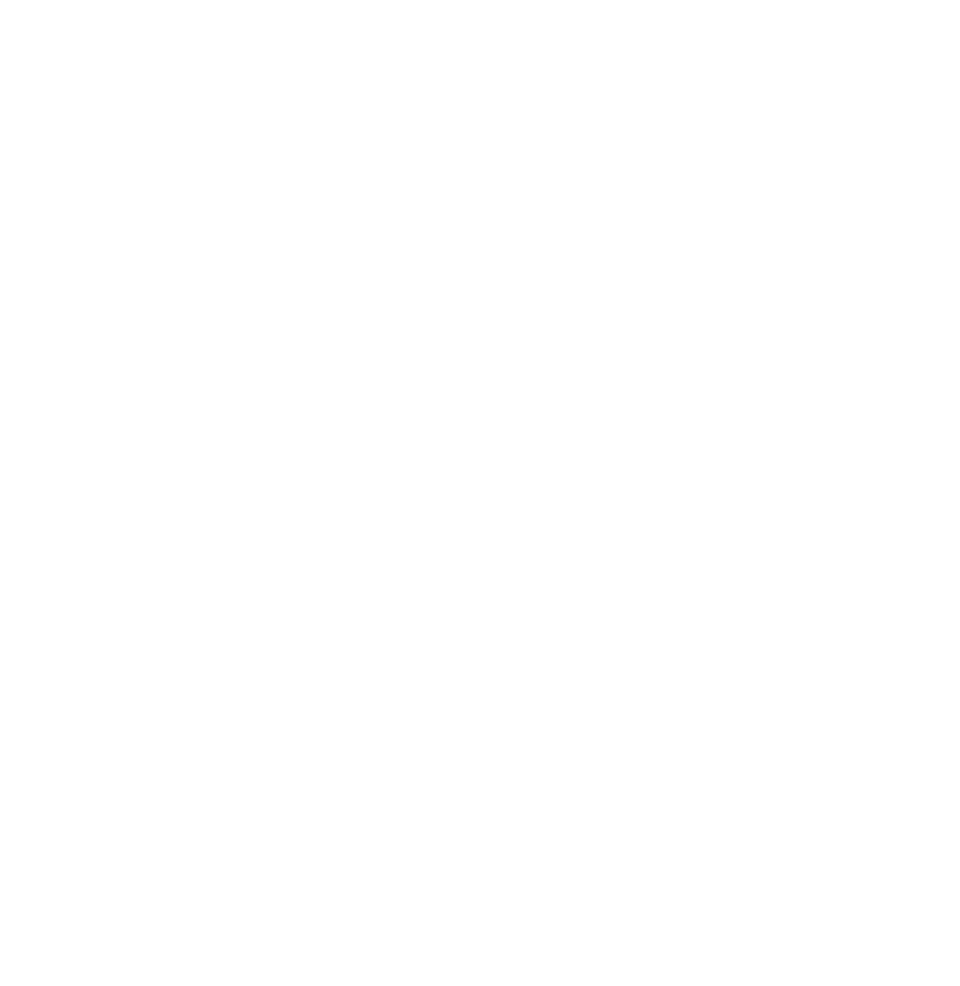
Main features
This press brake comes in the Easy design. The customer chose to equip it with the E-Reflex deformation compensation system and the Gasparini Adaptive Crowning system. The former monitors the bending of the structure thanks to a network of sensors in the machine and hydraulic system. The error is measured and compared with the position of the beam and oil pressure, allowing the actual height at which the punch is located to be calculated, regardless of deformations. The second, ensures that the two beams remain perfectly parallel, allowing total control of the bending angle.
GPS4 angle control system
The GPS4 system, installed on this X-press, ensures constant monitoring and correction of the bend angle throughout the entire processing cycle. At the heart of its operation is a double-forked shaped sensor with four sensing points that simultaneously measure the angle on both sides of the sheet. This data is sent to the system, which uses it to make immediate corrections.
Set-up is extremely intuitive: there is no need to specify details of thickness, length, material type or bending force. Simply enter the desired angle value into the CNC, and the GPS4 takes care of the rest. Even if there are variations in the material, the system automatically measures and corrects the angle, ensuring accurate and uniform bending at all times.
CNC and software
The CNC is the Delem DA-69S, with Delem Profile-S 3D offline software.
The DA-69S offers 2D and 3D programming including automatic bend sequence calculation and collision detection. Full machine configuration in 3D with multiple tool stations providing real feedback on feasibility and product handling. Highly effective control algorithms optimise the machine cycle and minimise set-up times.
The customer also chose to set up the bending machine with the Tele-Link remote service function.
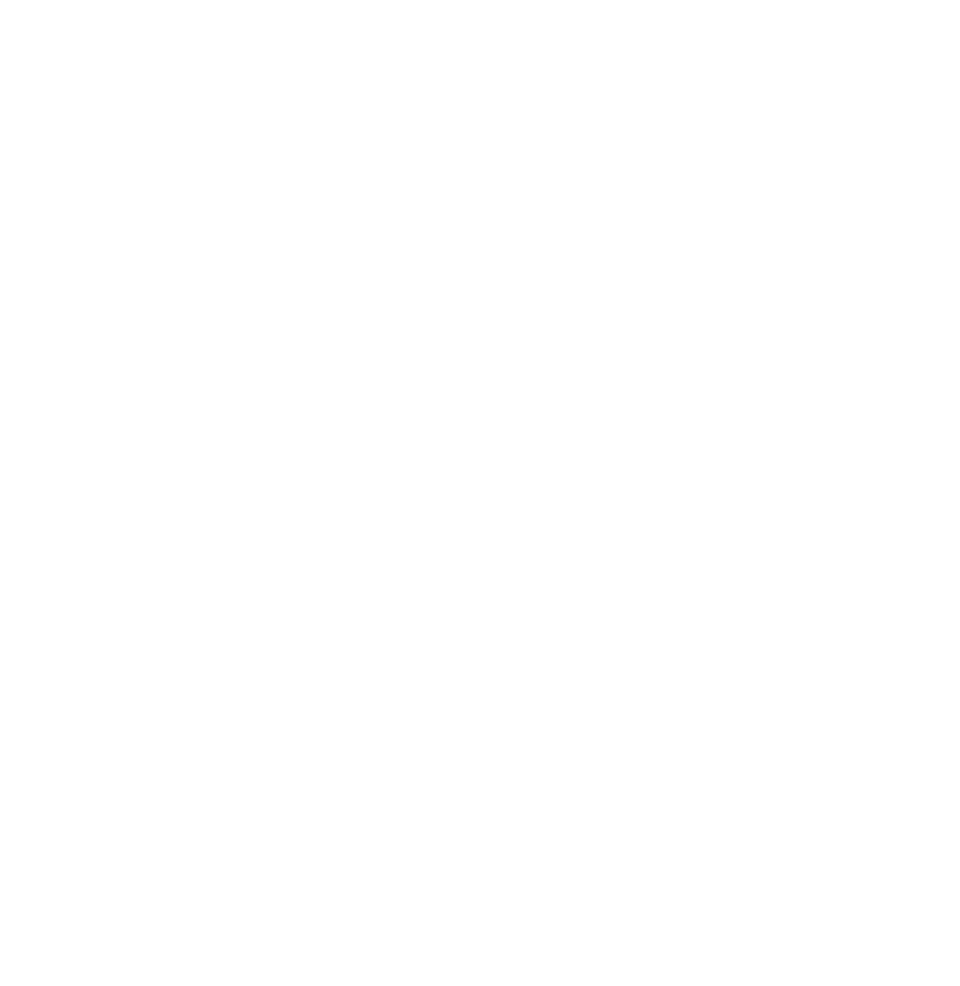
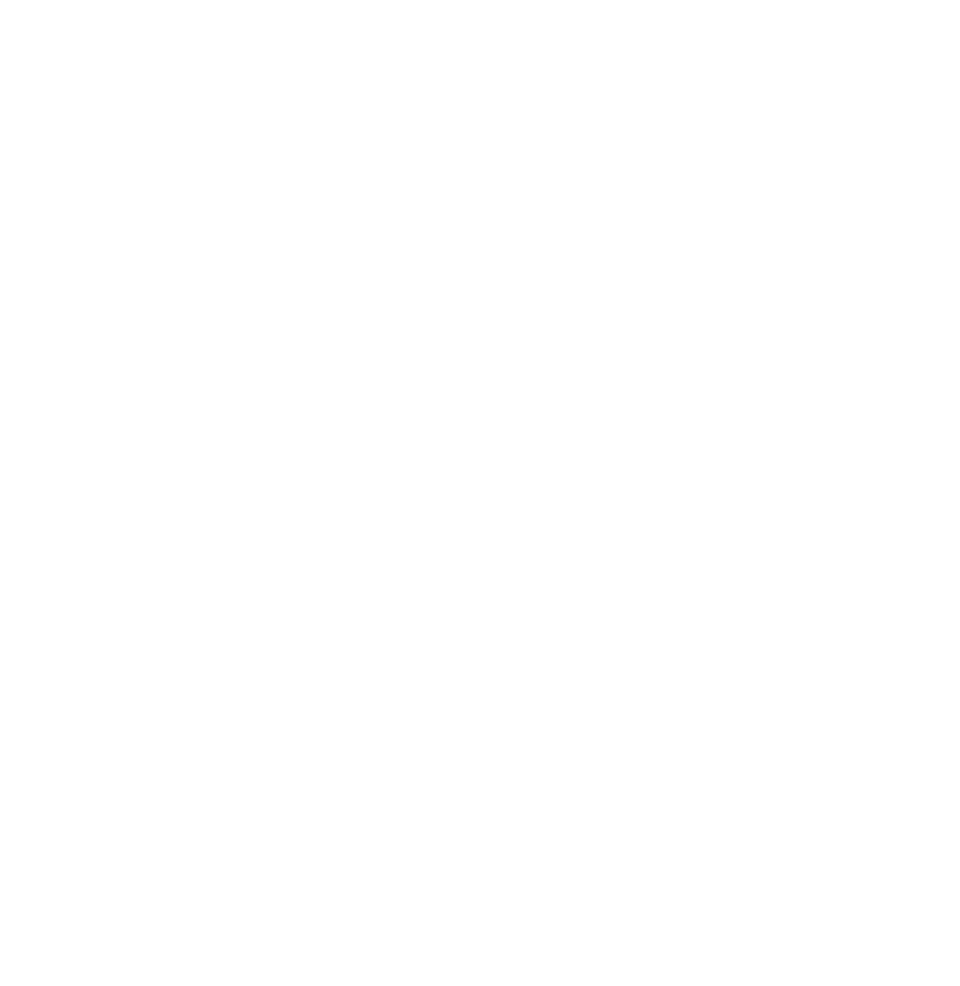
Clamping system
The upper clamp is a 200 mm high pneumatic Gasparini AirSlide type for European type tools.
This compressed air distribution system allows components to be moved along the beam in any position, without connecting pipes or tools. Components can be added or removed in any combination, without air leakage.
Furthermore, the components are self-aligning: the punches are automatically lifted and placed in the correct position. They can be brought closer together thanks to the front centring wedges and support segmented punches, keeping the tools perfectly stable even with the locks open.
Backgauge
The CNC-controlled 5-axis backgauge (X-R-Z1-Z2-X6) offers enhanced versatility over the traditional two standard axes, thanks to the addition of the Z1 and Z2 axes. These additions allow greater flexibility when machining different parts, allowing the lateral movement of references to easily handle materials of different lengths or work on multiple stations.
It also has an additional stop on a register reference, and 2 retractile back supports.
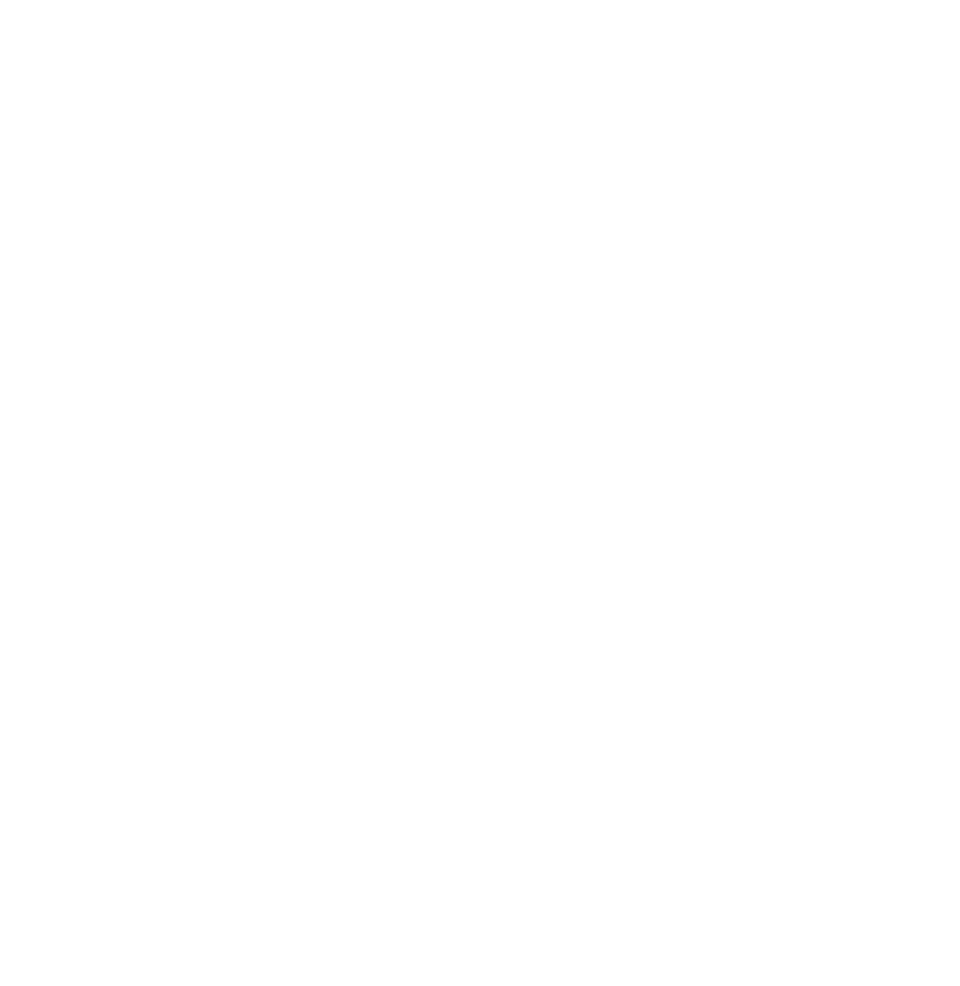
Other systems and accessories
This folder also features:
- 2 sliding front supports
- DSP-AP laser safety system with PLC
- 1 standard foot pedal
- LED lighting of the working area
- Industry 4.0 package