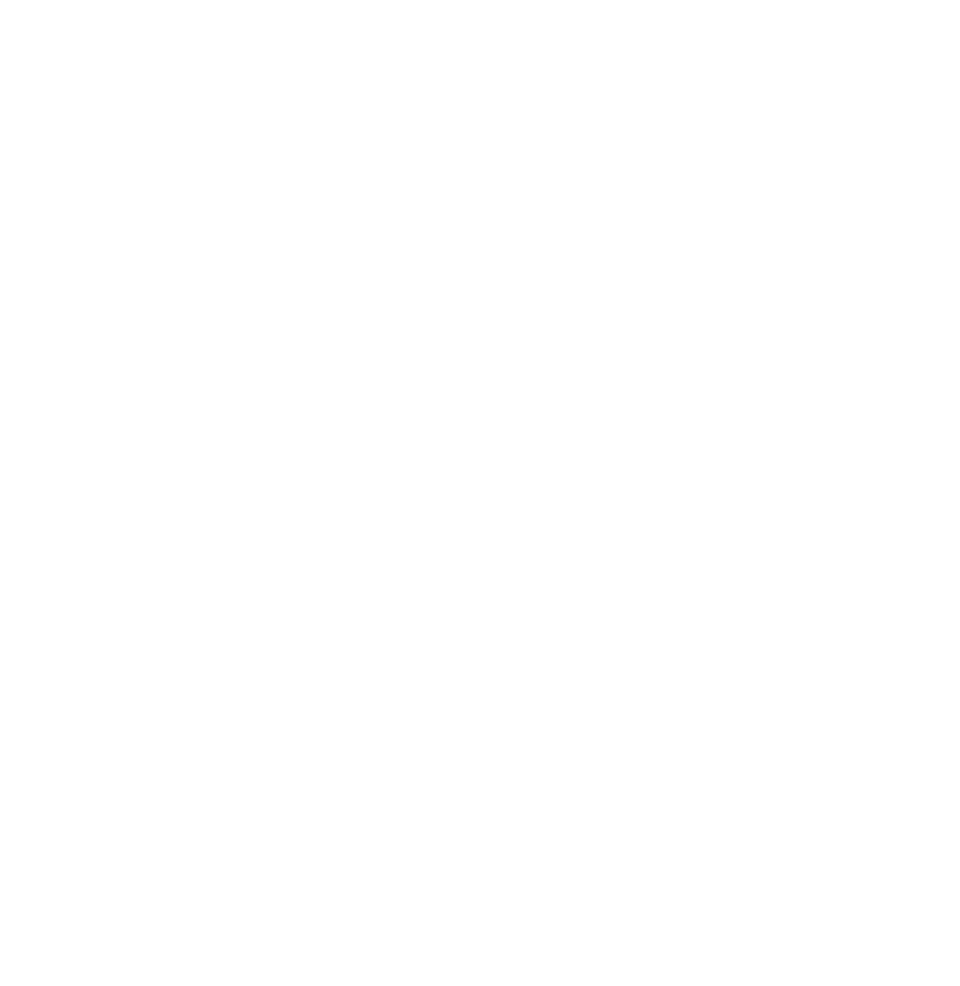
The main technical features of the press brake
Gasparini Adaptive Crowning, represents the patented system for a constant angle. At the heart of the crowning system are the two sensors placed on the ram and on the lower beam of the machine. The first one detects the deformation of the ram since bending begins. Then the CNC drives the pistons in the lower beam until the measurement of the second sensor matches that of the first, thus achieving perfect parallelism between the two beams. The result is total and precise angle control, repeatable with any type of material. This all goes to implement the E-Reflex system, the other type of compensation selected for this press brake.
The Delem DA-66T CNC and Delem Profile Lite TL 2D offline software are installed on this machine.
The open-height is 800 mm, with a Y-axis travel of 300 mm. This makes it possible to easily make box and complex parts. The upper clamping is Gasparini AirSlide pneumatic type, a system that through the distribution of compressed air allows intermediates to be moved along the entire length of the ram in any position, without connecting pipes and without tools. They can be removed or added in any combination, without air loss. In addition, they are self-aligning: the punches are lifted and brought into support. The intermediates chosen are 400 mm for European-type tools. In addition, the front supports are of the sliding type.
Communication standards in accordance with Industry 4.0 Intelligent Factory models have been installed on this press, and the Tele-Link remote service function has been arranged.
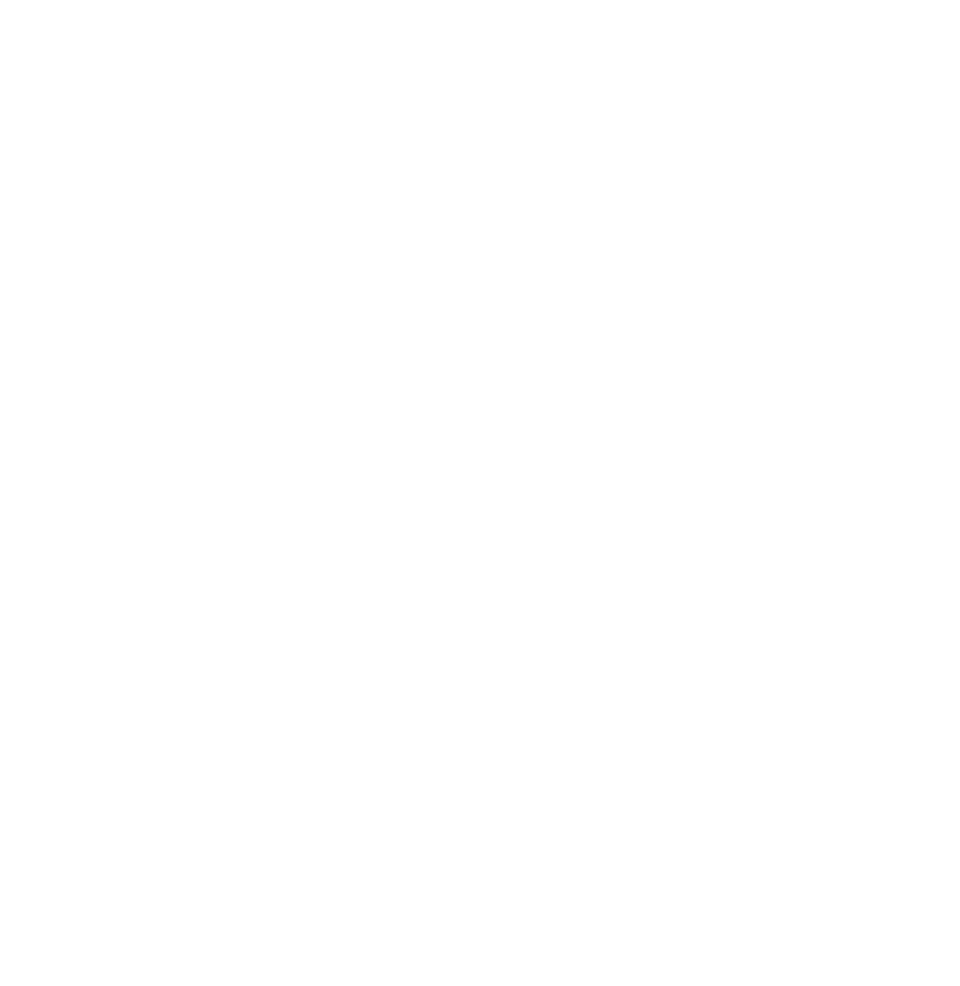
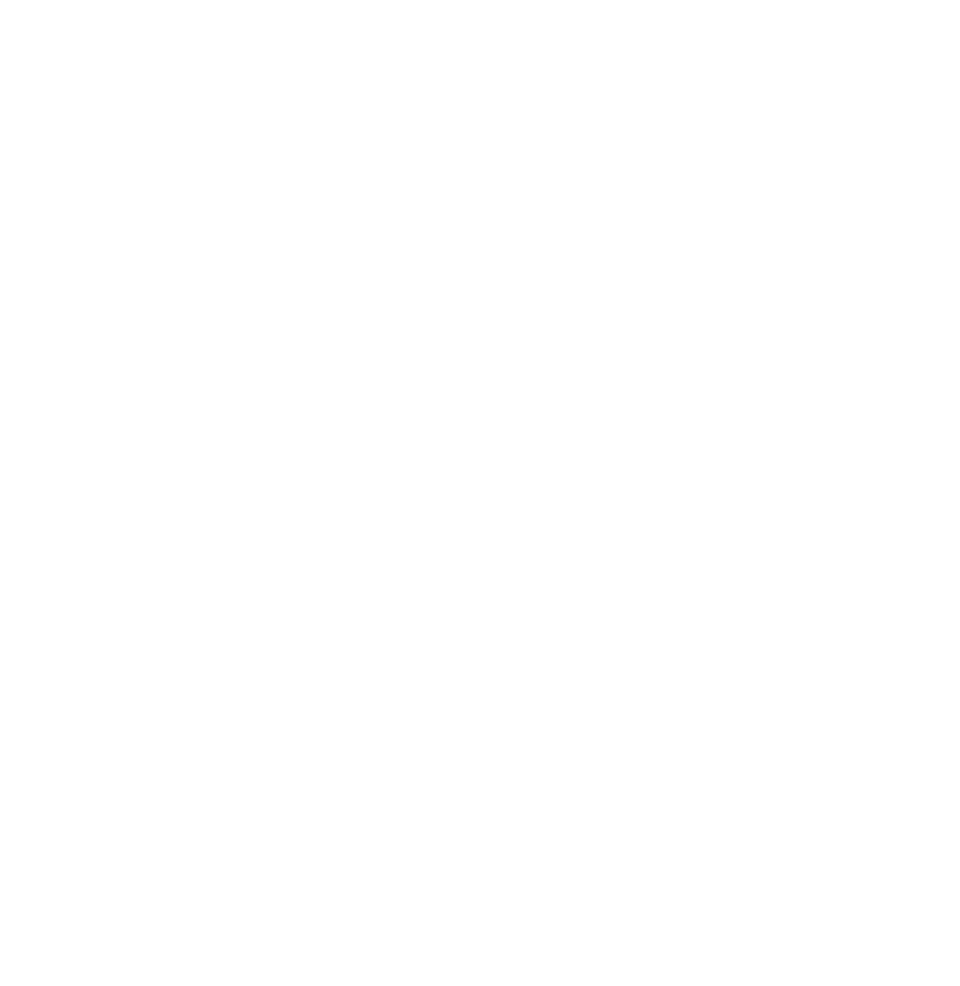
Precision and ergonomics of the press during bending: how we achieved them
The backgauge has 4 axes (X-R-Z1-Z2) controlled by CNC, which in addition to the two standard axes also features Z1 and Z2 axes. In addition, 2 retractile back supports have been implemented that can support even the largest and thinnest parts without scratching the surfaces. The installed safety system is of the DSP-AP Laser type with lowering of the speed change point and reduction of cycle time.
This press brake was developed with the ECO energy-saving system, thanks to which energy waste can be greatly decreased, thus improving productivity.
The footpedal is a wireless type, controlled therefore without wires, for maximum practicality of use. It is an evolution of Gasparini’s foot pedal, designed to take operators out of the hassle given by the ground connection cables at the front of the press. It can be clasped to a sliding bearing to slide it along the press brake with the simple push of a foot.
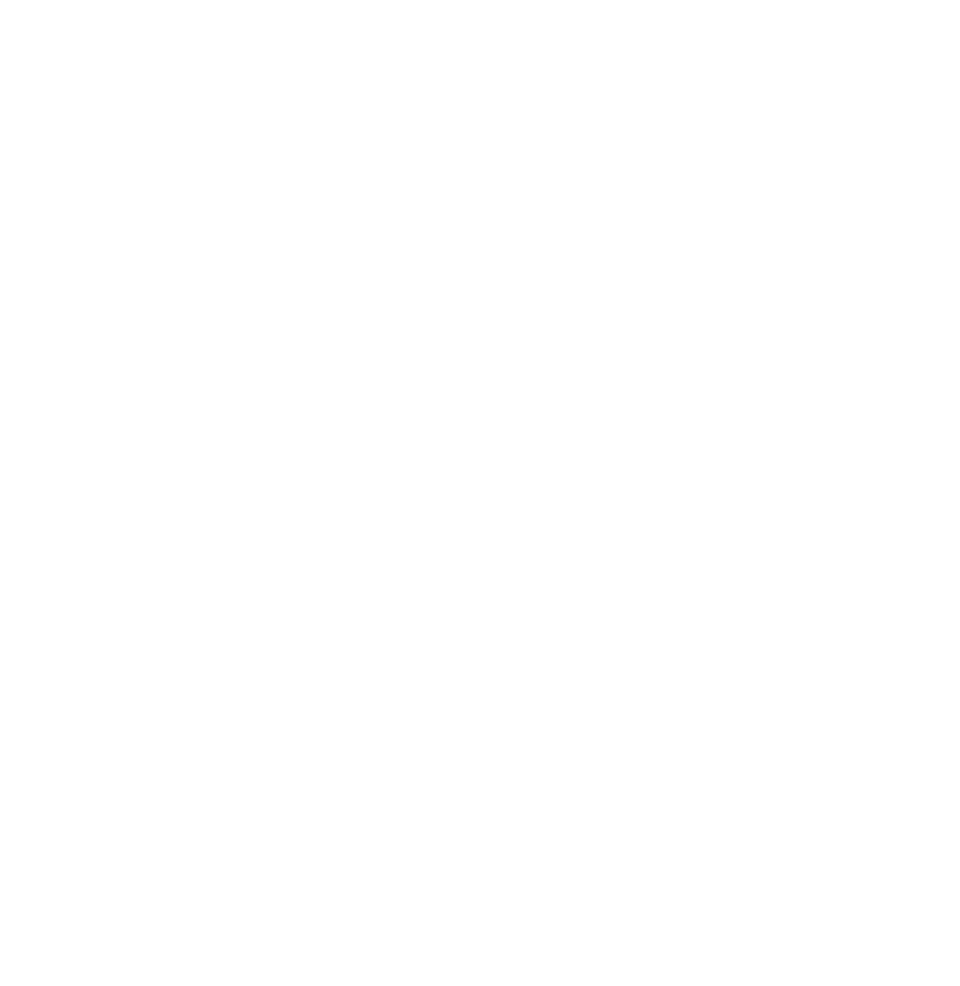
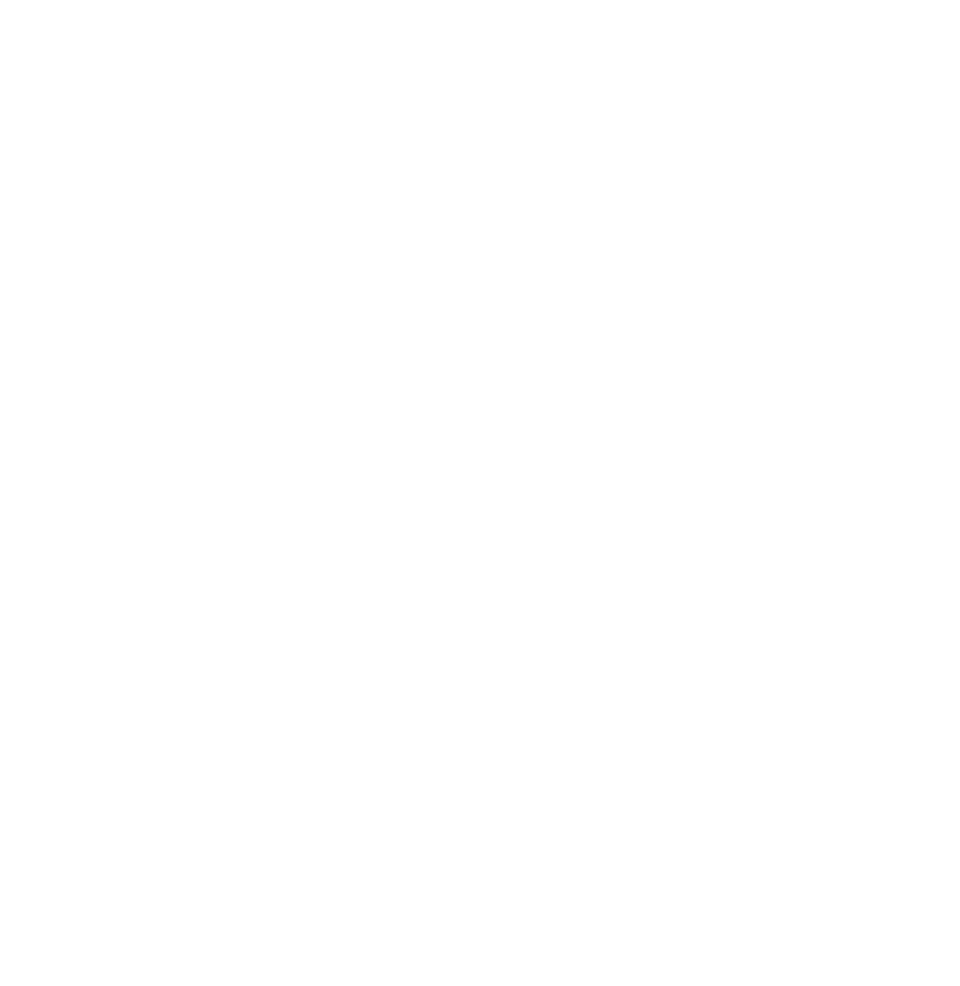
Agma, for this press chose to install the Barcode reader: a powerful handheld laser scanner. This optical barcode reader makes the operator’s work easier and reduces production time and errors, greatly increasing efficiency. The device communicates wirelessly with the charging base, which is connected to the CNC. It can read both classic 1D barcodes (EAN, Code128, Code39 Extended, etc.) and new 2D codes (DataMatrix, QR Code, etc.).
In addition to the optical reader, the Syner-G Remote Control was also provided, which provides easy access to a variety of functions including opening and closing pneumatic and hydraulic clamping, calibration of angle control systems, and parking of motorized photocells and backgauges.