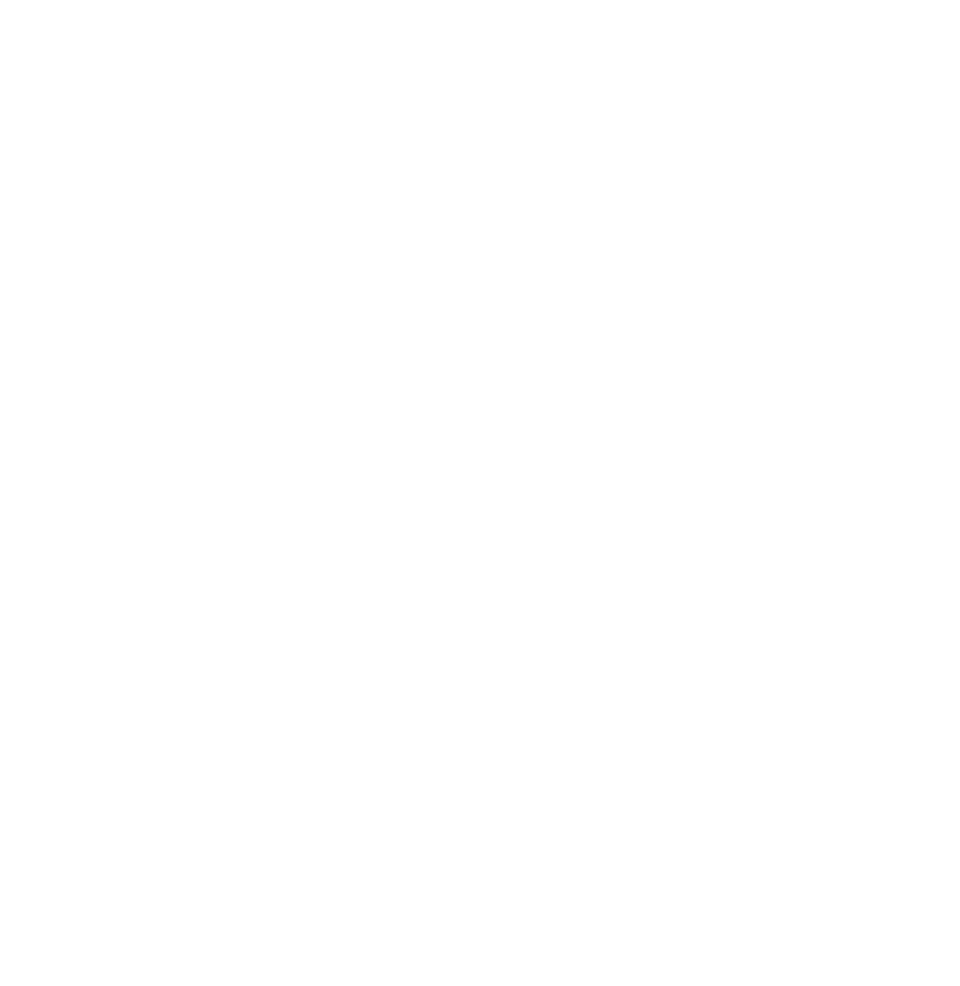
Main technical features
This press brake is equipped with the Gasparini Adaptive Crowning System and the E-Reflex Deformation Compensation System. Thanks to these technological solutions, the machine ensures excellent quality results. The use of these technologies allows extraordinary precision and constant repeatability of the bent parts.
The upper clamping system is of the Gasparini AirSlide pneumatic series, 200 mm high for European type tools. The lower clamping system is Gasparini’s pneumatic type.
In addition, the Laser Line system for bending without reference has been installed.
CNC and software
The CNC is of the ESA S875W type (on a mobile control desk):
- 21″ high resolution touch screen (16:9)
- 2D programming
- Network interface
- 2D offline CNC included
- 3D offline programming Autopol, Metalix, Radan
- 3D drawing and DXF, STEP and IGES import into the CNC or PC
- Esabend 3D-M
- MBEND offline software for 2 workstations
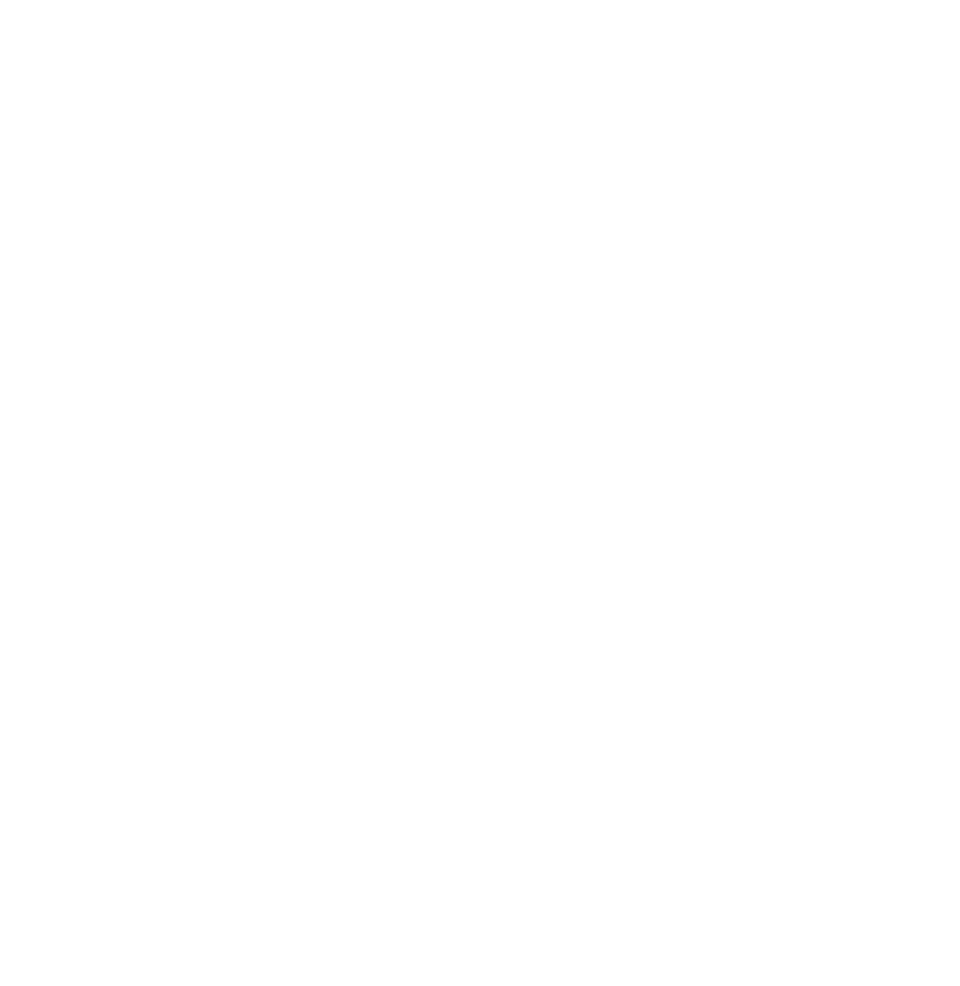
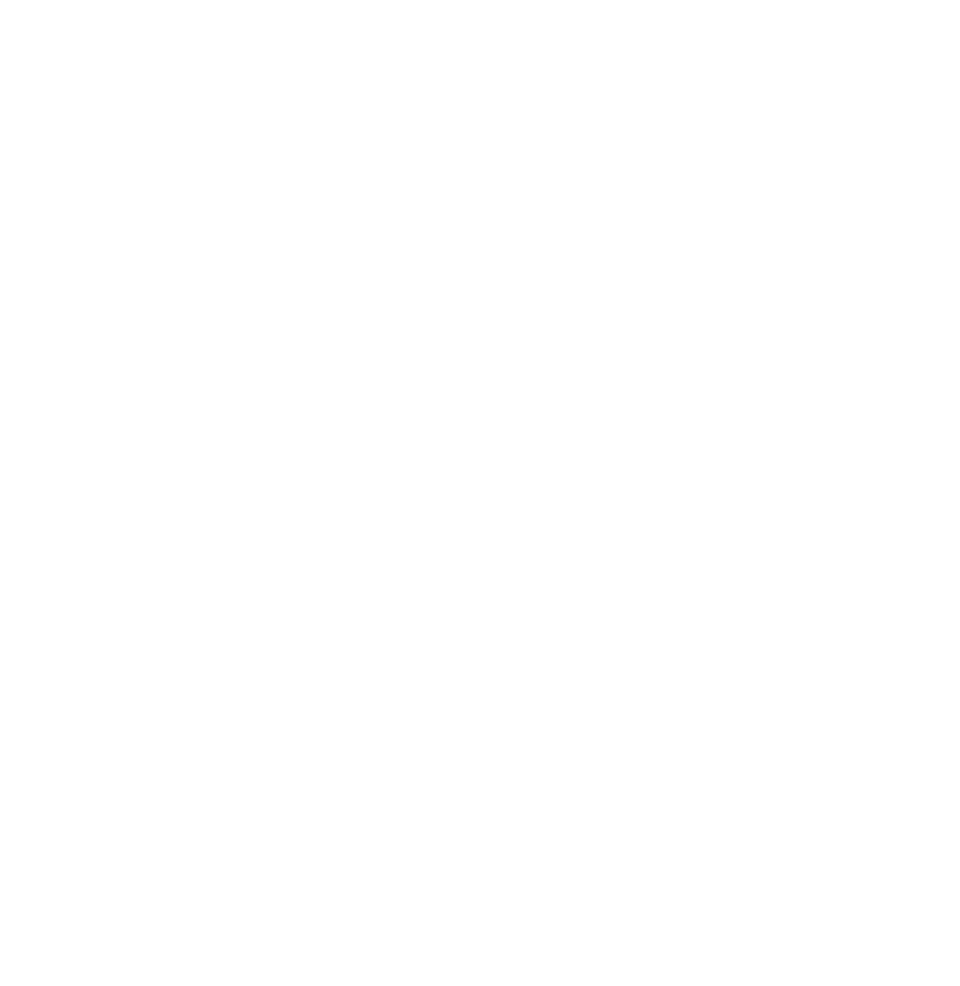
Backgauge
The backgauge is 5-axis (X-R-Z1-Z2-X6) CNC-controlled, and has an X-axis travel of 800 mm (with a stop at 1000 mm). It has an additional stop and reference, and two retractile back supports, featuring polyethylene profiles that allow even the thinnest sheets to be supported without scratching their surfaces.
Security System
The DSP-AP laser safety system generates a visible laser beam conforming to EN12622. The beam protects the operator from the danger of crushing between punch and die.
This device allows the speed change point to be lowered by up to 4 mm from the plate. The result is that the upper cross beam moves at high speed for longer, limiting the part of the bending sequence where speed is reduced to a minimum.
The time saved with DSP-AP compared to a light curtain or other guarding is approximately 1.2 seconds per bend. The DSP-AP laser guard also supports auto blanking for automatic recognition of boxed and side-walled profiles.
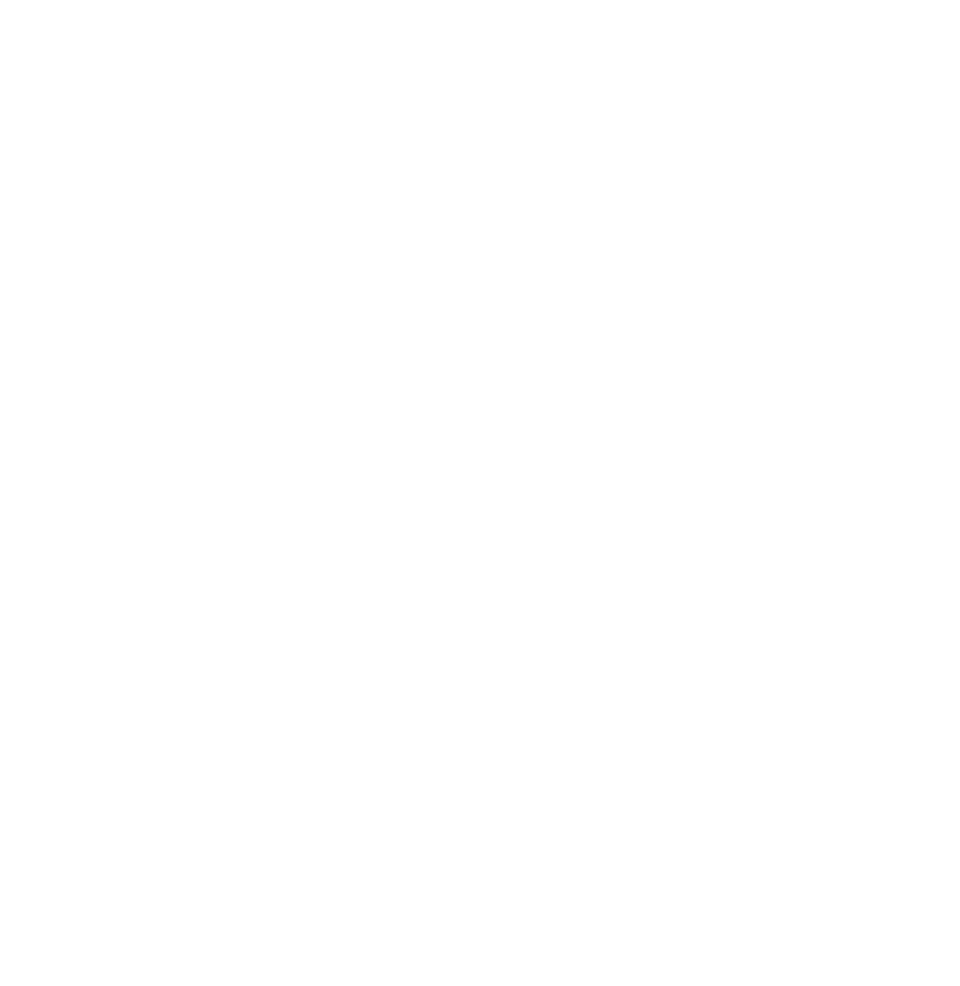
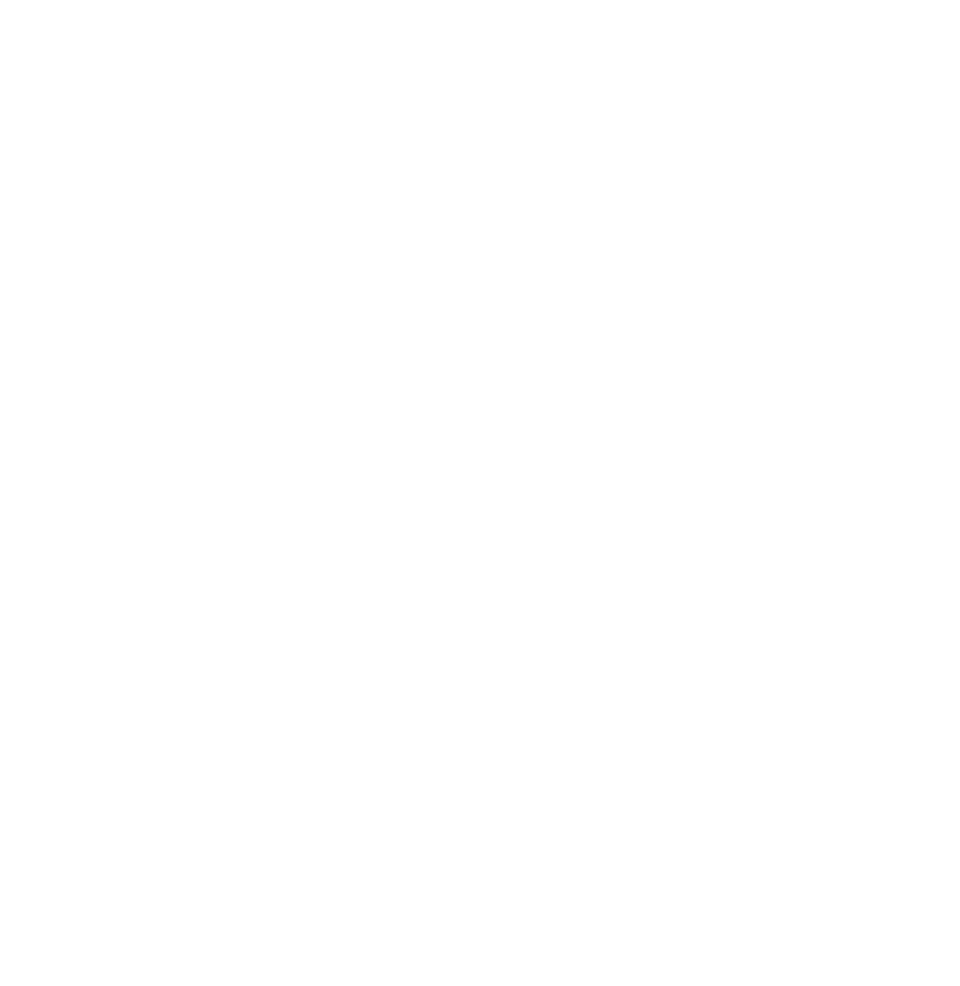
Sheet lifter
BS Impianti’s press brake is equipped with a sheet lifter with manual adjustment of the R-axis and extendable front table.
It consists of a mobile sheet metal support placed on the front of the machine, at the height of the bending line. Controlled by the CNC, it supports the sheet metal during the bending process. It can also be mounted on the inside of the press brake.
Energy saving
The customer chose to install the ECO energy-saving package. It is based on the continuous control of the main motor of the press brake via a vector inverter. Instead of running continuously at a constant speed, the main motor is regulated continuously. This makes it possible to run the pump at low speed when low flow is required, and to accelerate to maximum performance when the full available flow and pressure are needed.
Thanks to a new configuration of the hydraulic circuit, we control the flow rate according to the bending process. Environmental friendliness, energy savings, speed, low noise, limited maintenance, less waste, extreme precision and repeatability are the main advantages of the ECO package.
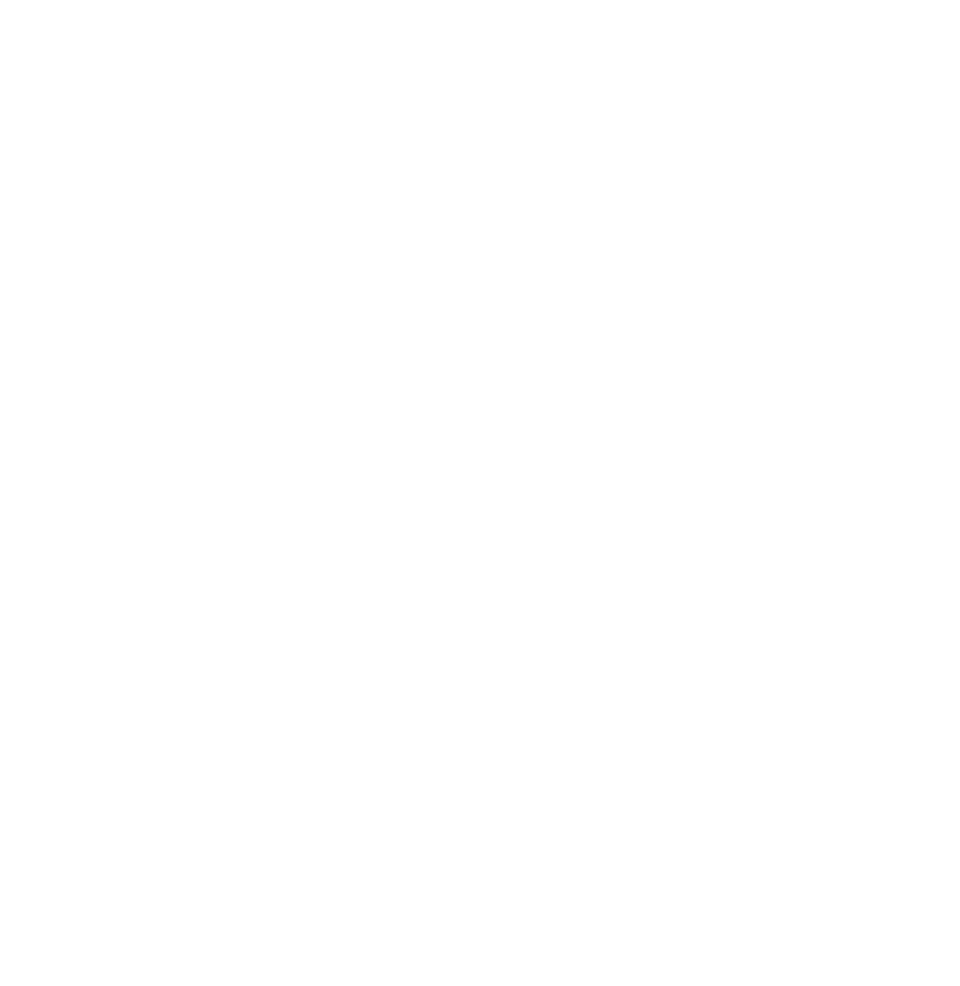
In addition, this machine has been equipped with:
- 2 standard front supports
- 1 wireless sliding footpedal
- Tele-Link remote assistance
- LED lighting of the working area
- Industry 4.0 package