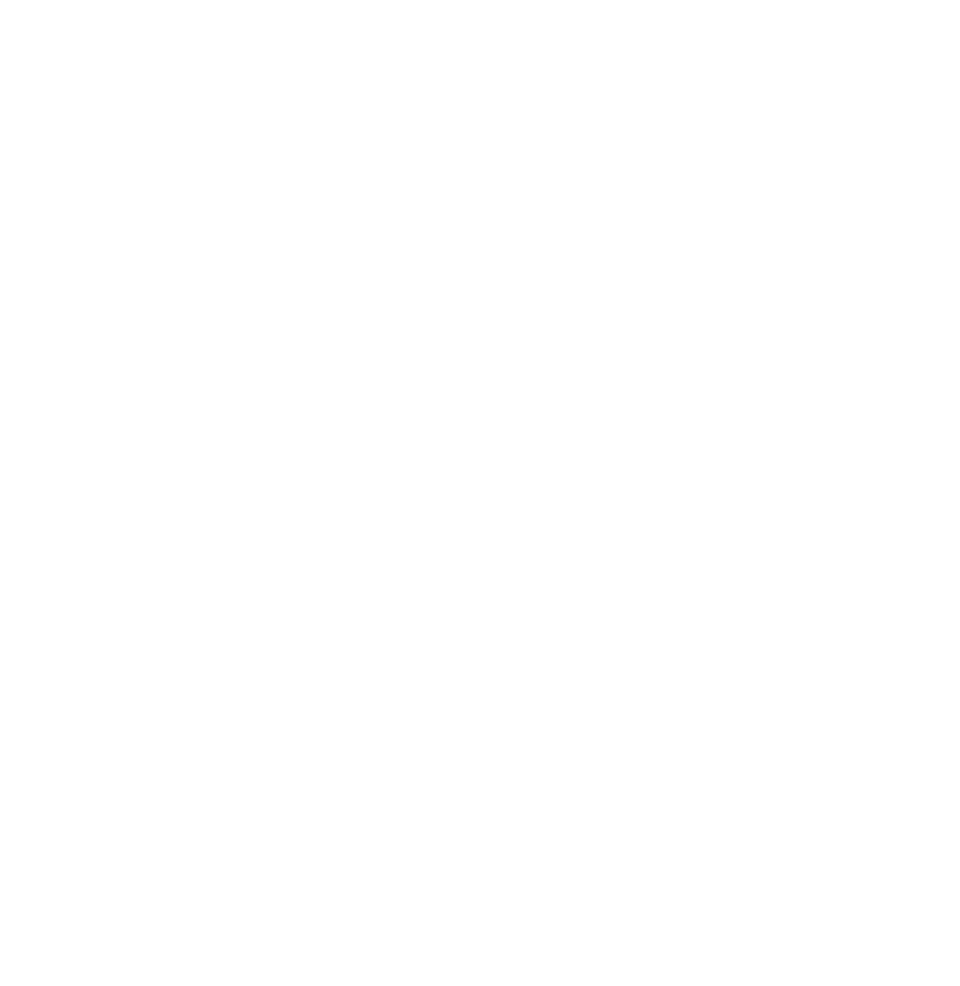
Clamping System
The upper beam is a pneumatic Gasparini AirSlide type with a height of 110 mm for European-type tools.
This compressed air distribution system allows components to be moved along the beam in any position, without the need for connecting hoses or tools. Components can be added or removed in any combination, maintaining system integrity without air leakage.
Furthermore, the components are self-aligning: the punches are automatically lifted and placed in the correct position. They can be brought closer together thanks to the front centring wedges and support segmented punches, keeping the tools perfectly stable even with the locks open.
Safety system
The safety system is the DSP-AP. Thanks to this device, the speed change point can be lowered to as little as 4 mm from the sheet, allowing the beam to maintain a high speed for longer, reducing the part of the cycle where speed is limited. Compared to conventional systems, DSP-AP saves approximately 1.2 seconds per bending cycle.
The system also features auto-blanking, which automatically recognises boxed or side-walled profiles. In the event of a collision, the supports are designed with the ‘Safe Release’ function, which releases them without damage. A motorised positioning system can be integrated, which automatically adjusts the transmitter and receiver to the correct height according to the tools and working conditions.
Dual monitor: CNC and software
This press brake was equipped with dual monitors.
The first is the Delem DA-66S CNC:
- 24’ high resolution touch screen (16:9)
- 3D visualisation of the bending sequence
- 2D programming
- DXF file import
- 3D visualisation of an offline programme
- Offline software included: Delem Profile Lite SL 2D
- Industry 4.0 package
The second monitor, on the other hand, is very ductile, as it can be used to display bending programmes, can be connected to a PC to view drawings or work process status.
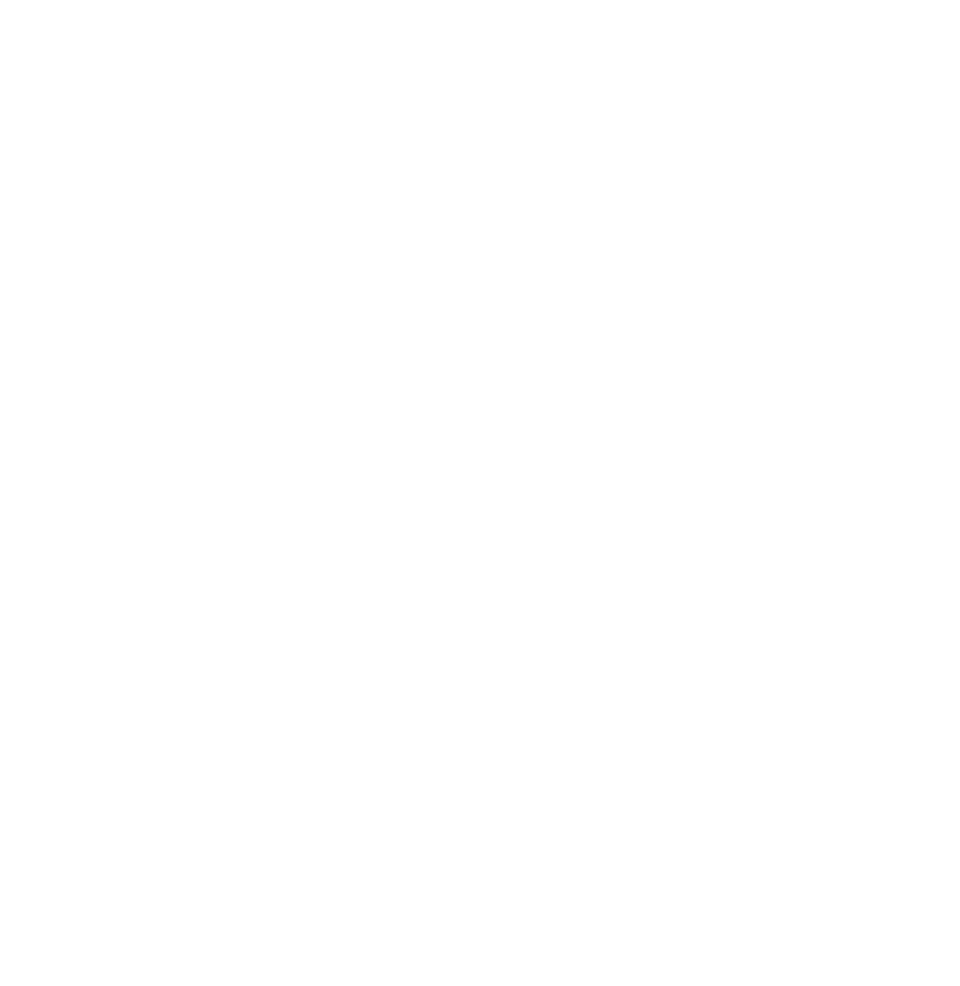
Backgauge
The CNC-controlled 4-axis backgauge (X-R-Z1-Z2) offers enhanced versatility over the traditional two standard axes, thanks to the addition of the Z1 and Z2 axes. These additions allow greater flexibility when machining different parts, allowing the lateral movement of references to easily handle materials of different lengths or work on multiple stations.
In addition, the register includes an anti-collision safety system. In the event of a violent collision, the rear references automatically disengage to prevent damage or misalignment, allowing the operator to reposition them quickly and easily. This ensures greater safety and precision during operations.
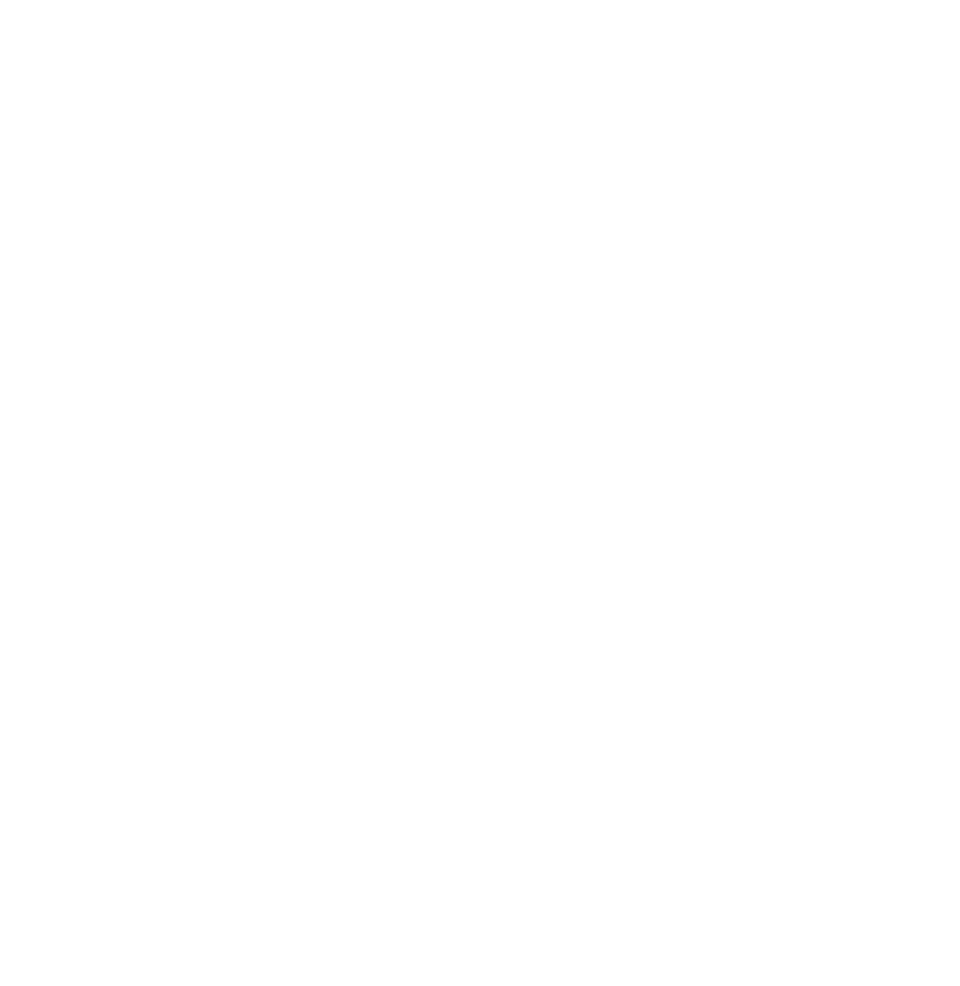
Other systems and accessories
This 165/3000 has been equipped with the ECO energy-saving package, which integrates inverter control of the main motor, optimising the machine’s energy consumption. This system can be combined with Gasparini’s Adaptive Crowning System, which operates in real time thanks to power from the main hydraulic circuit, ensuring precise and uniform bending.
In addition, the bending machine is equipped with:
- 2 sliding front supports
- Gasparini laser safety supports
- 1 standard footpedal
- Provision for Tele-Link remote assistance
- LED lighting of the working area