X-Press press brakes can be equipped with two main CNC-controlled backgauge models; both are synonymous of robustness, accuracy and speed. Movements are carried out through expandable and flexible EtherCAT digital servodrives. Motors and drivers are manufactured by Panasonic Electric Works, who developed their application in cooperation with Gasparini.
Recirculating ball linear bearing with rack-and-pinion movement and no mechanical play ensure high and constant precision. The type of backstops and number of axes can be adapted to the type of process, part size, and number of working stations. In this way the most varied production needs are met.
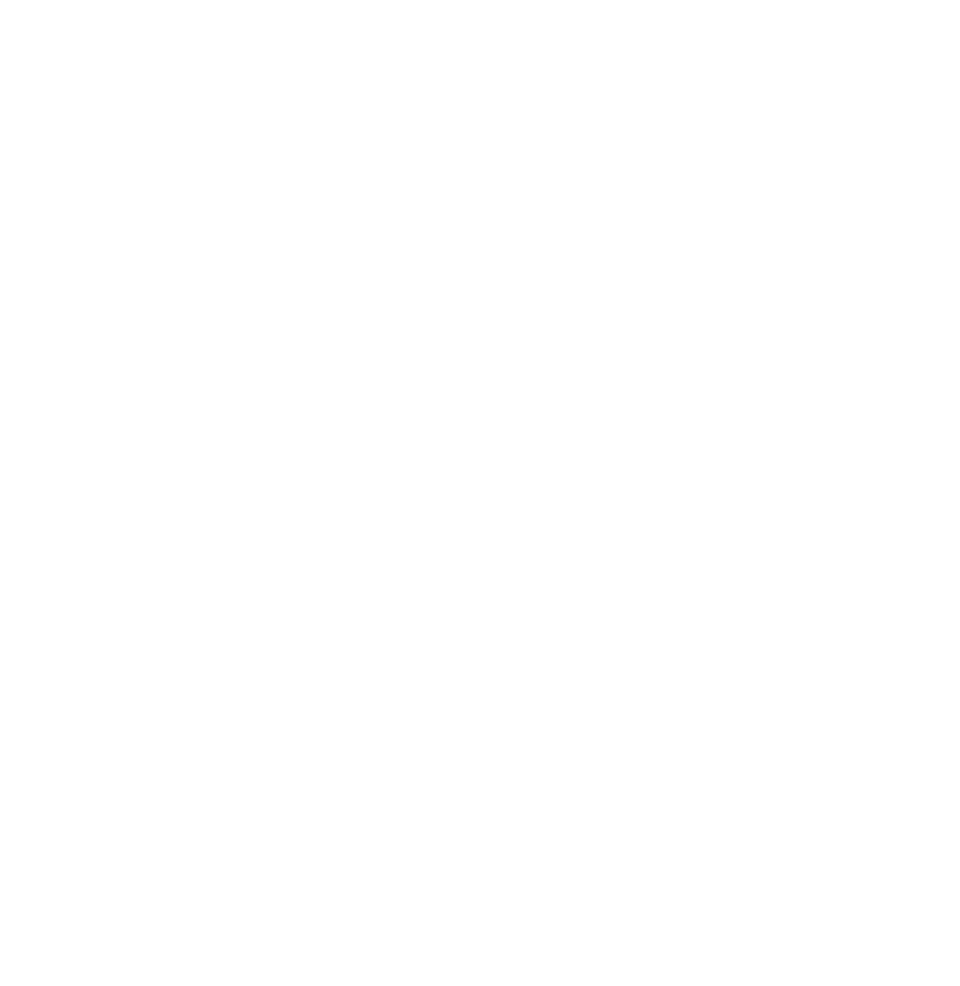
Gasparini Backgauges: fast and accurate
The Gasparini backgauge system is made of a monobloc frame, movable on recirculating ball linear bearing, with hardened and precision-ground rack and pinion. Standard configuration includes X and R axes (depth and height), and is equipped with 2 manual backstops (also known as fingers), according to the machine length, mounted on linear guides. The Gasparini Backgauge system is expandable also on existing press brakes and covers all combinations from 2 to 6 axes.
Backstops have an integrated anti-collision safety feature. Thanks to the Anti-collision System, the back gauge punch is unlocked in the event of shocks that could damage it or even make it lose its position. In this case, the operator can easily put the gauge back in its seat.
All back gauges, also in the basic 2 axes configuration, can be moved and repositioned without having to access the rear of the machine, with considerable advantages in time and safety.
Versatility
Adding Z1-Z2 axes, backstops can be moved crosswise to simplify positioning of parts with different lengths or when working on multiple stations. Brushless motors on EtherCAT bus guarantee extremely fast movements.
Should our part have offset or staggered resting points, you can add one backstop with an independent stroke with the X6 axis. By adding this axis, it is also possible to make conical bends up to 75°. In this case, shaped fingers provide three reliable resting points, to get a correct angle and bend position. To reach maximum versatility you can automate both backstops with X5-X6 axes, reaching an angle of 80° on oblique bends.
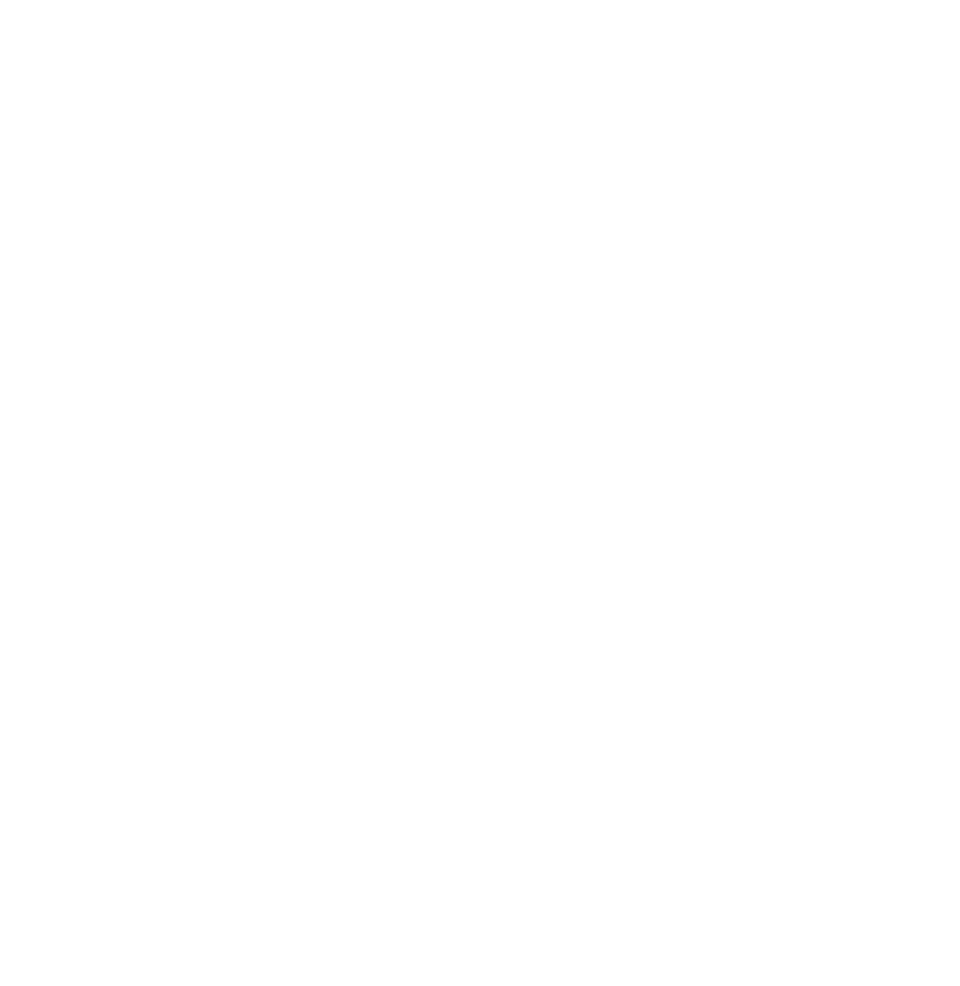
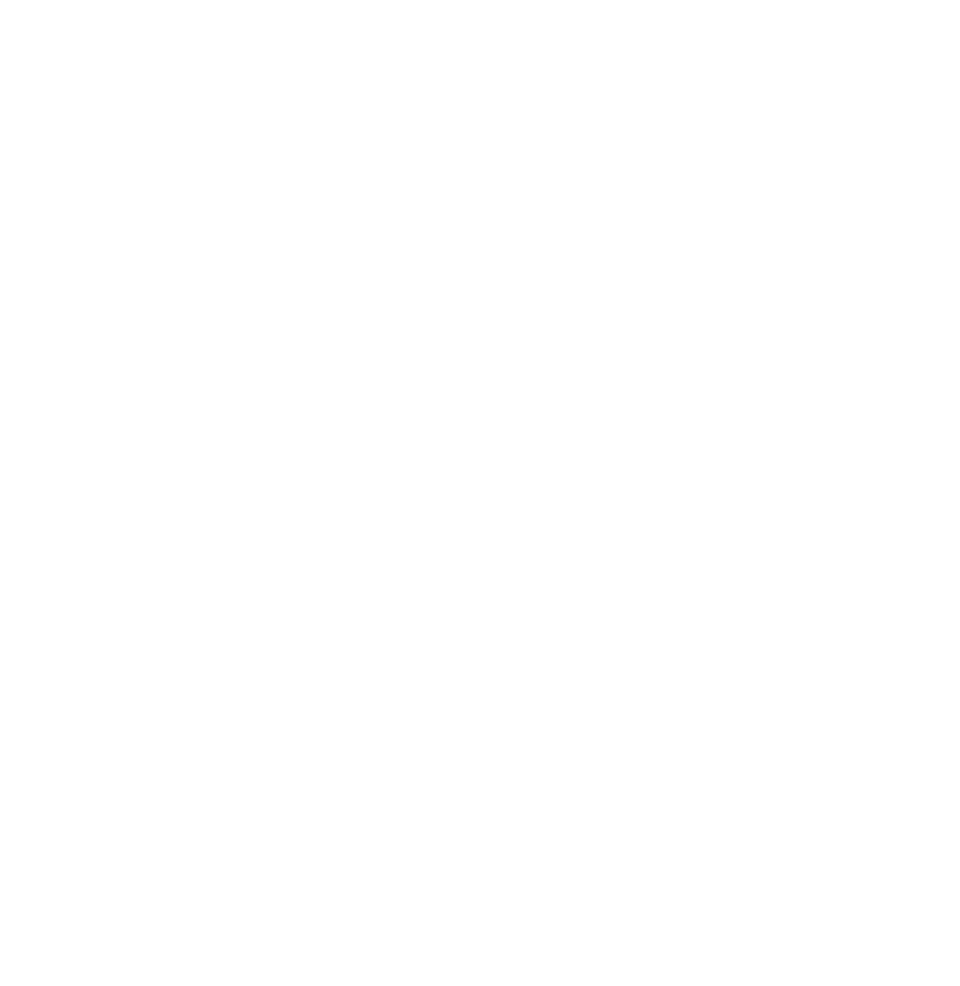
Praticity in mind
With the Thin-support system (optional retractile back supports) even thinner sheets are always correctly positioned and guided.
By selecting the F function (avalable as an option on press brakes sizes from 50 to 330 tons), the operator pneumatically unlocks and moves the turrets toward himself without the use of keys or tools: the operator can now reposition the back gauges according to the new needs from his workstation.
Tower Backgauge: absolute power and precision
Tower backgauges are extremely sturdy and precise. They are suitable for heavy processing as well as any type of bending on X-Press press brakes ranging from 100 t to 2500 t. To ensure top performances, the back gauges are designed and manufactured with high-technology, sophisticated, and reliable components. Tower backgauges provide a wide handling range, easy oblique positioning, very high precision and the possibility to integrate back sheet lifters.
Tower backgauge consists of two or more 3-axis turrets, movable on linear guides through ball screws and AC brushless motors. This configuration, with independent trolleys and axes, enables any kind of positioning, does not limit any kind of inclination or conical bending, and furthermore allows the operator to make a large variety of movements within the machine itself. On the rear side of the machine, it is possible to install sheet followers, to support the metal sheet in a similar way as with front sheet followers. They are especially useful in case of very thin, wide, and/or heavy metal sheets.
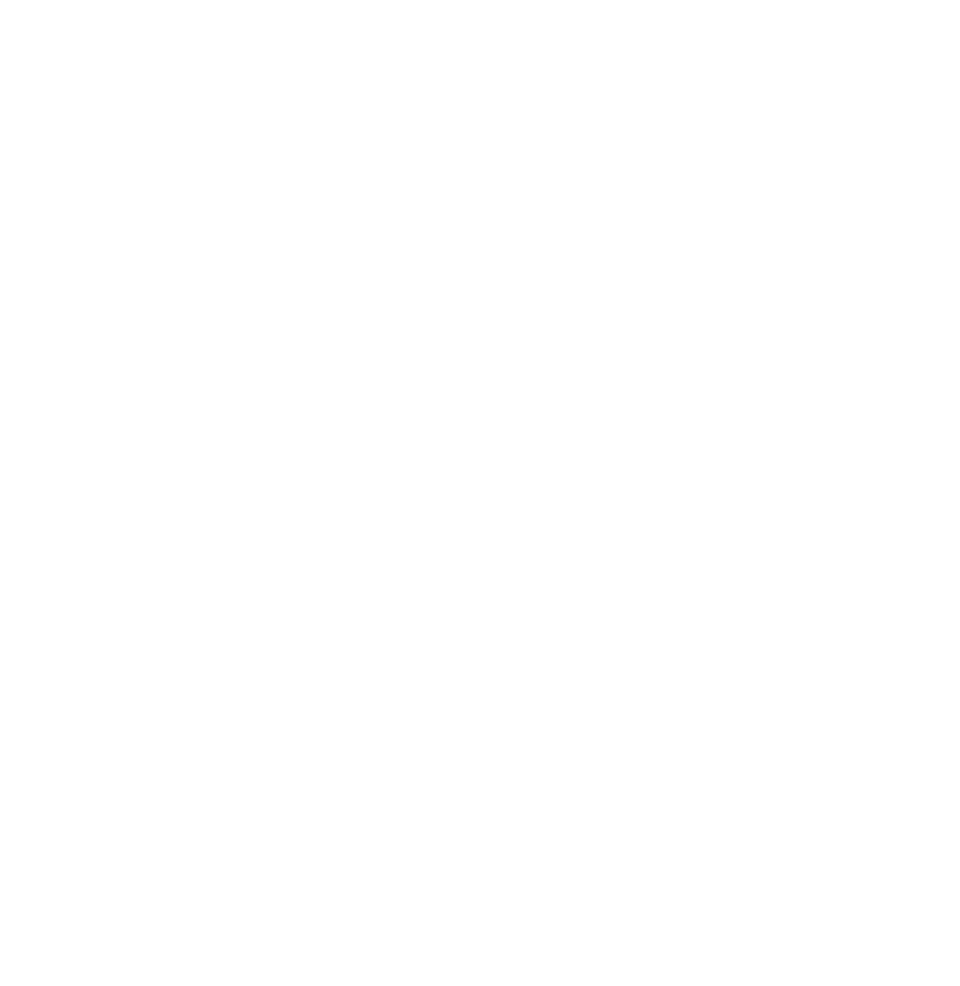
Dati tecnici Backgauge
Characteristic | Standard | Advanced | unit |
---|---|---|---|
X stroke | 600 | 600 | mm |
Extended X stroke (optional) | upon request | upon request | mm |
X speed | 500 | 500 | mm/s |
X accuracy | ±0.1 (optional ±0.05) | ±0.05 | mm |
X repeatability | ±0.05 (optional ±0.02) | ±0.02 | mm |
R stroke | 200 (optional 250) | 250 | mm |
R speed | 250 | 250 | mm/s |
R accuracy | ±0.1 | ±0.1 | mm |
R repeatability | ±0.05 | ±0.05 | mm |
Number of stops (without Z1-Z2) | according to machine length | according to machine length | N° |
Number of stops (with Z1-Z2) | 2 | 2 | N° |
Z speed | 900 | 1600 | mm/s |
Z accuracy | ±0.25 | ±0.25 | mm |
Z repeatability | ±0.15 | ±0.15 | mm |
X6 stroke | ±150 | ±150 | mm |
X6 speed | 125 | 125 | mm/s |
X6 accuracy | ±0.1 | ±0.1 | mm |
X6 repeatability | ±0.05 | ±0.05 | mm |
X6 displacement angle | 75 | 75 | ° |
X5-X6 displacement angle | 80 | 80 | ° |
Minimum distance between stops | 100 | 100 | mm |
Minimum distance between stop and side frame | 200 | 200 | mm |
Minimum distance between manual stops | 60 | 60 | mm |
Minimum distance between manual stop and side frame | 100 | 100 | mm |
Tower Backgauge
Characteristics | Value | unit |
---|---|---|
X stroke | 950 | mm |
X speed | 600 | mm/s |
X accuracy | ±0.1 | mm |
X repeatabilityX | ±0.2 | mm |
R stroke | 300 | mm |
R speed | 200 | mm/s |
R accuracy | ±0.1 | mm |
R repeatability R | ±0.05 | mm |
Z speed | 560 | mm/s |
Z accuracy | ±0.2 | mm |
Z repeatability | ±0.1 | mm |