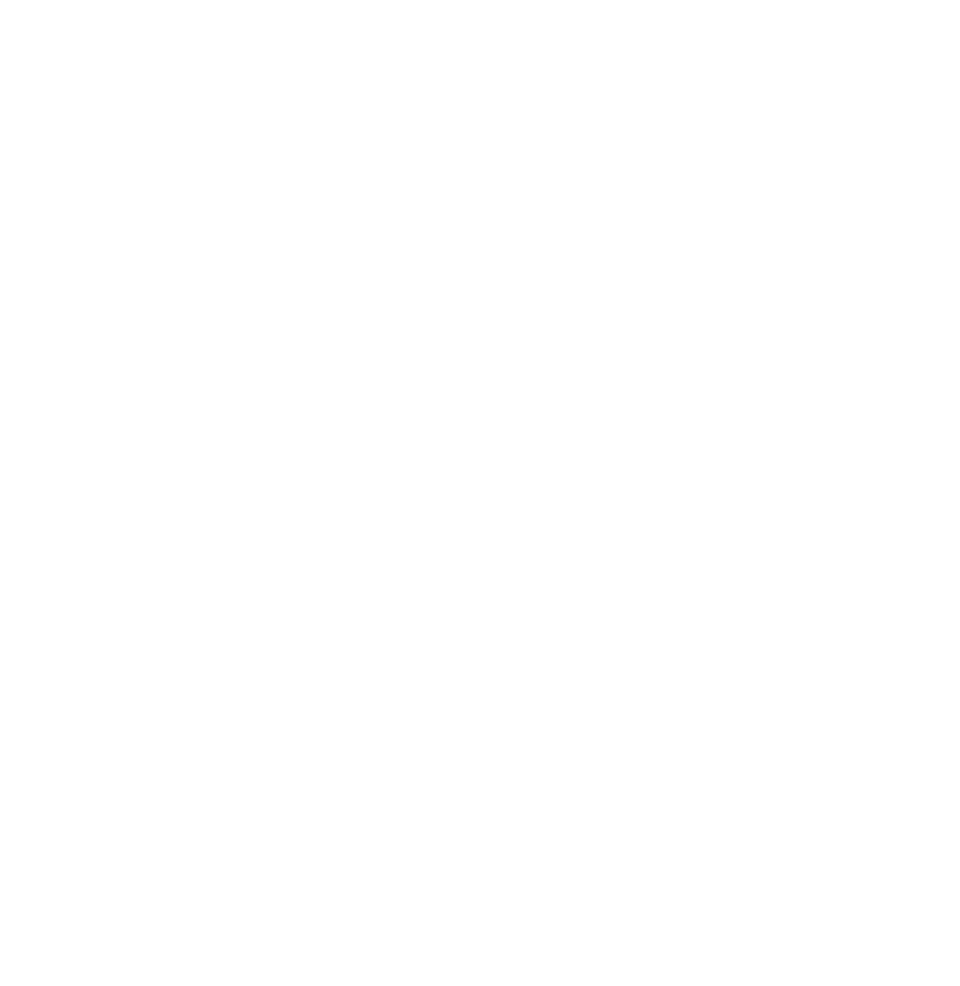
The main technical features of the press brake
This bending machine features the top-mounted Delem DA-66T CNC and Delem Profile Lite TL 2D offline software for ease of use and state-of-the-art technology. The touch screen provides access to the proven user interface and direct navigation between programming and production. Functions are placed directly where they are needed, offering optimised ergonomics. The DA-66T offers 2D programming including automatic bending sequence calculation and collision detection. Highly effective control algorithms optimise the machine cycle and minimise set-up times. This makes press brake operation easier, more efficient and more versatile than ever before.
In addition, communication standards compliant with Industry 4.0 Intelligent Factory models have been installed.
The choice of clamping system
With regard to the choice of clamping system, the customer decided to equip the press brake with the 110 mm high Gasparini AirSlide upper pneumatic system for European type tools and the manual lower clamping device. Gasparini AirSlide is an innovative compressed air distribution system that allows tool adapters to be moved along the entire length of the ram in any position, without connecting pipes and without tools. They can be removed or added in any combination, without air leakage. In addition, they are self-aligning: the punches are lifted and brought into position.
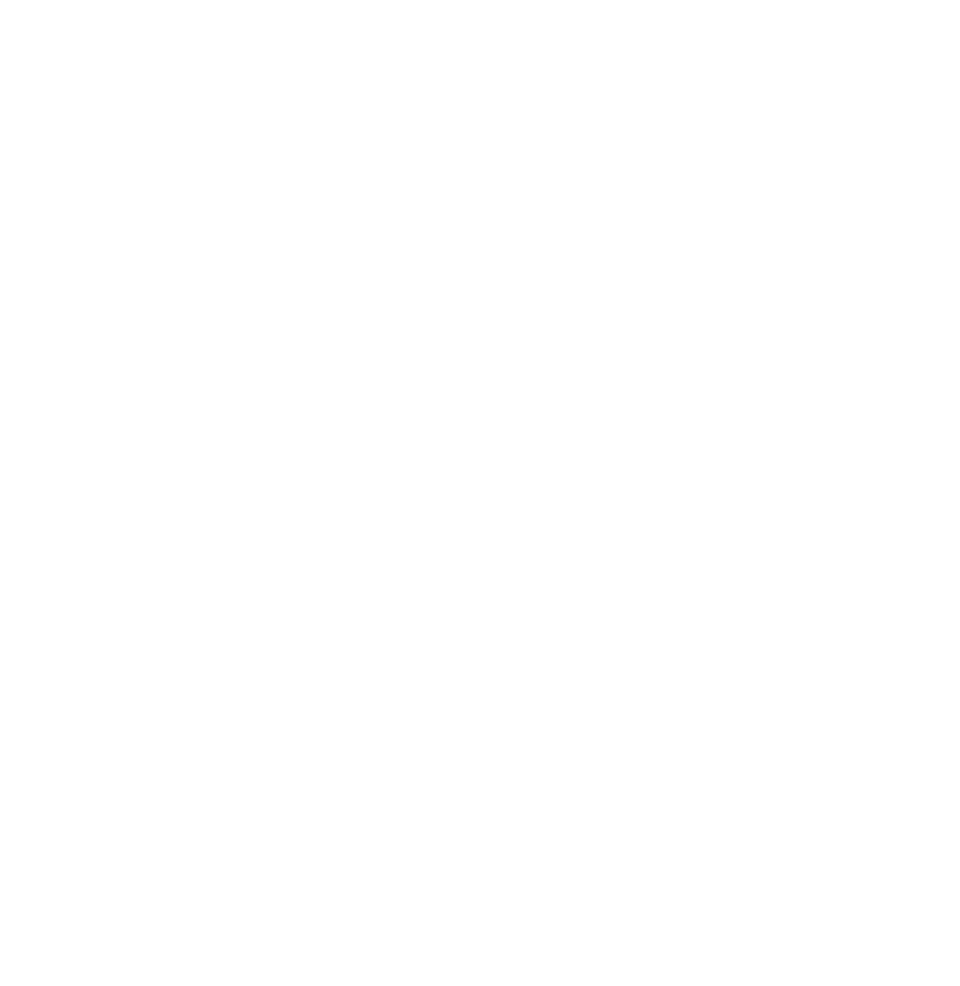
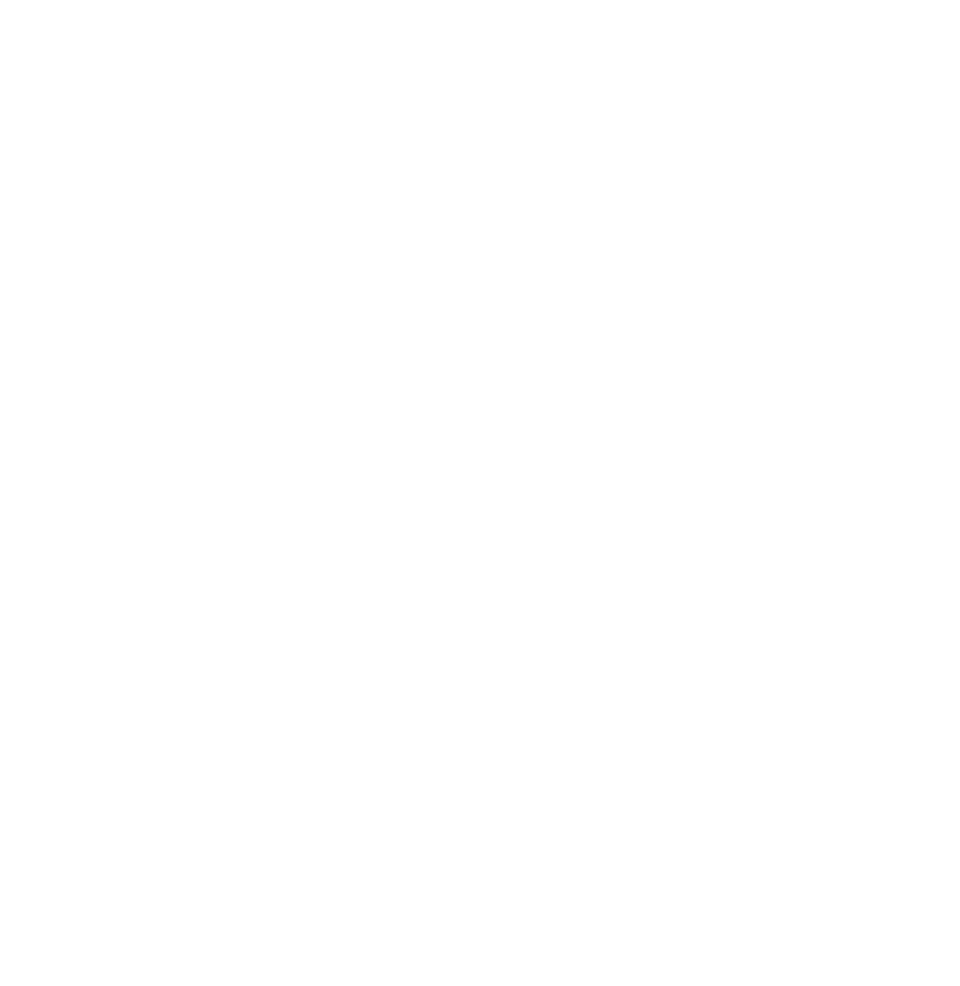
The choice of angle control system
The machine is equipped with the Iris Plus laser angle control system. This is an automatic measuring system integrated in the safety device without physical contact with the sheet metal.
Inside the receiver is a real-time image processor that transfers data to the CNC during bending.
A range of data is provided including:
- internal and external angles
- average angle
- springback
- thickness
Iris Plus processes the part profile image. Measure and compare:
- internal angle
- external angle
Precision and ergonomics of the press during bending: how we achieved them
The backgauge is 4-axis (X-R-Z1-Z2) CNC-controlled, which in addition to the two standard axes also features the Z1 and Z2 axes. It also has an additional stop on a backgauge reference for an increased depth of support during bending.
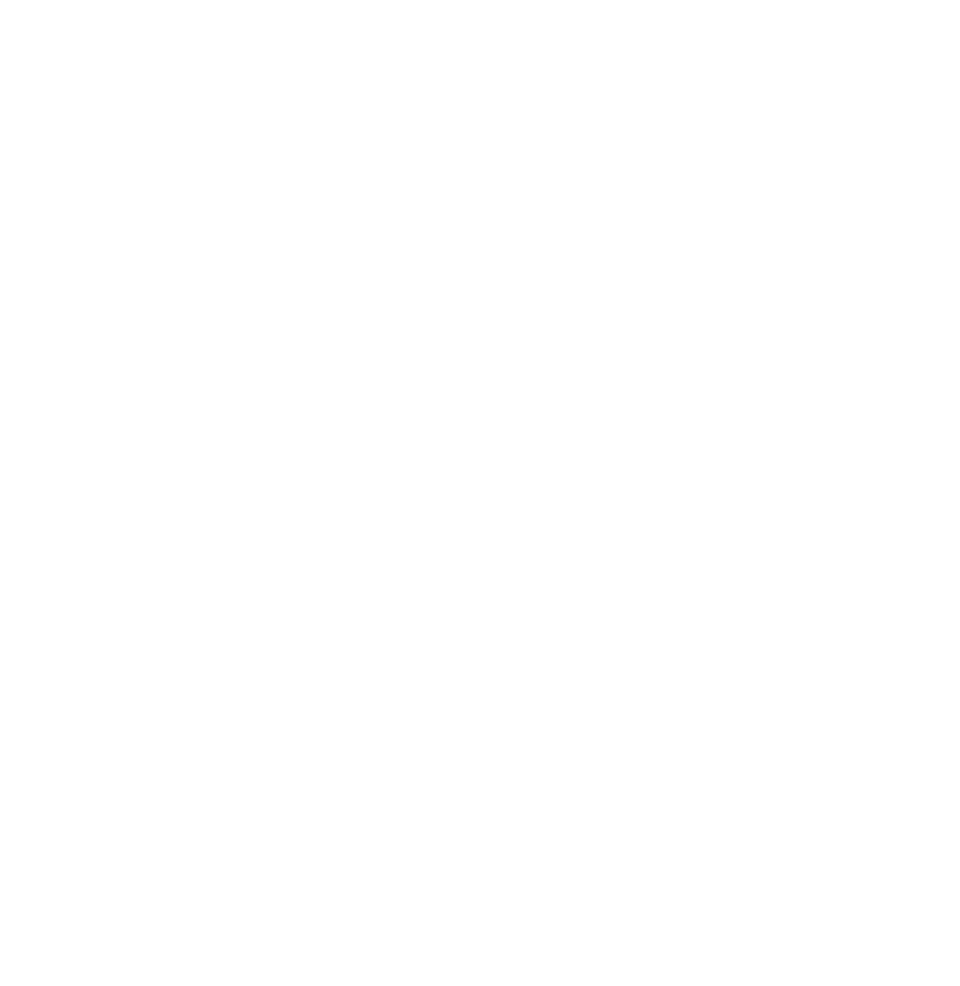
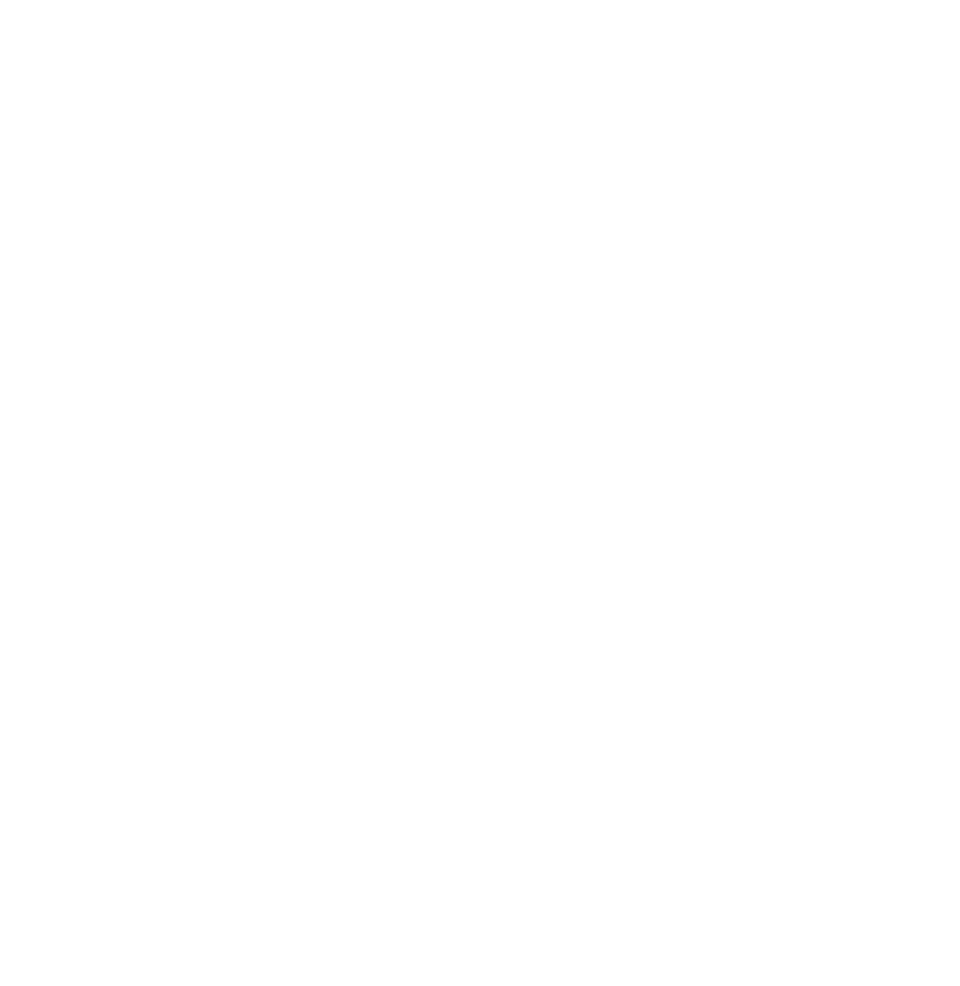
The customer chose to equip the press brake with a tool holder in the side cabinet, in order to be able to quickly and comfortably handle tool changes during bending.