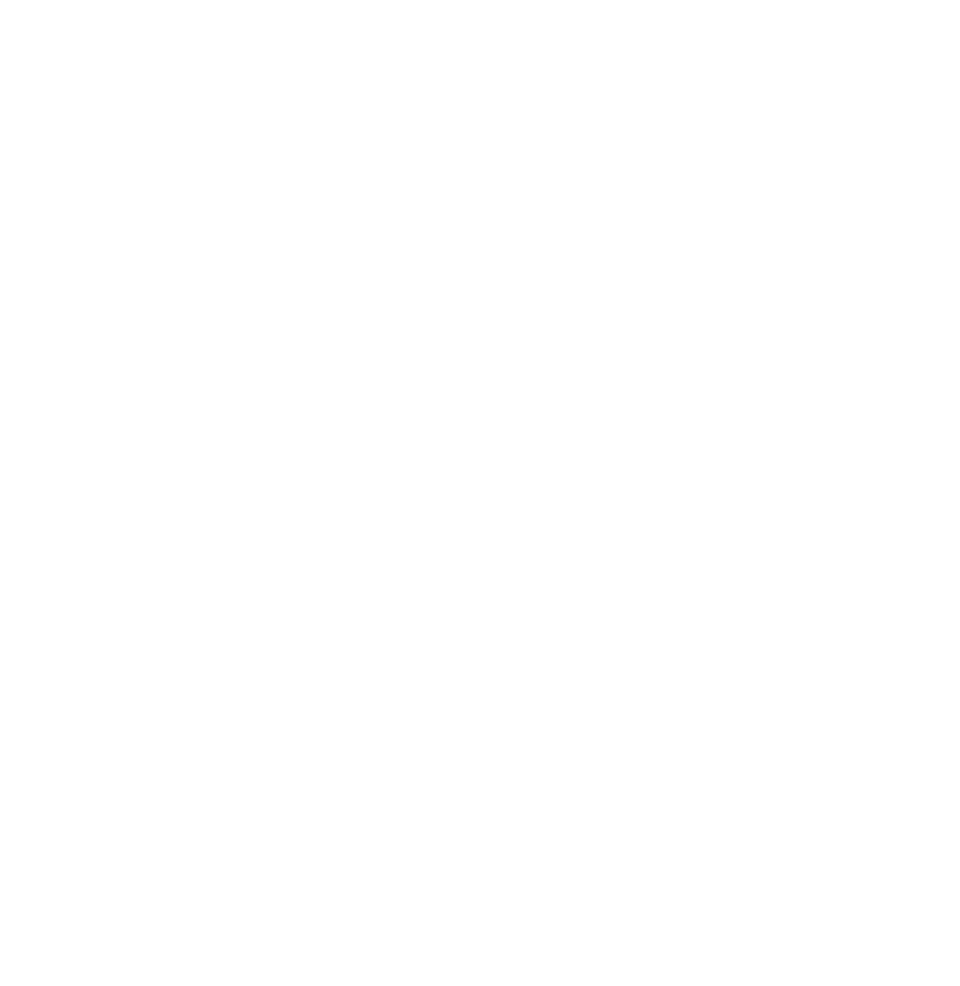
Gasparini adaptive Crowning and E-Reflex deformation compensation system
This press brake features two of our main systems. The first is Gasparini Adaptive Crowning, which monitors the sheet metal bending process via two sensors. The deformation of the upper beam is monitored by the first sensor and the second manages the data to match.
The e-Reflex system manages the bending of the press brake structure through a network of sensors distributed both in the machine and in the hydraulic system. Error measurements are compared with the beam position and oil pressure, allowing the actual height of the punch to be calculated accurately, regardless of the deflections taking place.
CNC and sheet metal lifters
The CNC is the Delem DA-69S (on mobile console), with Delem Profile-S 3D offline software, offering 2D and 3D programming. Full machine configuration in 3D with multiple tool stations providing real feedback on feasibility and product handling. Highly effective control algorithms optimise the machine cycle and minimise set-up times.
The customer also chose to equip the bending machine with the Tele-Link remote service function.
Metal Steel Project’s bending machine has 2 sheet metal lifters with manual R-axis adjustment.
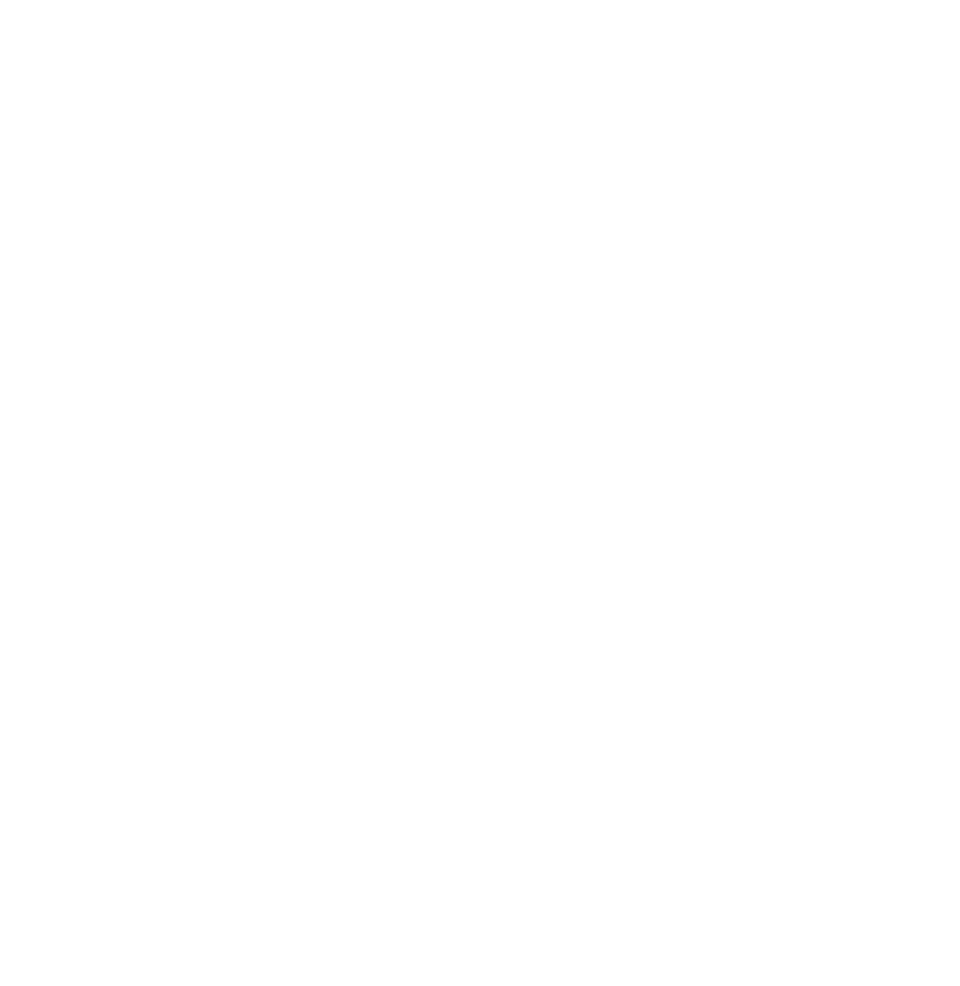
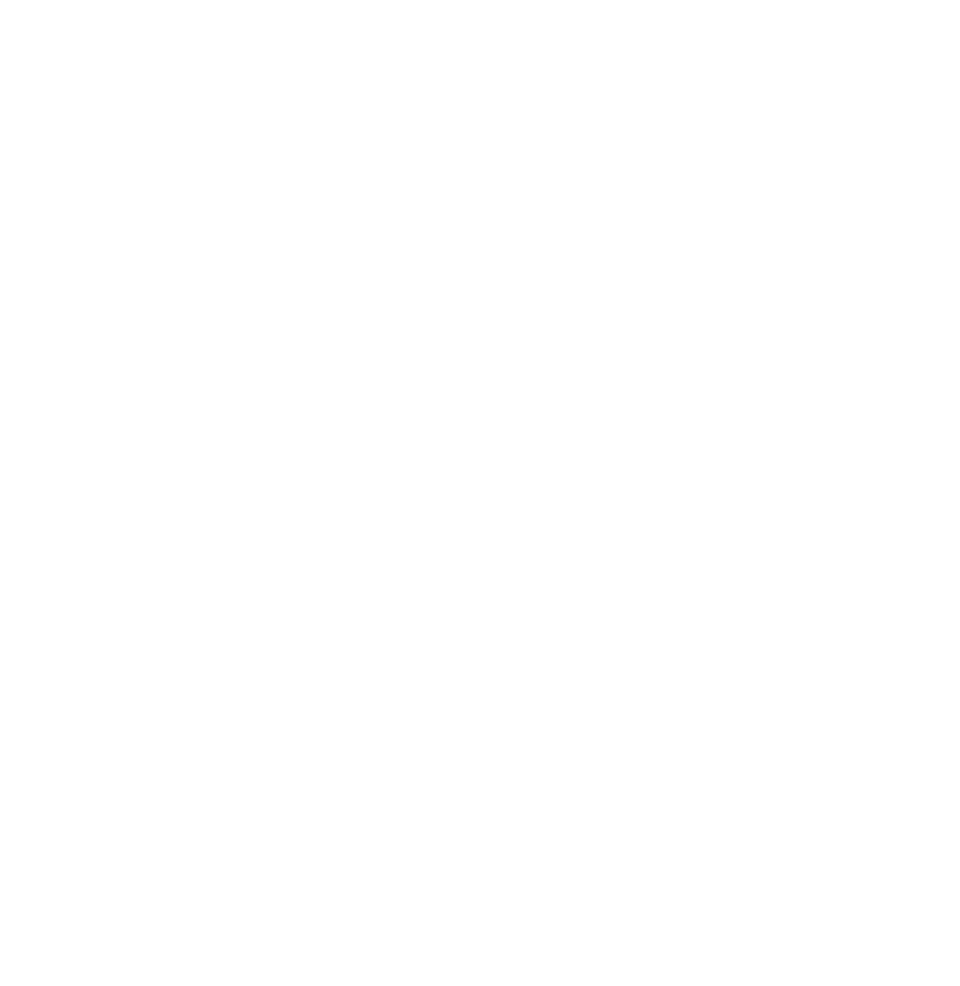
Clamping system
The upper clamp is a pneumatic Gasparini AirSlide type with a height of 110 mm for European-type tools.
This compressed air distribution system allows components to be moved along the beam in any position, without the need for connecting hoses or tools. Components can be added or removed in any combination, maintaining the integrity of the system without air leaks.
The bottom lock is a manual type.
Backgauge
The CNC-controlled 5-axis backgauge (X-R-Z1-Z2-X6) offers enhanced versatility over the traditional two standard axes, thanks to the addition of the Z1 and Z2 axes. These additions allow greater flexibility when machining different parts, allowing the lateral movement of references to easily handle materials of different lengths or work on multiple stations.
A stop and a reference in the backgauge have been added.
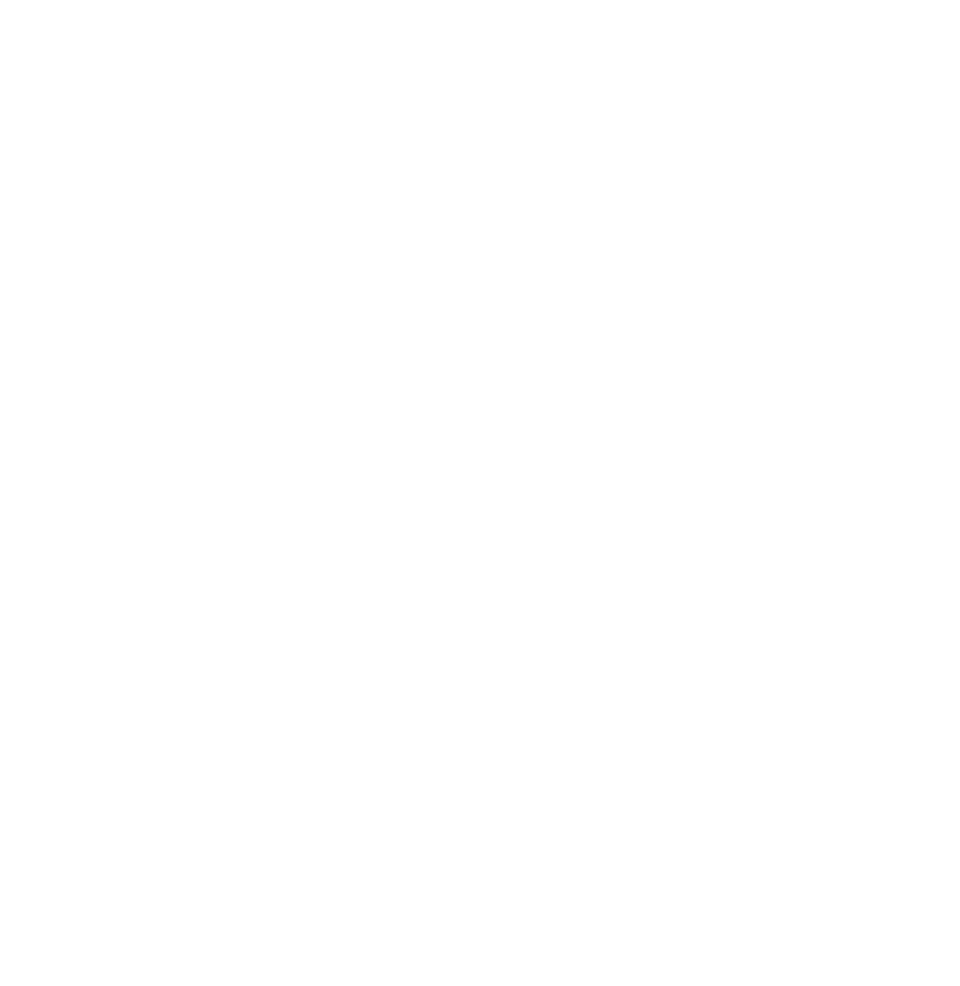
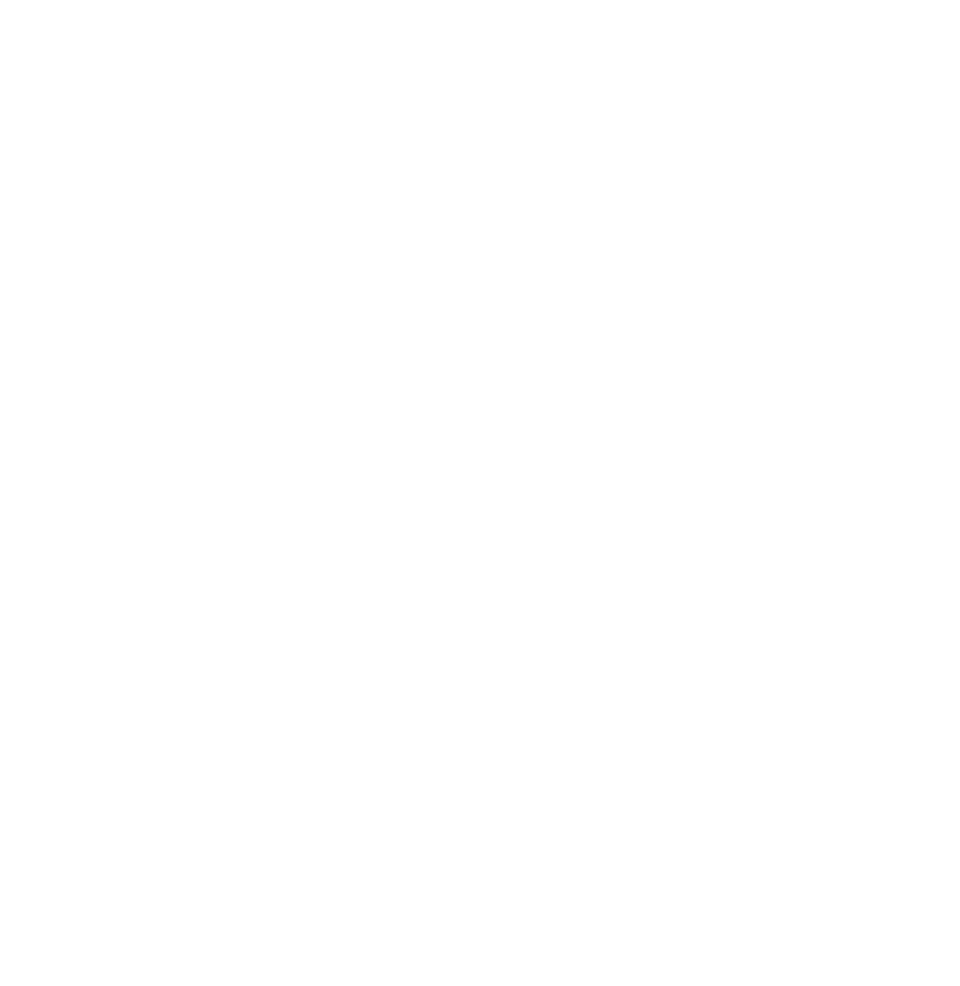
Safety system
The safety system is the DSP-AP. Thanks to this device, the speed change point can be lowered to as little as 4 mm from the sheet, allowing the crosshead to maintain a high speed for longer, reducing the part of the cycle where speed is limited. Compared to conventional systems, DSP-AP saves approximately 1.2 seconds per bending cycle.
The system also features auto-blanking, which automatically recognises boxed or side-walled profiles. In the event of a collision, the supports are designed with the ‘Safe Release’ function, which releases them without damage. A motorised positioning system can be integrated, which automatically adjusts the transmitter and receiver to the correct height according to the tools and working conditions.
Other accessories
This press brake also features the Industry 4.0 package and LED lighting of the work area.
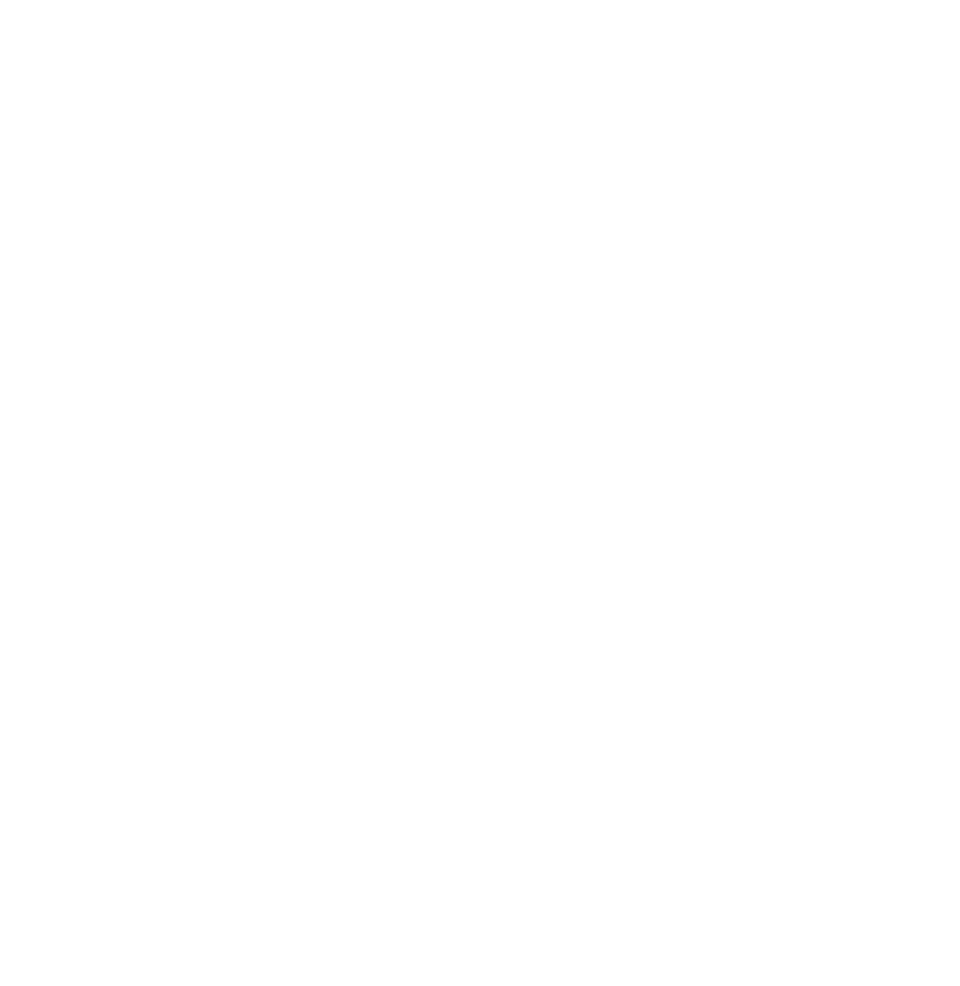