Angle control systems
This 225/4000 incorporates Gasparini’s Adaptive Crowning System and E-Reflex compensation technology, ensuring high quality, precision and repeatable results in the bending process. The bending system ensures that the two beams remain perfectly parallel, allowing total control of the bending angle. At the same time, E-Reflex monitors structural bending via a network of sensors located in the press brake and hydraulic system.
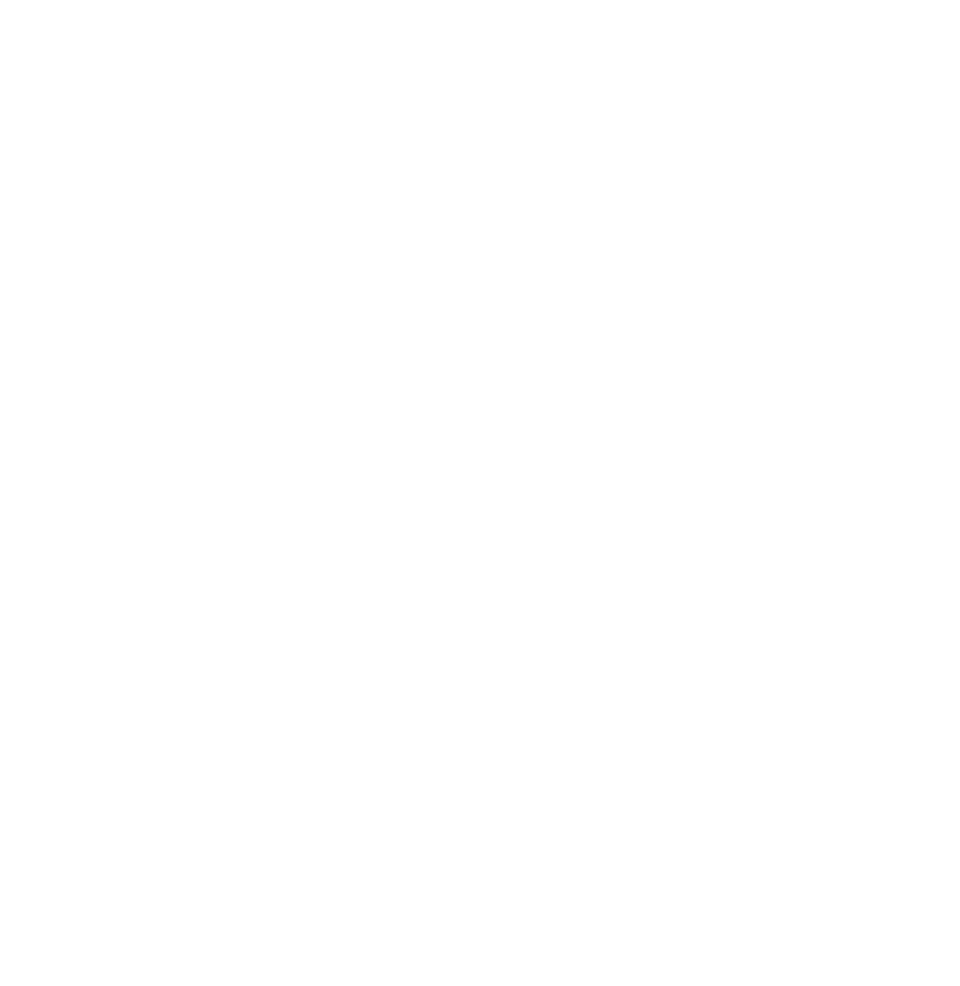
Clamping system
For tool management this bending machine consists of:
Gasparini AirSlide upper pneumatic clamping unit 110 mm high for European-type tools
Gasparini lower pneumatic clamping unit
Want to know more? Discover our clamping systems here.
Backgauge
The backgauge is 5-axis (X-R-Z1-Z2-X6) CNC-controlled, and has been implemented with an additional stop and reference.
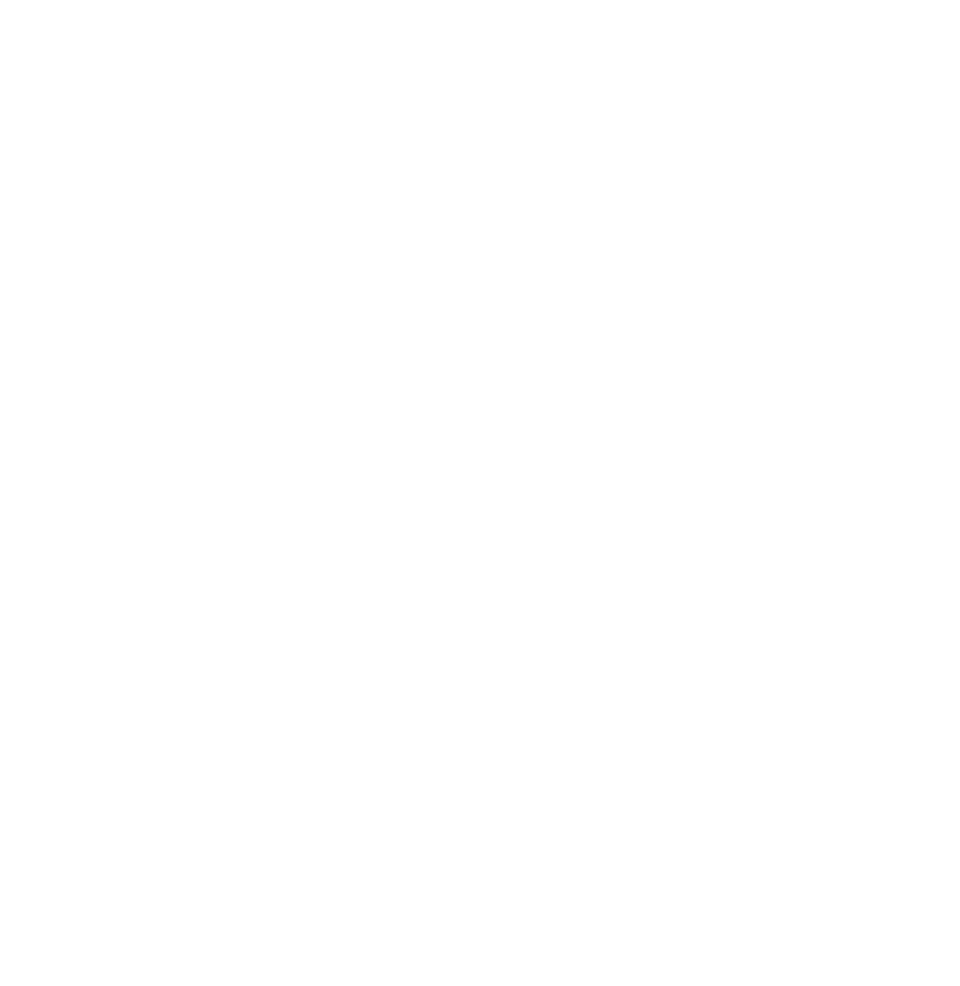
CNC and software
The machine was equipped with the Delem DA-69S CNC with Delem Profile-S 3D offline software.
The DA-69S offers 2D and 3D programming including automatic bend sequence calculation and collision detection. Full machine configuration in 3D with multiple tool stations providing real feedback on feasibility and product handling. Highly effective control algorithms optimise the machine cycle and minimise set-up times.
The customer also chose to set up the press brake with the Tele-Link remote service function.
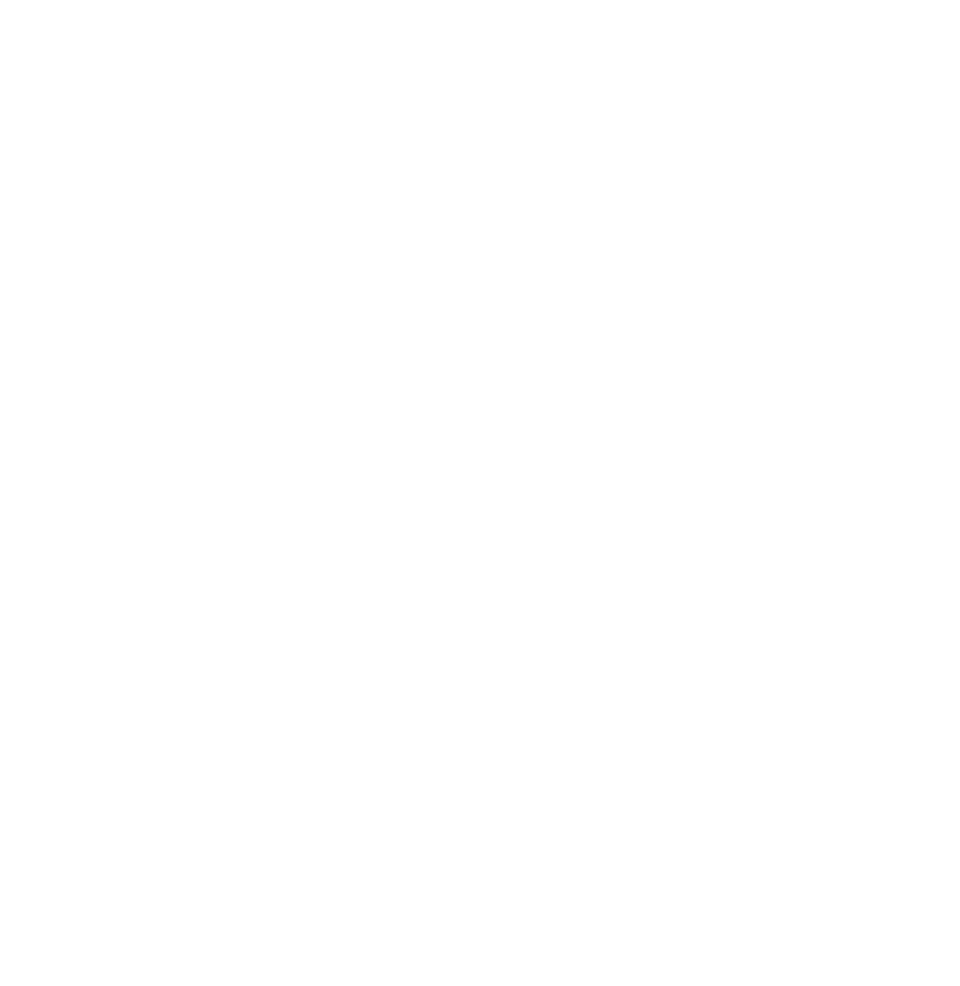
Security System
The IRIS laser safety system with PLC uses a two-dimensional die sensor to read the entire area around the punch tip.
With an optical resolution of only 2 mm, it allows the speed change point to be set at 0 mm from the sheet. The cycle time is greatly reduced: up to 3 seconds saved per bend. The maximum distance between systems is 15 m.
Other systems and accessories
In addition, the following were installed:
- 1 standard footplate
- 2 sliding front supports
- LED lighting of the working area
- ECO energy-saving package
- Industry 4.0 package