Efficient production process
Dal Santo S.R.L., a company specialising in sheet metal working, approached Gasparini with the need to optimise the bending process of short parts, working on several stations in an ergonomic and efficient manner. The traditional method, in fact, can cause production slowdowns and require a lot of operator interaction, increasing fatigue and the risk of errors. In addition, the handling and support of parts during bending can be complex.
To meet the customer’s needs, Gasparini designed a SuperCustom XP 330/6000 press brake, introducing two key elements: multiple TIP-TAP foot pedals and motorised R-axis front sheet lifters.
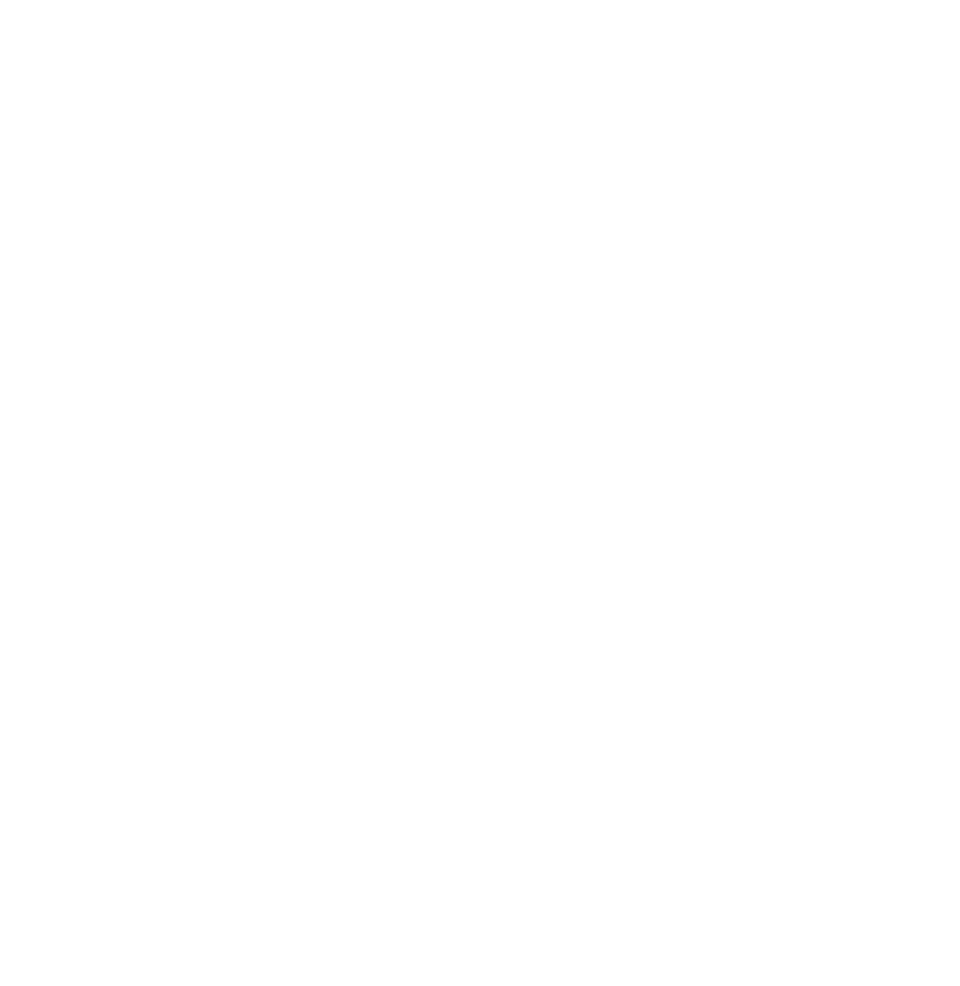
TIP-TAP multiple foot pedals: production by stations
In order to improve ergonomics and operational efficiency, Gasparini has developed a multiple foot pedal system that brings a number of advantages:
- this configuration makes it possible to operate several bending stations in sequence;
- as workpieces progress from one station to the next, the operator can manage the bending process with intuitive and ergonomic control, reducing waiting time;
- the system allows for smoother and faster work, ensuring more efficient production and reducing operator fatigue.
Front sheet lifters with motorised R-axis: support and precision
In order to ensure optimal support during processing, the machine has been equipped with advanced front sheet lifters:
- the sheet guides are equipped with motorised movement on the R-axis, allowing perfect positioning and support of the material;
- in addition to facilitating the lifting and handling of parts, they perform the dual function of sheet metal support to ensure stability and precision during bending;
- this solution significantly reduces manual intervention, improving bending quality and increasing operational safety.
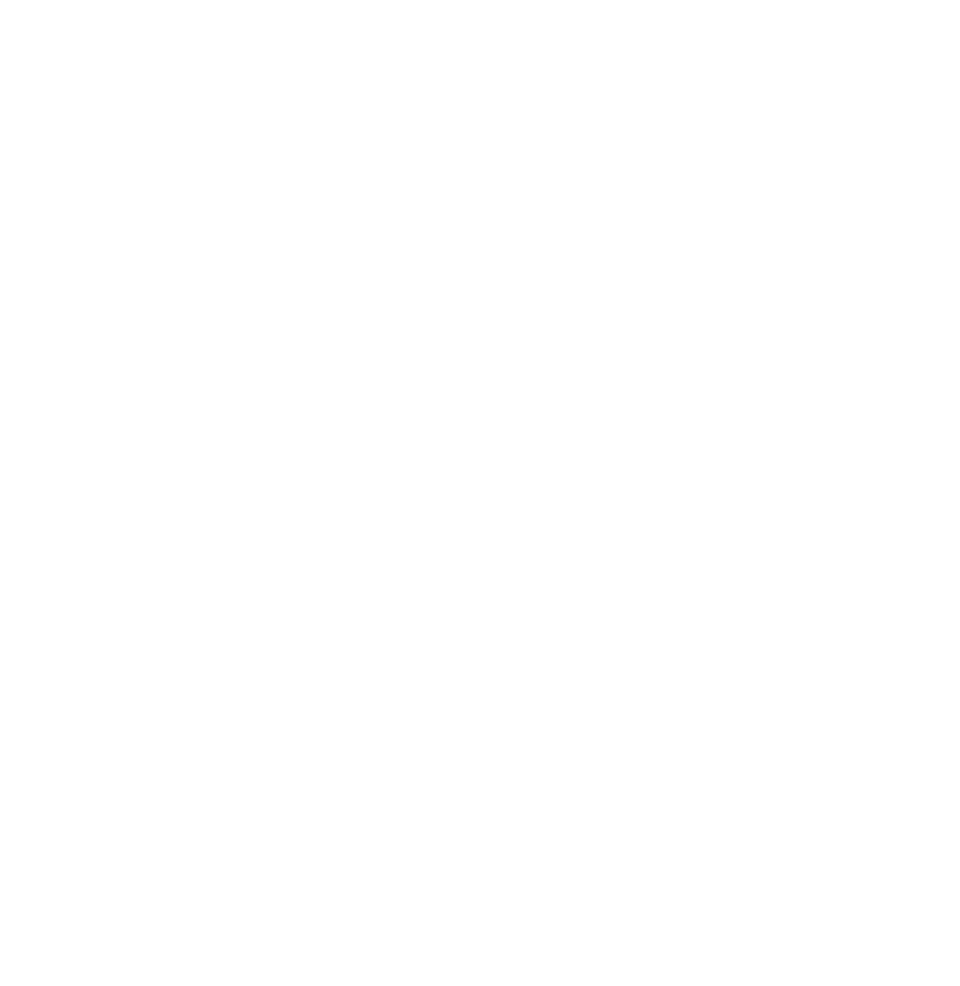
E-Reflex system for automatic compensation of structural deformations
Thanks to the E-Reflex system, the machine is able to detect and compensate for structural deformations occurring during bending in real time. This ensures consistently accurate results, eliminating the need for manual adjustments and reducing the margin of error.
5-axis backgauge for accurate workpiece positioning
The 5-axis (X-R-Z1-Z2-X6) fully CNC-controlled backgauge, with X-axis travel of 800 mm (with a stop at 1000 mm), allows extremely precise material positioning and ensures maximum repeatability in the most complex machining operations. It is also equipped with 2 retractile back supports and an additional stop on a reference. This configuration offers greater operational flexibility, allowing the handling of diverse geometries with extreme accuracy.
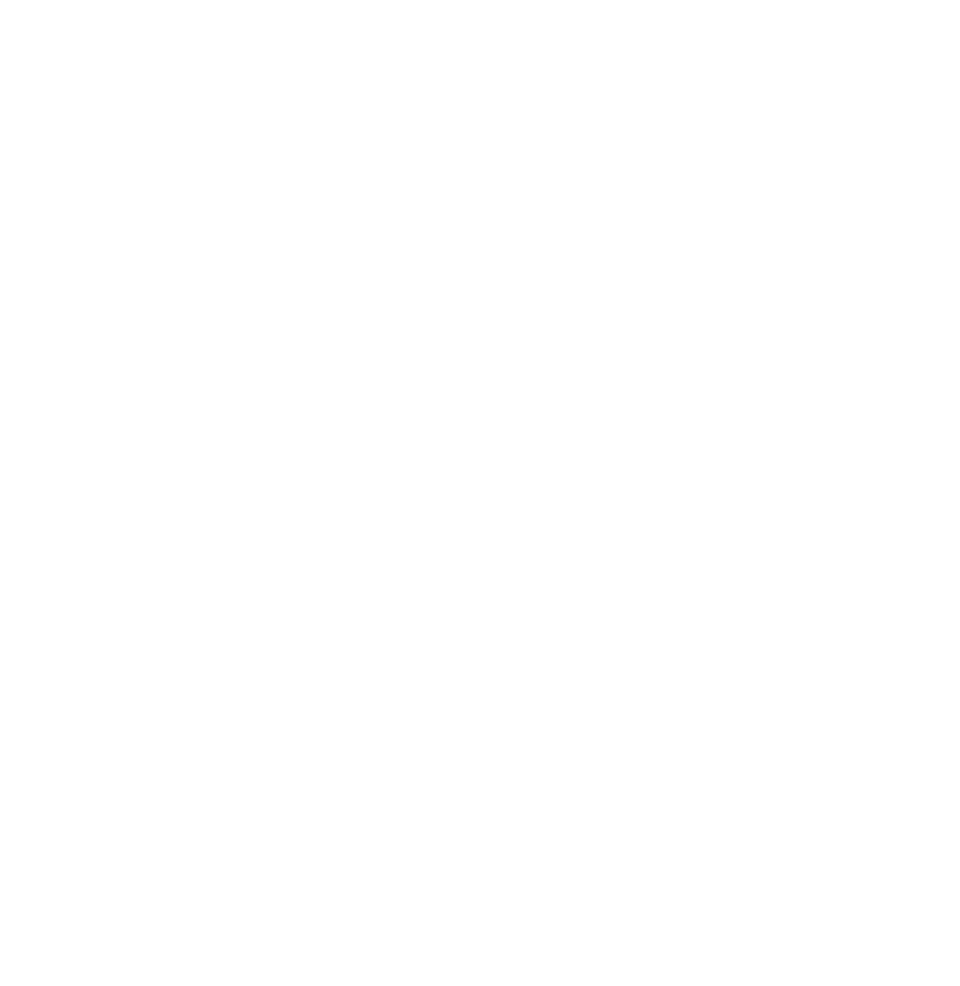
CNC and software
The CNC is the Delem DA-69S, mounted on a top-mounted, double-jointed cabinet.
The DA-69S offers 2D and 3D programming including automatic bending sequence calculation and collision detection. Full 3D machine configuration with multiple tool stations provide real feedback on feasibility and product handling. Highly effective control algorithms optimise the machine cycle and minimise set-up times.
Delem Profile-S 3D software allows bending operations to be programmed in an intuitive and advanced way. Thanks to three-dimensional simulation, operators can visualise the process before the actual execution, reducing errors and optimising production time.
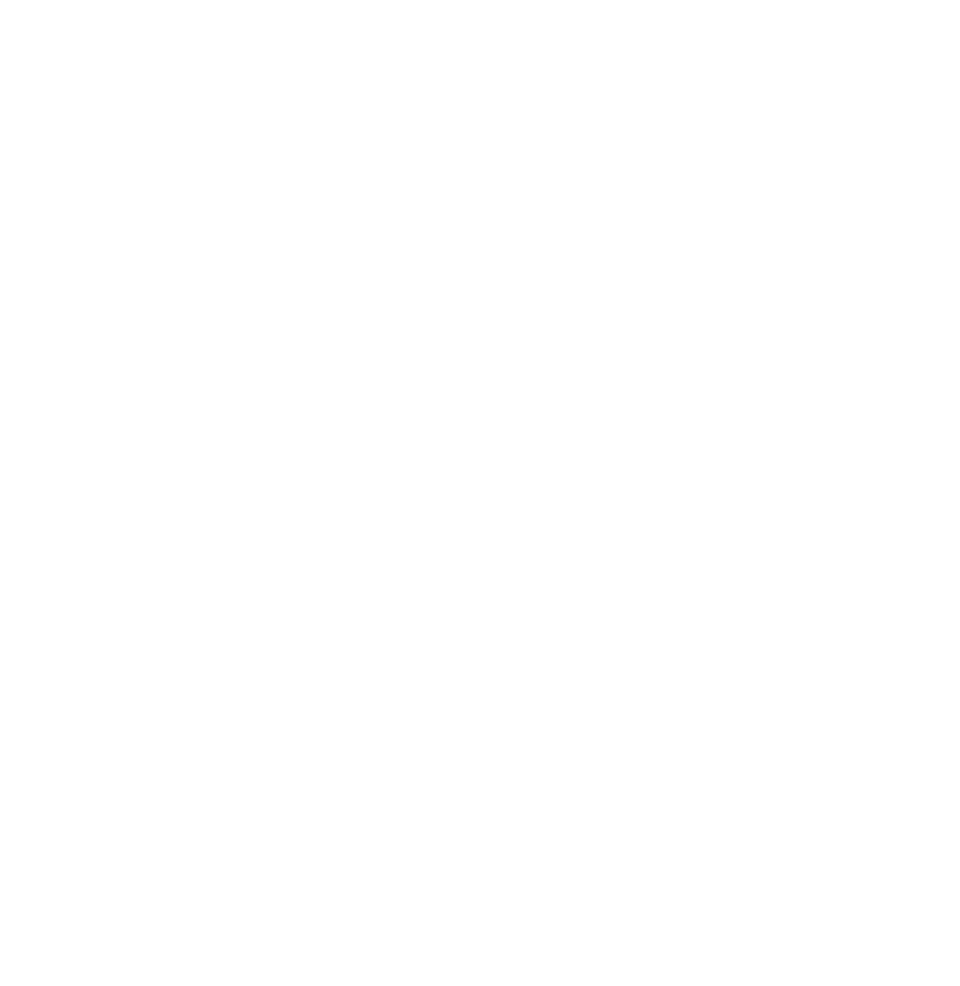
ECO+ system for reduced energy consumption
The innovative ECO+ system optimises machine energy consumption, reducing waste without compromising performance. This translates into cost savings for the company and greater environmental sustainability.
Locking system: stability and versatility
For maximum machining reliability and versatility, the XP330/6000 is equipped with an advanced clamping system:
- nitrided strips on the crossbar, offering greater wear resistance and durability;
- Gasparini hydraulic lower clamping, for quick and safe tool clamping;
- manual clamps on cross beam without intermediates, which simplify tool installation and improve operability;
- provision for ROL GRIP intermediates, which allows even faster and more flexible tool change, improving production efficiency.
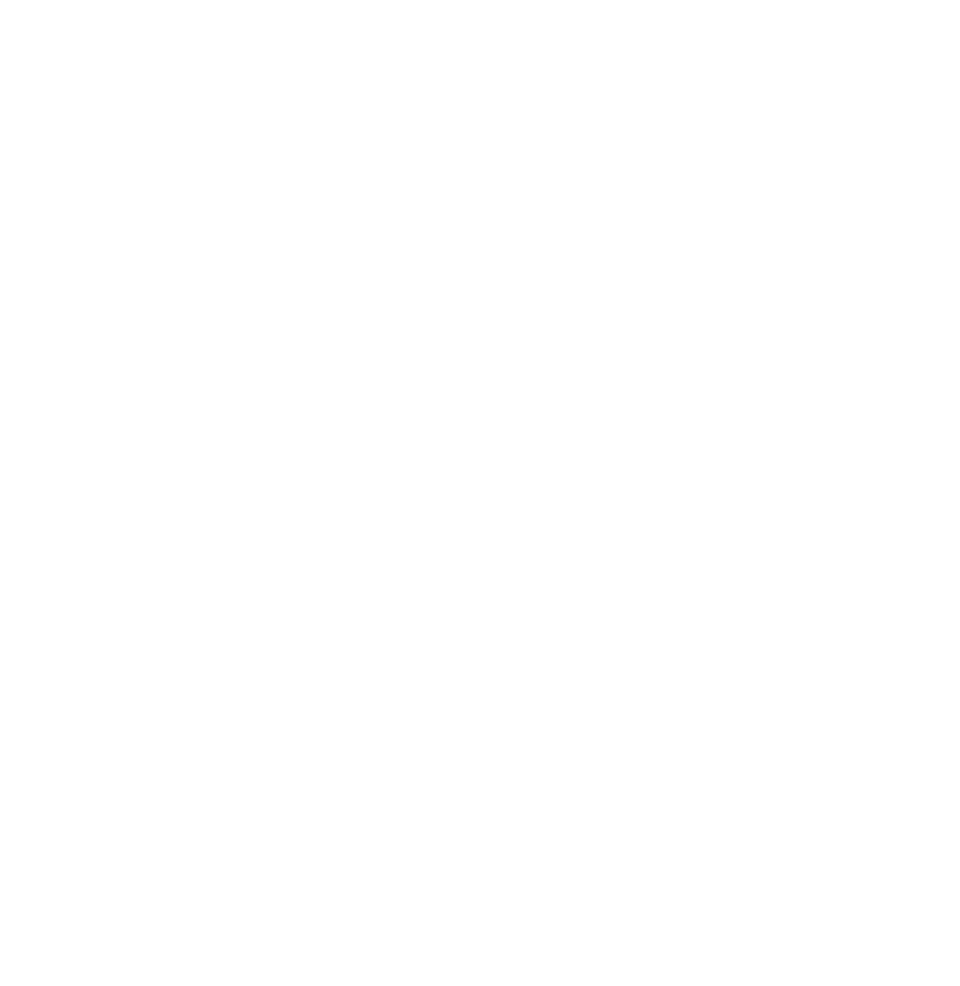
Other systems and accessories
In addition, this press brake features:
- three-light column for machine activity status display
- electrical and pneumatic set-up for bending tool
- 2 standard front supports
- DSP-AP laser safety system with PLC
- 2 standard foot pedals
- drive bar for tool positioning
- provision for Tele-Link remote assistance
- LED work area lighting
- Industry 4.0 package