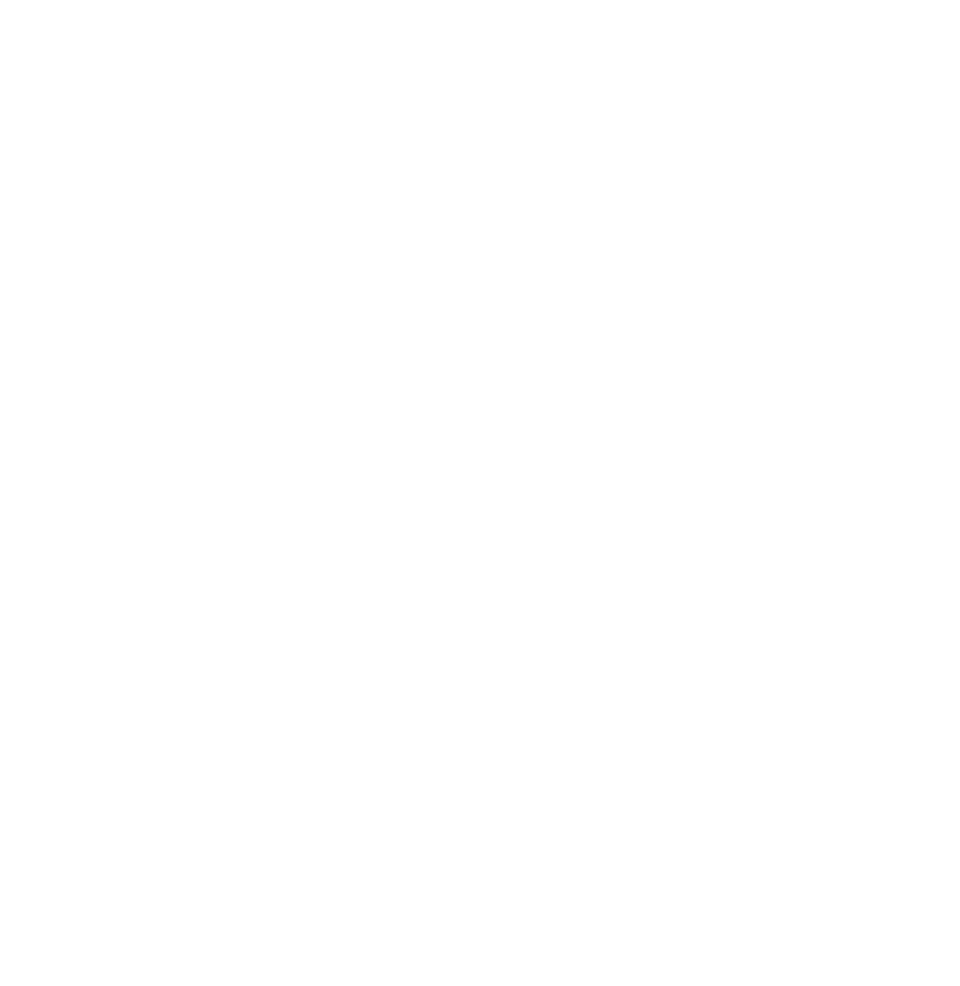
Robotised cell
We developed a press brake that can be integrated with the customer’s production facility, based on their specific needs. In cooperation with Starmatik, we produced an automated yet flexible and reconfigurable bending system that reduces waste and accurately determines production time and costs.
By accessing vital machine information, it is possible to monitor material characteristics, processing steps, and reduce the risk of breakdowns.
E-Reflex Deformation Compensation System
It features the E-Reflex deformation compensation system, which monitors the bending of the structure by means of a network of sensors in the press brake and hydraulic system. The error is measured and compared with the beam position and oil pressure. We can thus calculate the actual height at which the punch is located, regardless of deformations.
GPS4 angle control system
The customer chose to equip this press brake with the GPS4 angle control system for 2 sectors, which allows the angle to be controlled and adjusted throughout the bending process.
The heart of the system is the shaped double fork sensor with 4 contact points: this detects, on contact with the material, the bending angle of both sides of the sheet and sends the data to the system to perform the bending.
It has also been implemented with an additional module to manage the measuring device (up to 4 sectors) and GPS4 ‘double-window’ sector (without matrix).
Backgauge
The backgauge is 4-axis (X-R-Z1-Z2) CNC-controlled, which in addition to the two standard axes also features the Z1 and Z2 axes. It is characterised by the addition of a stop on one of the references.
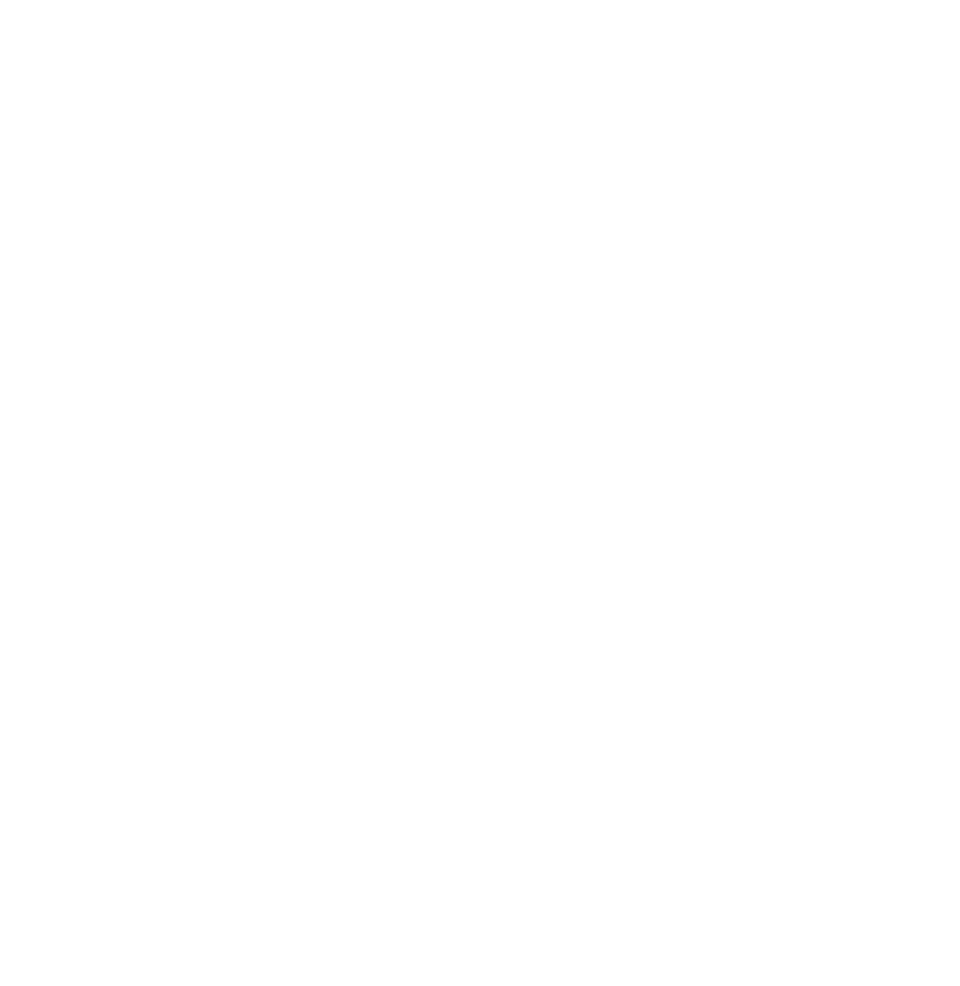
Safety system
The safety device implemented is the DSP-AP Laser, which provides a reduction in speed and a decrease in cycle time. The system emits a visible laser beam that meets EN12622 standards and ensures the operator is protected from any danger of crushing between the die and the punch.
Other systems and configurations
This X-press 115/3000 folder has been equipped with:
- ECO+ energy-saving system
- 1 standard footpedal
- Electrical interface for robot-operator configuration
- Interface with third-party offline software
- Heat exchanger
- Provision for Tele-Link remote assistance
- Delem DA-66T CNC
- Delem Profile Lite TL 2D offline software
- LED work area lighting
- Electrical interface for changing robot operation