The customer's need
The customer needed a press brake capable of performing a double flattening during the bending sequence, without having to reconfigure the machine between operations. The objective was to reduce set-up times and optimise the production flow, while maintaining high accuracy and operator safety.
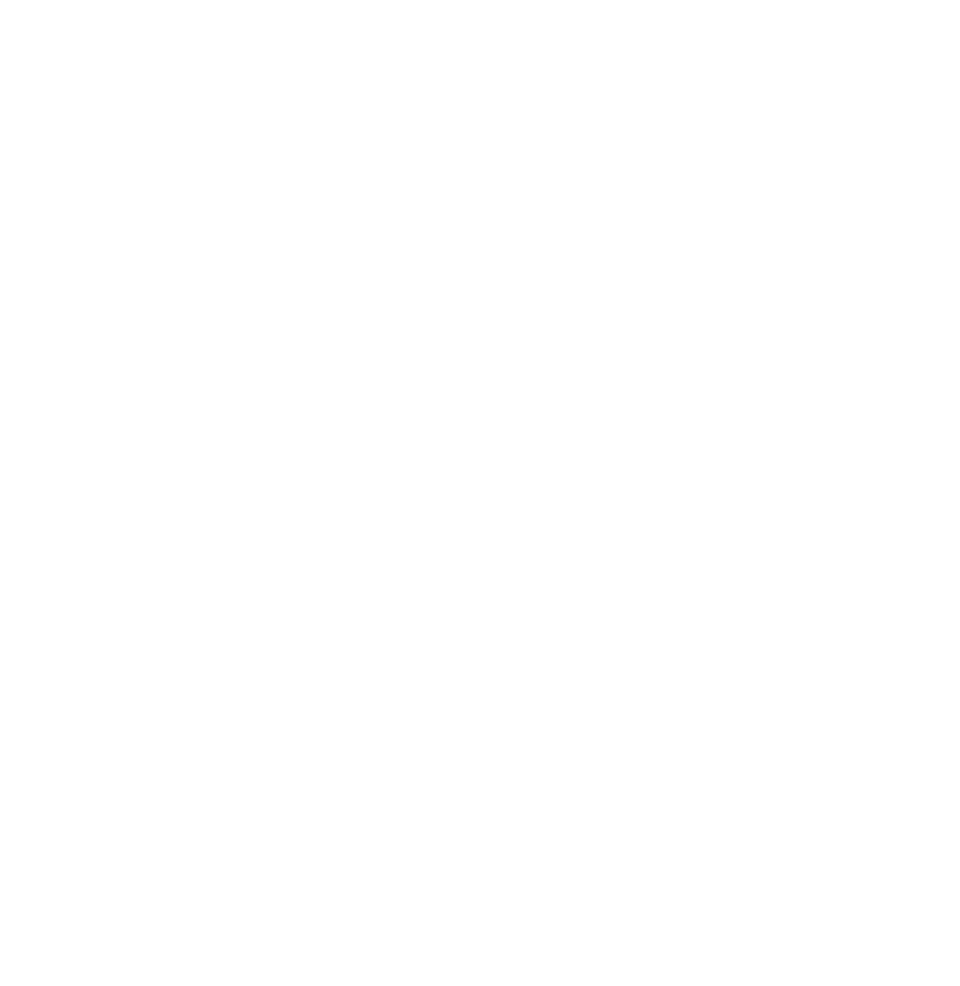
The Gasparini solution
To meet this need, Gasparini designed an XP165/3000 press brake, equipped with an automated tool change system and an automatically positioned multi-pocket die, allowing the entire bending and flattening cycle to be performed in a single set-up.
Key machine features
✔ Automated changeover for double machining without interruption
Two-position top tool with automated changeover → Allows rapid switching between the two operations without the need for manual intervention.
Automatically positioning multi-position matrix with bending-flattening function → Dynamically adapts the configuration to perform both operations precisely and efficiently.
✔ Safety and operational versatility
Adaptive safety photocell → Automatically adapts to both punch positions, providing continuous protection without interfering with productivity.
✔ Maximum ergonomics and practicality for the operator
Customised front table → Designed to facilitate workpiece positioning, reducing operator fatigue.
Quick coupling system → For fast and safe set-up.
Pneumatic movement and lateral extensions → Allow easier handling of even large workpieces.
Clamping systems
- Manual upper clamping with special attachment
- Punch rotation system with barrier safety system
- Manual lower clamping with special attachment
- Die handling system (5 die positions) with adjustable wedge bench
Customised front bench details
- 2-position front support with pneumatic activation
- Open table dimensions 3000×3000 mm
- Closed table (manually foldable) to 2500×3000 mm
Other systems and accessories
- IRIS laser safety system with PLC
- Support for IRIS laser safety system with 2-position vertical and horizontal positioning
- Delem DA-66S CNC
- Delem Profile Lite SL 2D offline software
- X-R axes with longitudinal references
Achievements
Thanks to this advanced configuration, the customer achieved:
✅ A faster and more continuous bending cycle, without interruptions for tool changes.
✅ Reduced set-up times, improving overall productivity.
✅ Increased operator safety with an adaptive photocell system.
✅ A more ergonomic and fluid process, thanks to the customised front table.
With Gasparini, every detail is designed for maximum efficiency and safety.