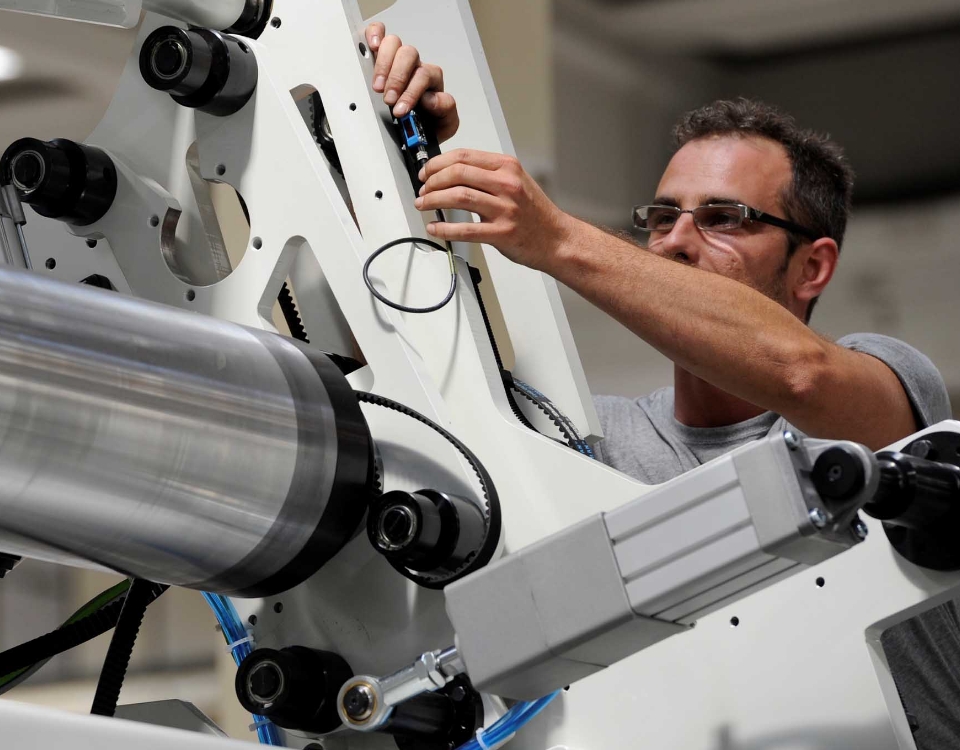
This bending machine is equipped with Gasparini Adaptive Crowning System. To adapt in real time to the bending of the ram, it uses two precision sensors: the first one detects the deformation of the upper ram from the moment bending begins; the CNC drives the pistons in the lower ram until the measurement of the second sensor is equal to that of the first. In this way the two rams are perfectly parallel.
In addition, the machine was equipped with the E-Reflex Deformation Compensation System, which monitors the bending of the structure via a network of sensors in the press brake and hydraulics.
The upper clamping system is hydraulic self-aligning type H-GG and the tool adapters are European type H30-GG with manual clamping and Toolever.
The lower clamping is also hydraulic.
The safety system installed is the DSP-AP Laser, which generates a visible laser beam conforming to EN12622. The beam protects the operator from the danger of crushing between punch and die.
This device allows the speed change point to be lowered by up to 4 mm from the plate.
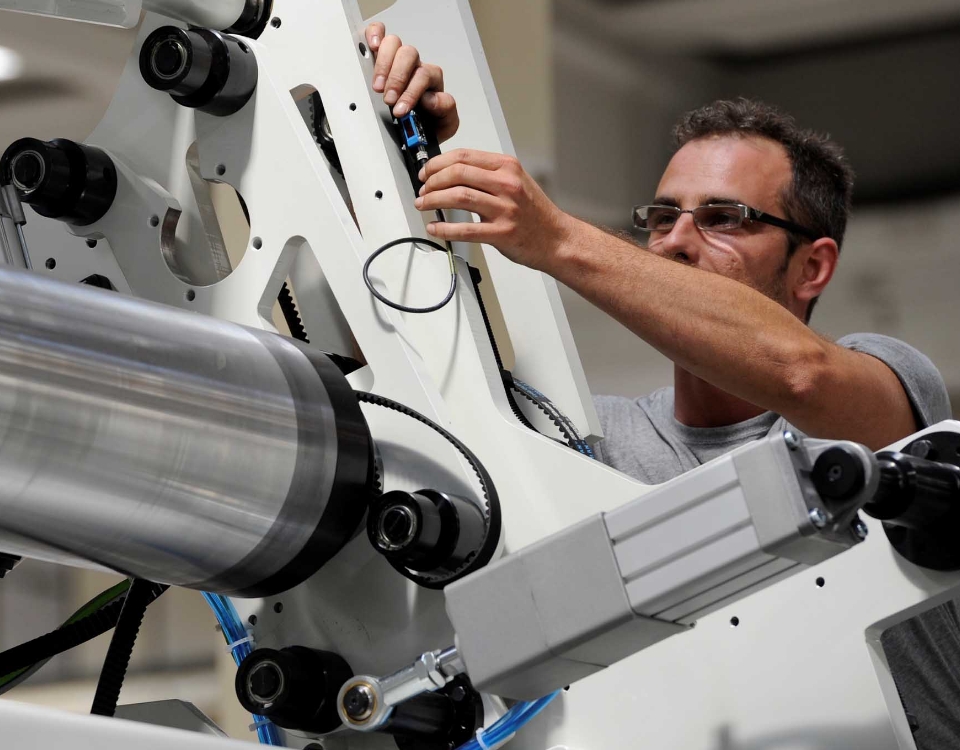
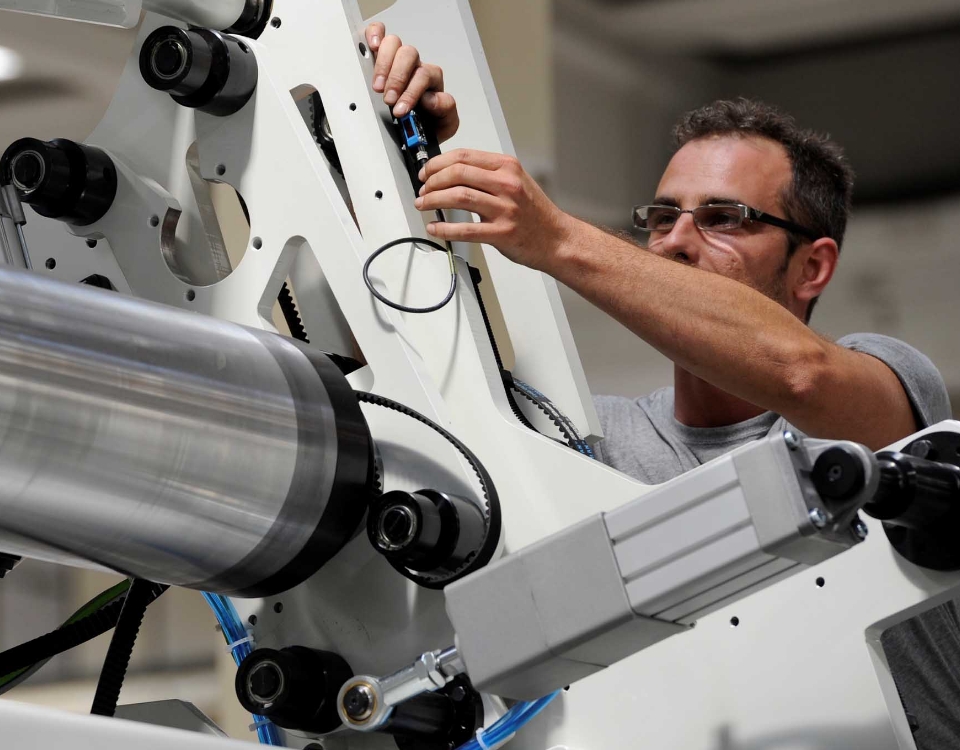
The backgauge is 4-axis (X-R-Z1-Z2) CNC-controlled, and has been implemented with an additional reference to ensure maximum precision for operators during the bending process of specific parts.
The OCVM press brake is equipped with two sheet lifters with manual adjustment of the R-axis. These are two movable sheet metal supports placed at the front of the machine, at the height of the bending line (lower tool). The supports are controlled by the CNC and support the sheet metal during the bending process.
The CNC mounted on a mobile console is the Delem DA-69T with Delem Profile-T 3D offline software. Its user interface allows fast collaboration between programming and production, and also enables 3D programming.
The press brake also features Tele-Link remote assistance and the Industry 4.0 package.
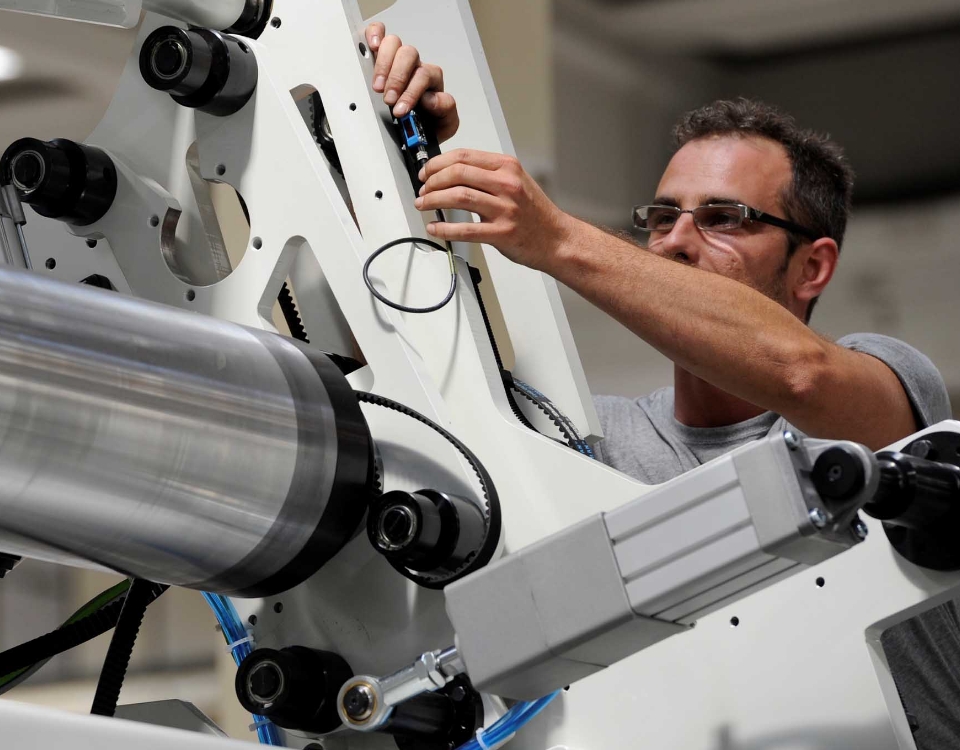
The folder is also designed with:
- Stand-by energy-saving system
- 2 standard foot pedals
- LED lighting of the working area