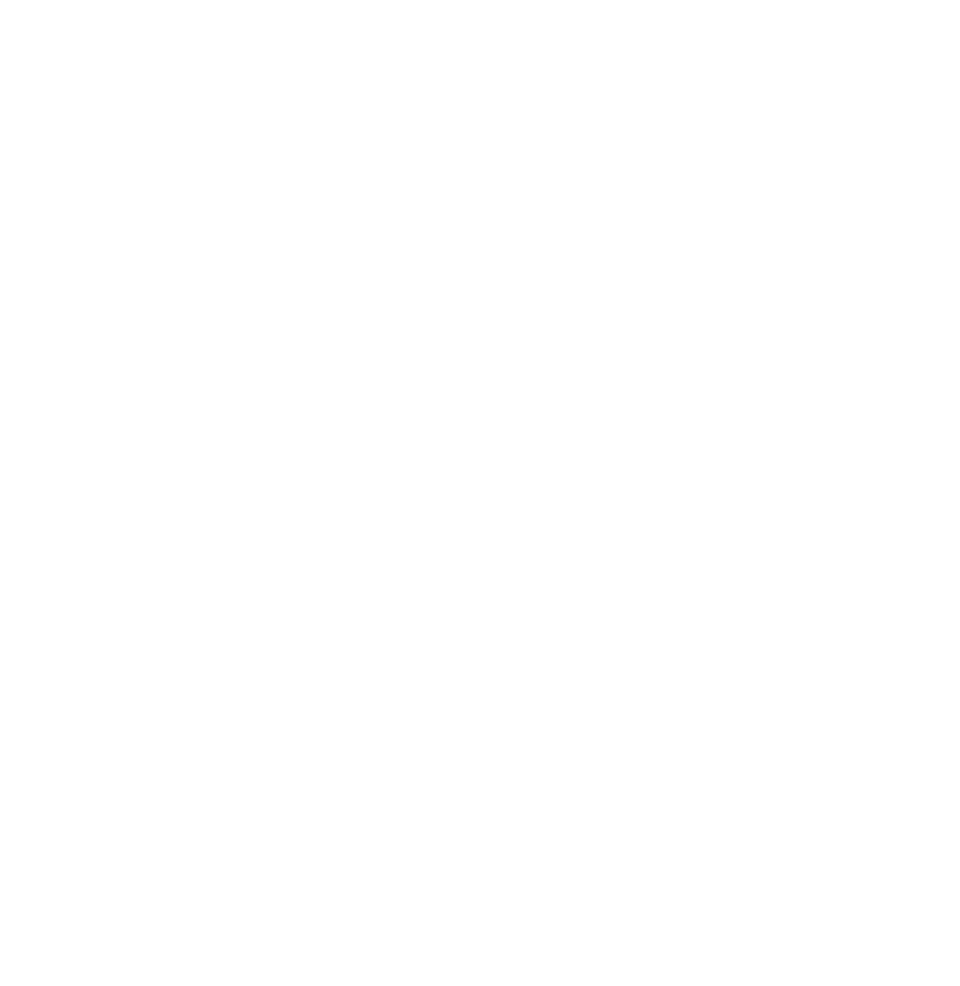
The main technical features of the press brake
The machine was set up with the SuperCustom configuration, which represents the ultimate in press brakes. Totally customisable in terms of open height, stroke, throat, and tool adapters height, it is the tailor-made suit that fits each customer’s product perfectly. It offers major advantages to those who produce mainly large box and tub products.
The bench-traverse span of this press brake is 700 mm, with a Y-axis stroke and throat of 500 mm. This machine is designed with an X-axis travel extension of 1200 mm, with a maximum stop at 1400 mm.
This press brake was equipped with the Tele-Link remote assistance function and the Industry 4.0 package.
The CNC is an ESA S 660 W type, mounted on a mobile console.
In addition, it has been equipped with a rear camera, positioned on top of the machine, and an additional dedicated monitor, on the pulpit. Its function is to provide an additional point of view for the operator, who would otherwise not be able to see the entire rear of the bending machine due to the clutter in the working area. In this way, the press brake can verify that the support of the workpiece on the machine is consistent and correct in every phase of work.
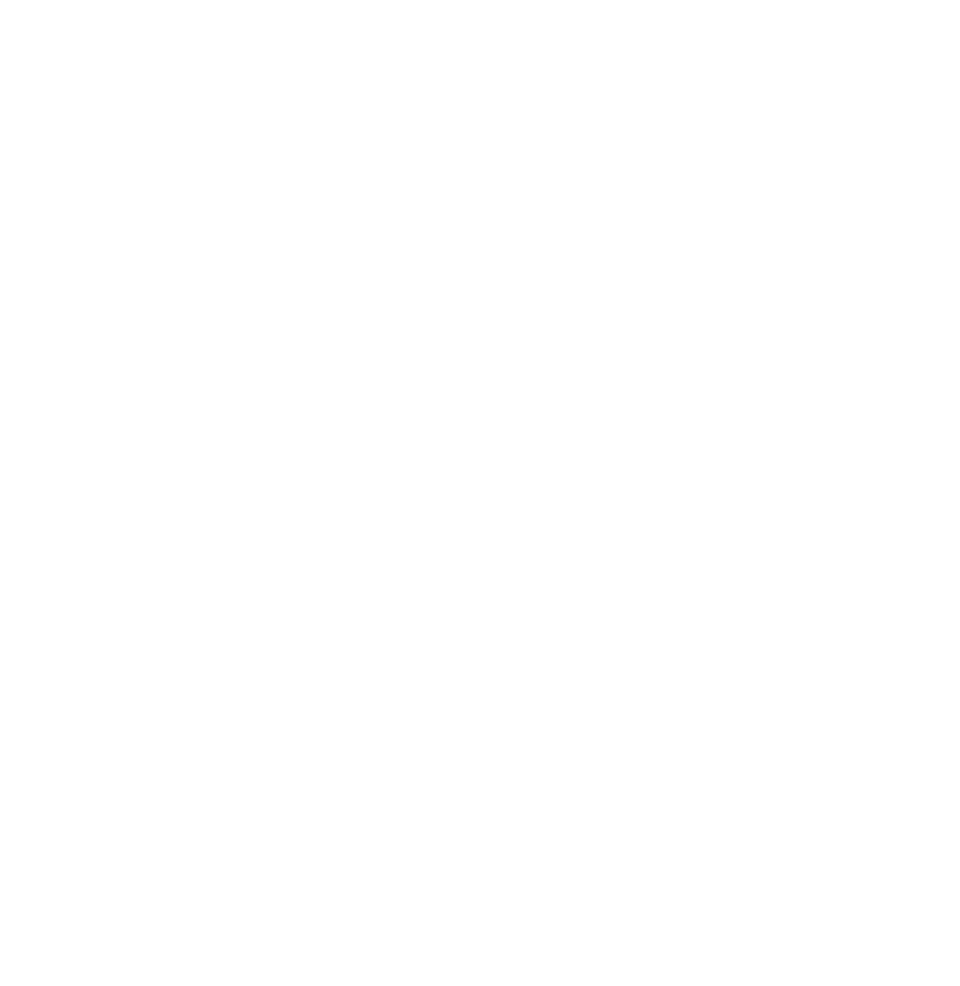
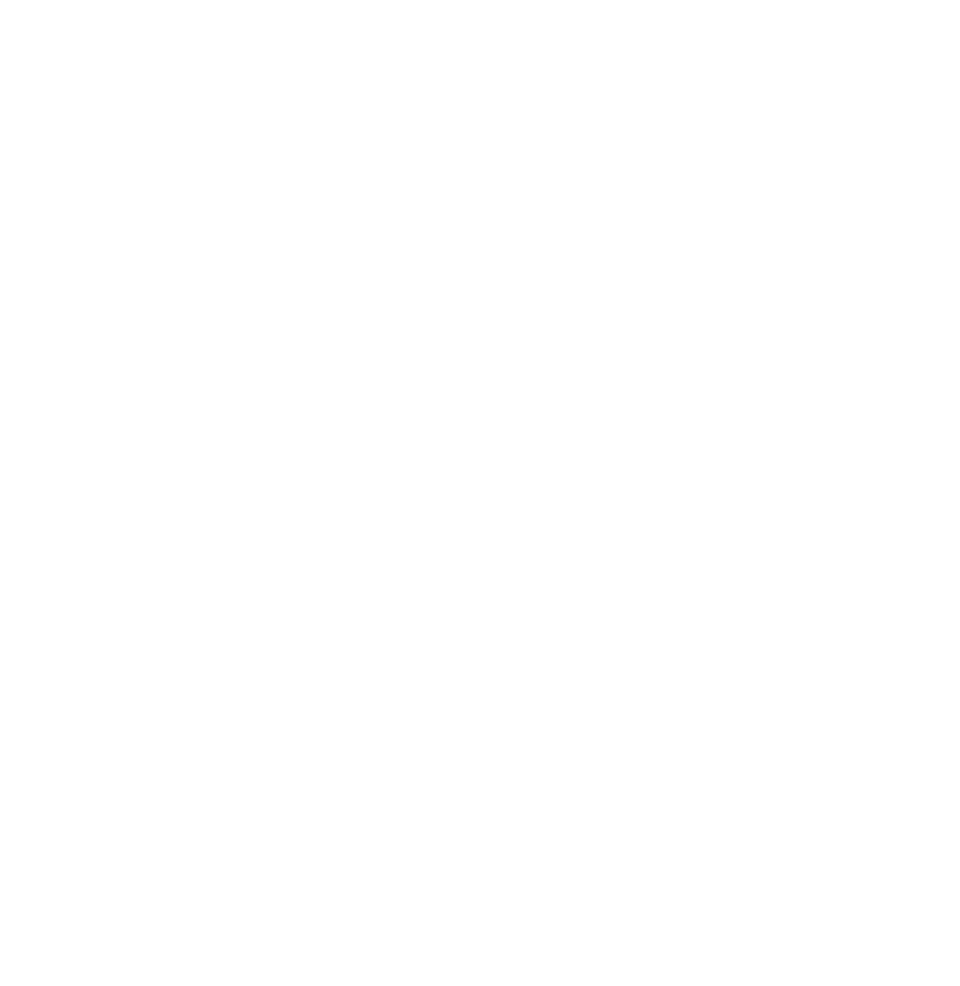
How to increase safety, precision and ergonomics in sheet metal bending
The safety device implemented is the DSP-AP Laser, which provides a reduction in speed and a decrease in cycle time. The system emits a visible laser beam that complies with EN12622 standards and ensures that the operator is protected from any danger of being crushed between the die and the punch. This solution is an improvement over old light barriers or single-beam guards that no longer meet current standards.
The customer then chose to install the Laser Line system for bending without reference. This system projects a laser beam onto the sheet metal at the bending line, making it possible to check that the part is in the correct bending position. It can be applied at a later stage, even on already installed press brakes, depending on the reference CNC version.
The machine has been equipped with two standard foot pedals (one on the right and one on the left), which are then connected by wiring to the press brake.
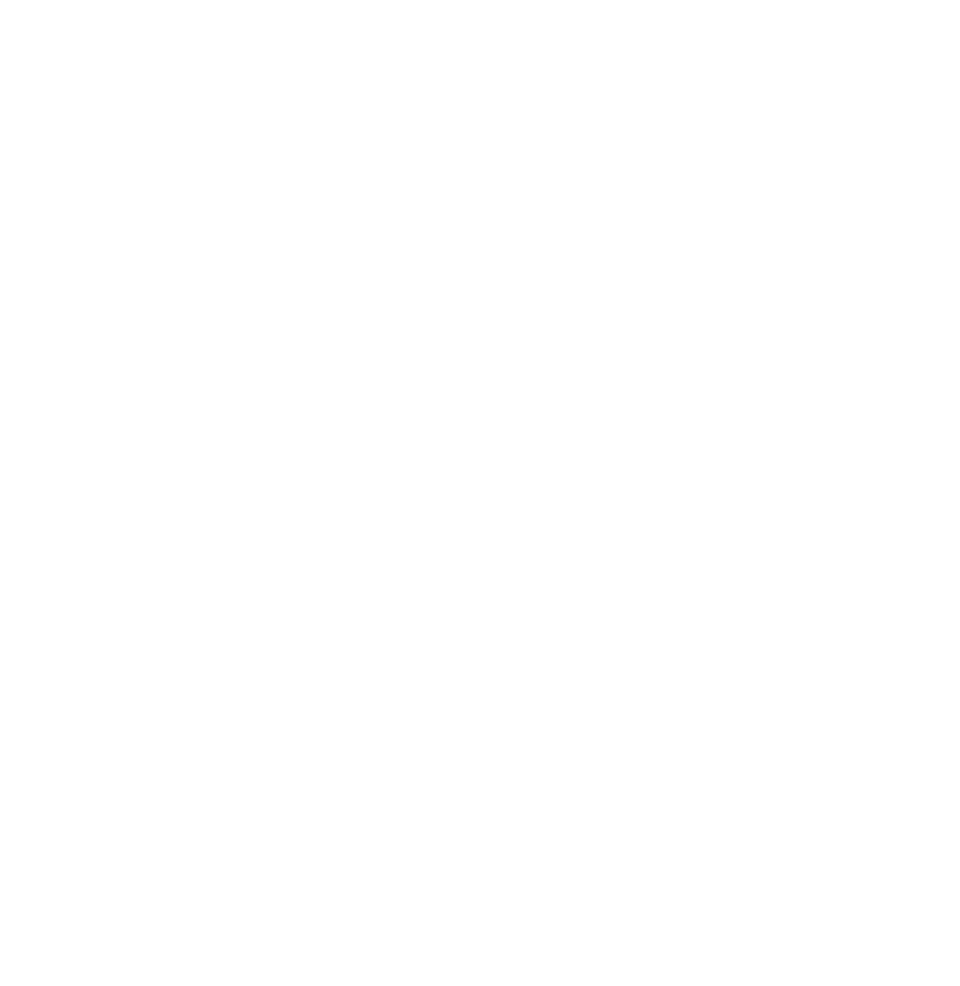
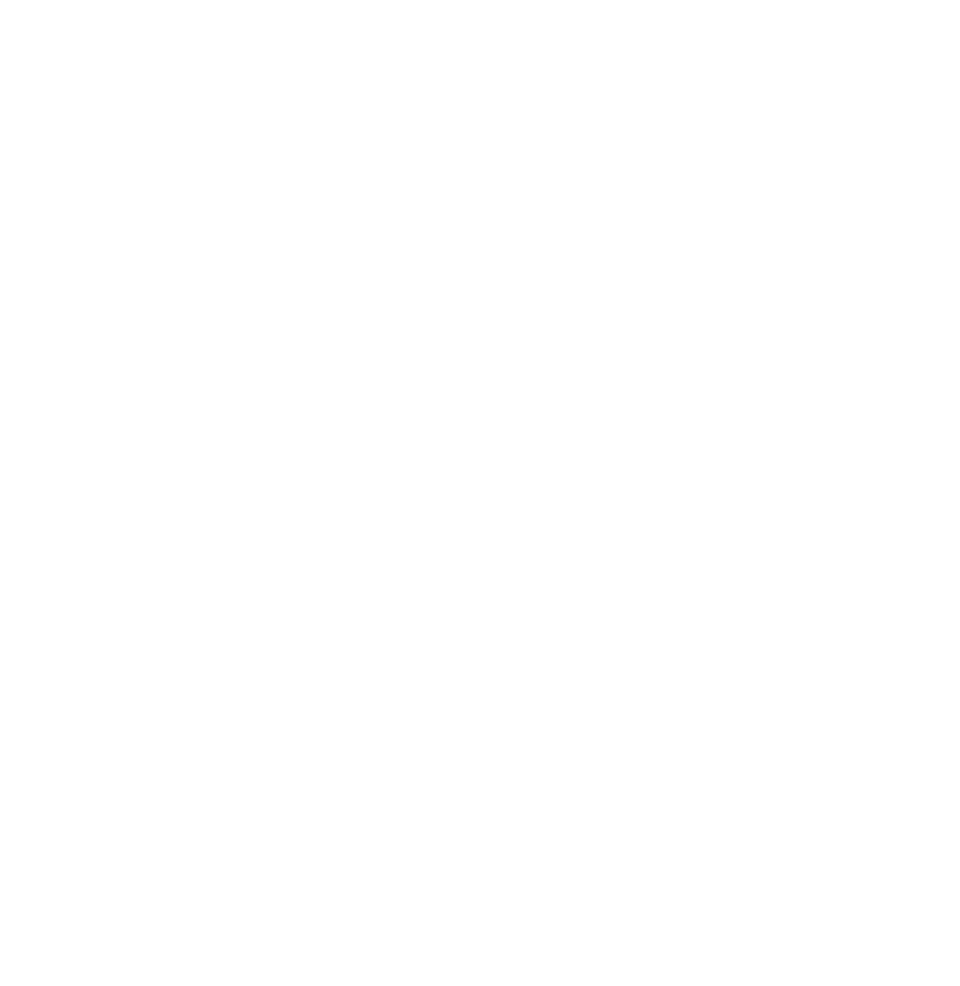
The press brake was implemented with the addition of a front sheet lifter with manual adjustment of the R-axis. This is a mobile sheet metal support placed at the front of the machine, at the height of the bending line, controlled by the CNC. It helps support the sheet metal during the bending process.
The backgauge has five CNC-controlled axes (X-R-Z1-Z2-X6), which in addition to the two standard axes also features the Z1 and Z2 axes. It is characterised by the addition of a stop on a backgauge reference, and a third vertical stop used to support workpieces during bending processes with a 70 mm radius.
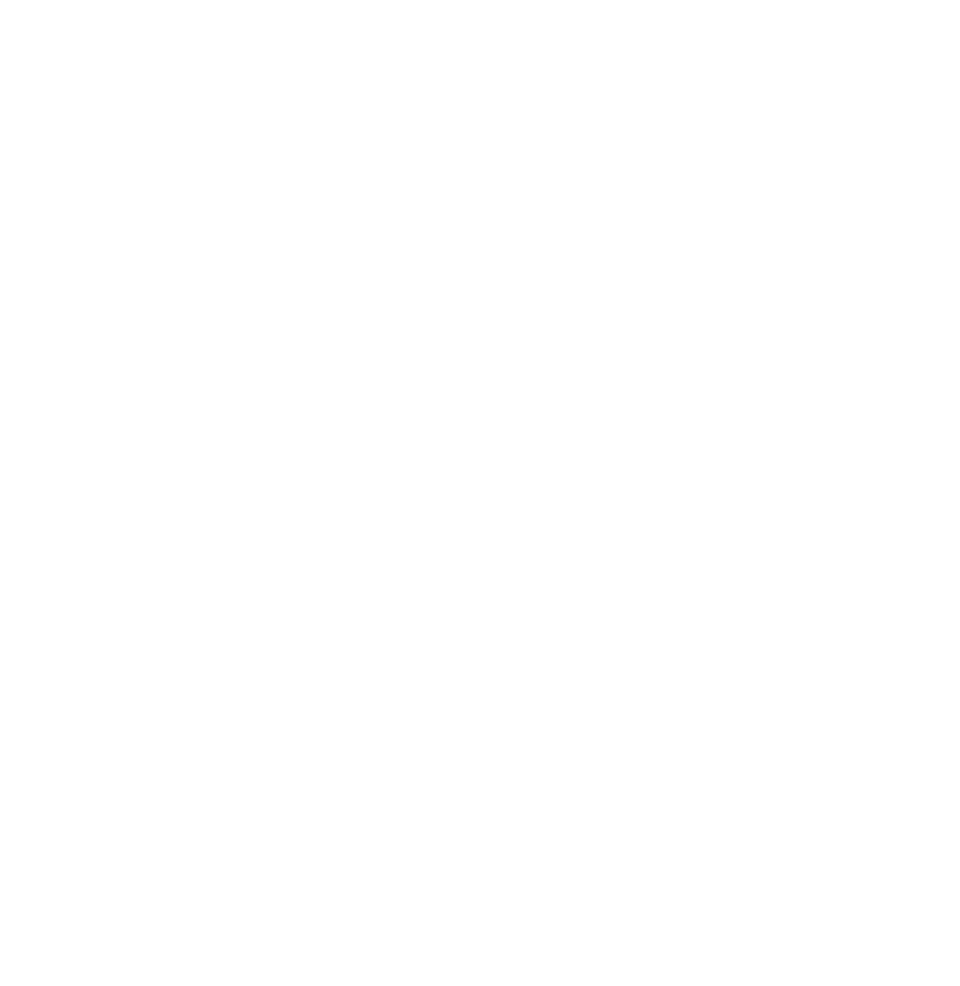
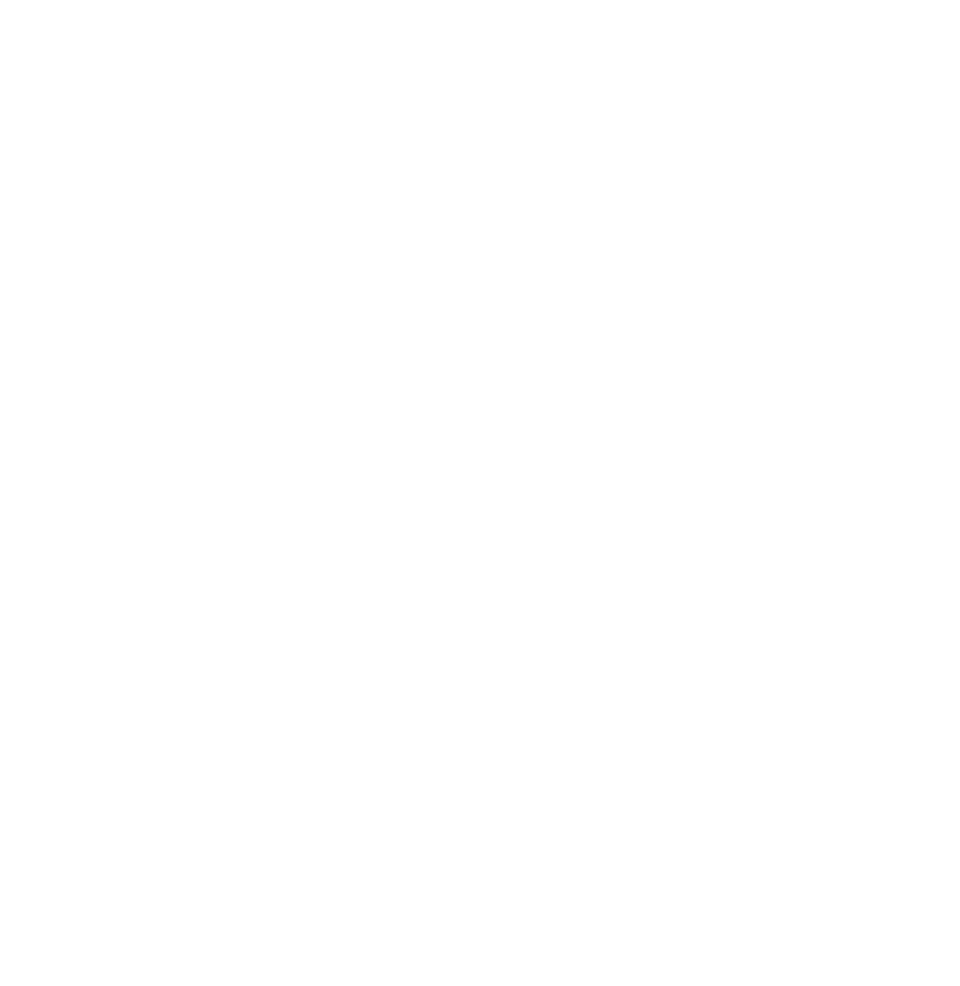
The choice of clamping system
In terms of clamping, the customer opted for:
- Gasparini AirSlide upper pneumatic clamping of 200 mm height for European type tools
self-aligning hydraulic clamping type H-GG for punches or intermediates - Gasparini lower pneumatic clamping
Press Brake customisations required
Each press brake is also equipped with a Syner-G remote control, which allows convenient access to a number of main functions:
- opening and closing the pneumatic clamping of the die and punch
- opening and closing of the hydraulic intermediate clamping
- calibration of the GPS4 bending angle control system sensor
- parking the motorised photocells and the rear register
This machine is also mechanically prepared for the installation of the GPS4 angle control system, and has a drive bar for tool positioning.
Gasparini Industries has always focused on the needs of each customer when designing its press brakes. In this case, it has experimented with a new solution to overcome the problem of pieces of a certain size colliding with the upper beam. In fact, protective strips were applied to the beam. In this way, longer sheets or particular box sections do not collide directly with it and the machine remains protected from scratches and other resulting damage.
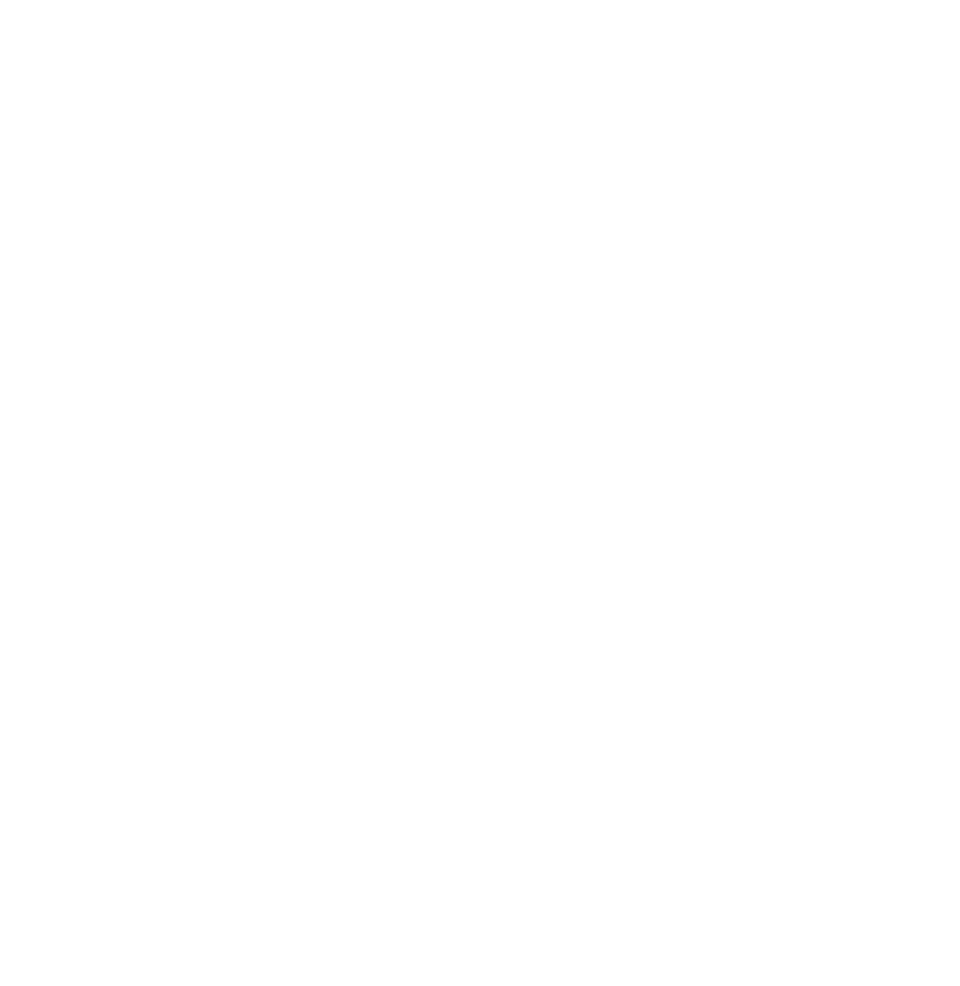
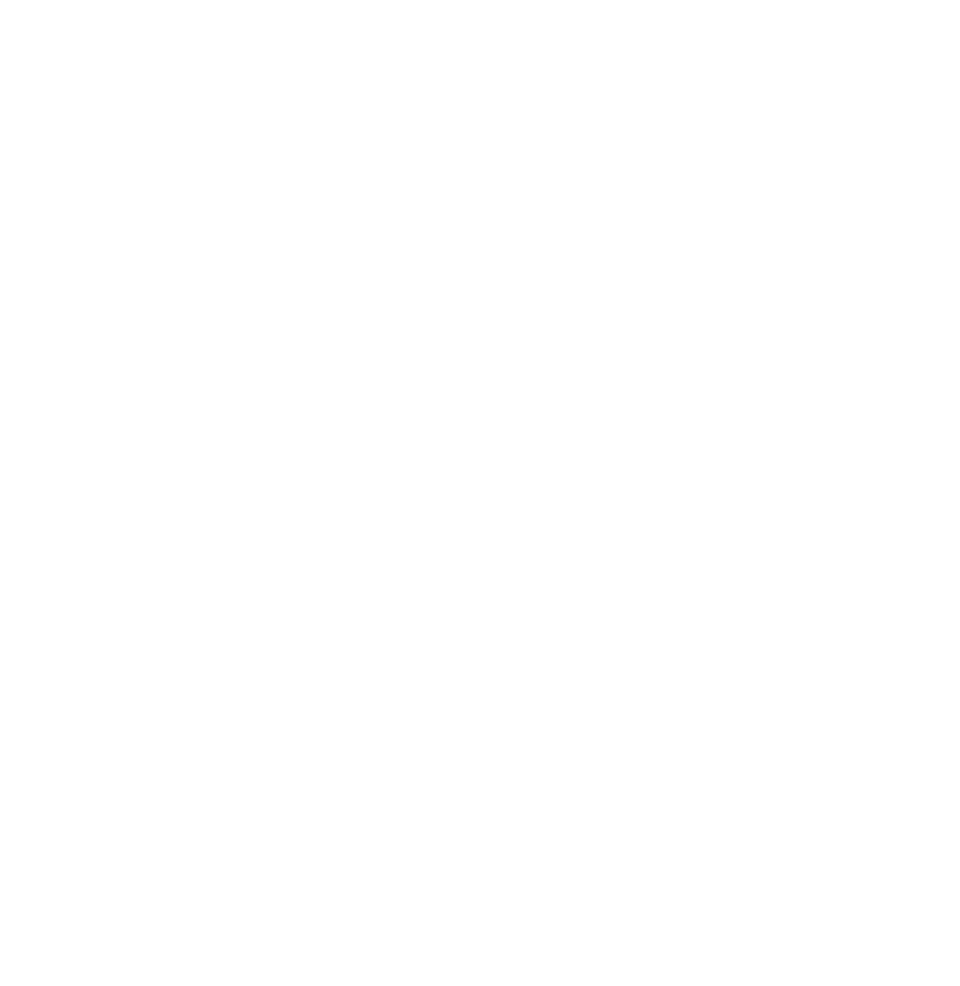
This press brake is equipped with:
- the E-Reflex Deformation Compensation System, which ensures the control of the bending of the structure through a network of sensors, located both inside the machine and in the hydraulic system;
- the Gasparini Adaptive Crowning System, which, using two precision sensors, detects the deformation of the upper beam and drives the lower accordingly.