The main technical features of the press brake
This press brake is equipped with Gasparini Adaptive Crowning System and the E-Reflex side frames deflection compensation system. The combination of these two systems allows excellent results in terms of quality, precision and repeatability of the parts to be bent. Thanks to the camber, in fact, the two crosspieces are perfectly parallel and it is possible to obtain total control of the angle. There is no need to set any values: the press brake gets this directly from its sensors. The material can change completely from one part to the next and the bending machine will always react optimally. The E-Reflex then monitors the bending of the structure thanks to a network of sensors in the press brake and hydraulics. The error is measured and compared with the ram position and oil pressure. We can thus calculate the actual height at which the punch is located, regardless of deformations.
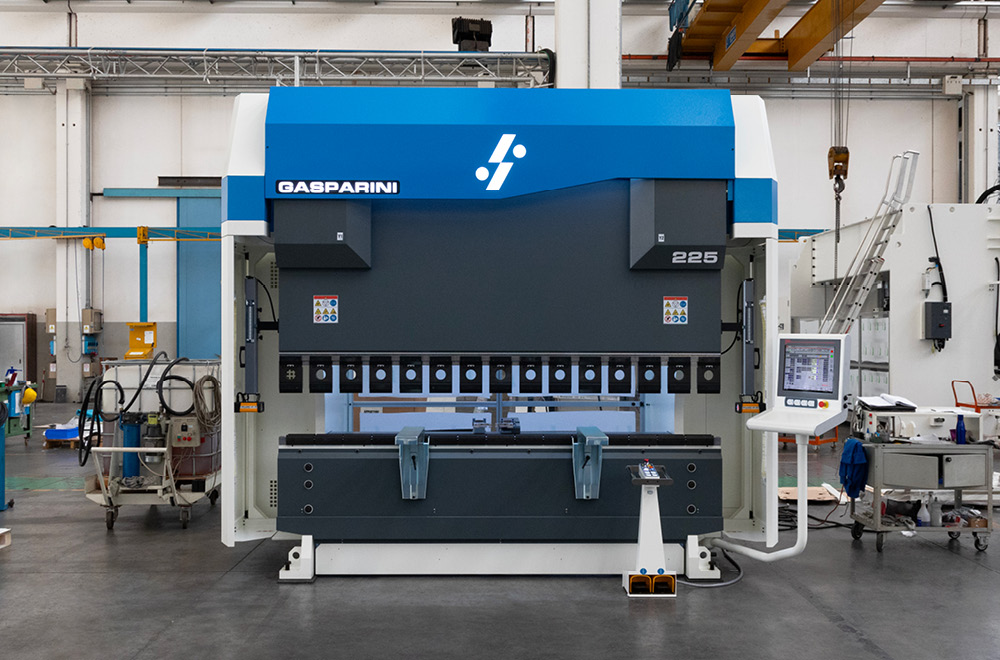
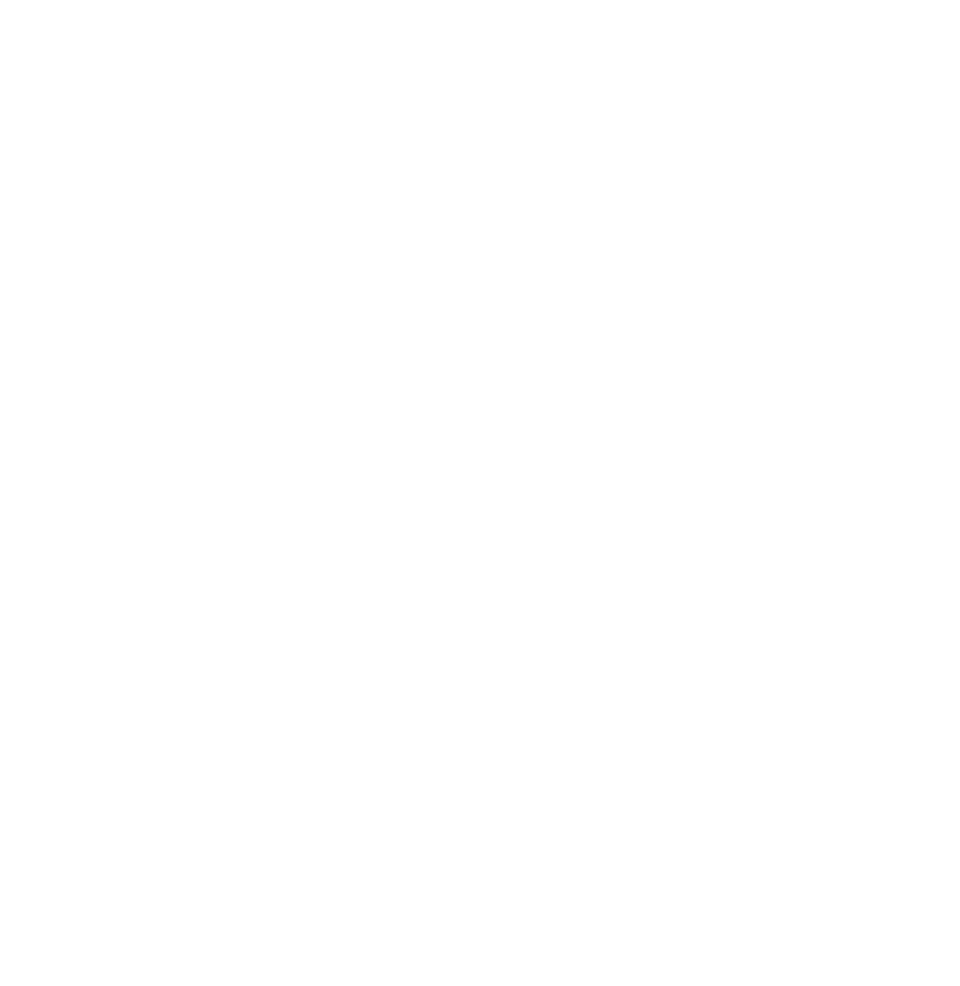
Which accessories to choose to increase the safety of a press brake
The clamping system of this machine consists of:
- manual clamping of punches with standard intermediate heights of 100 mm and 200 mm
- manual lower clamping
Precision and ergonomics of the press during bending: how we achieved them
The backgauge has 5 axes (X-R-Z1-Z2-X6) controlled by CNC. In addition, it has been implemented with an additional stop on one of the references and an F function, which allows the references to be moved from the front of the machine, without having to access the rear. This results in significant time savings and a safety benefit.
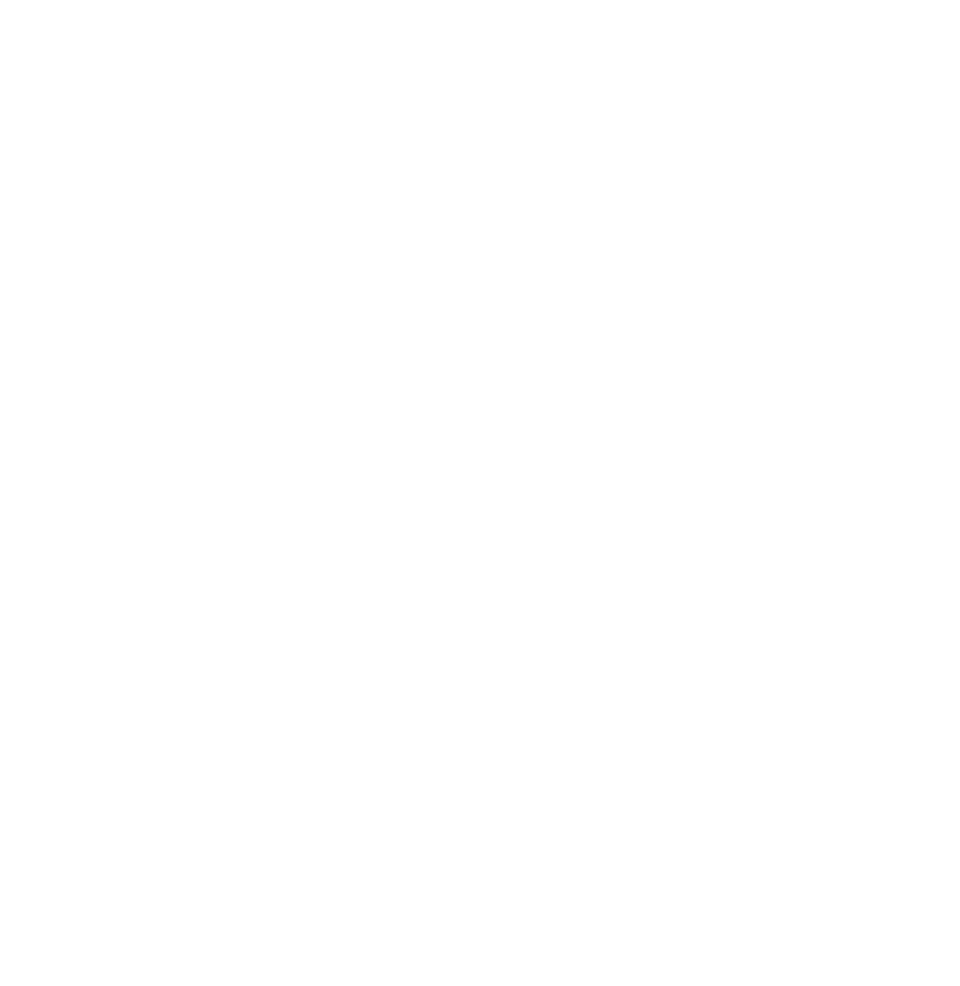
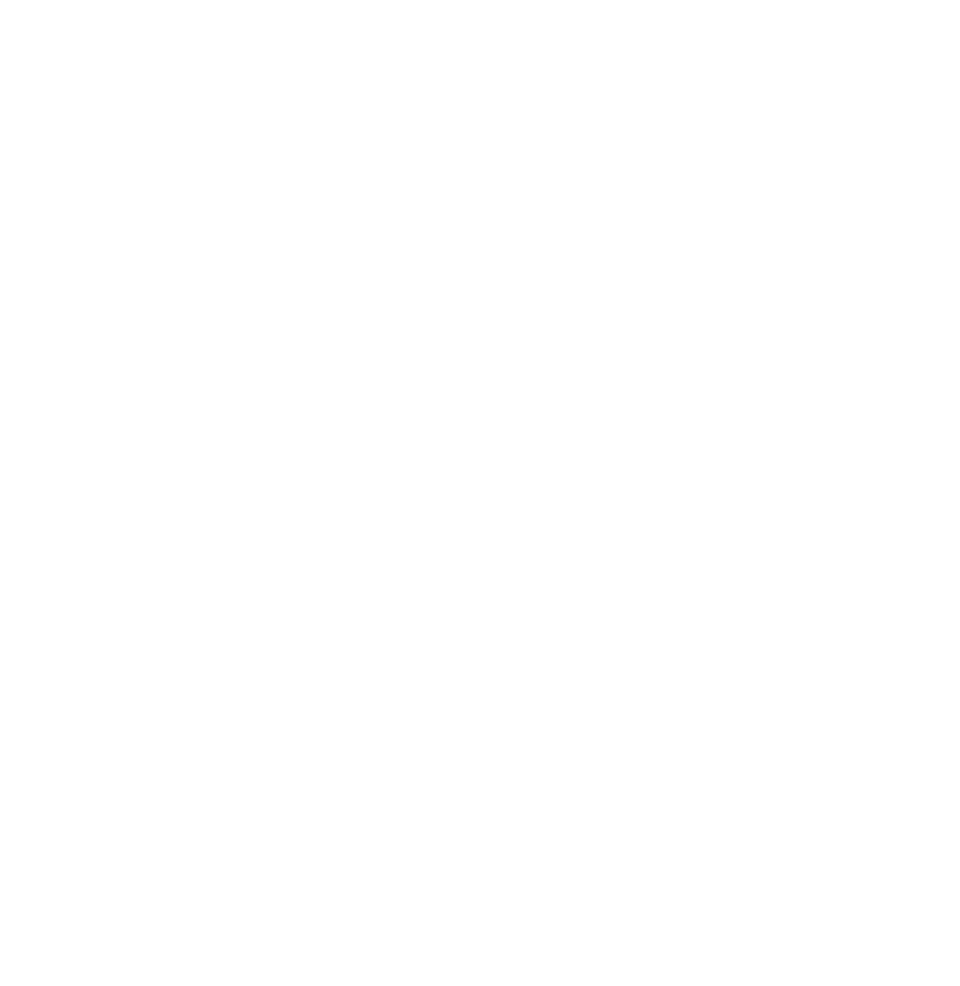
Automation and remote assistance: what advantages
This press brake was equipped with the Tele-Link remote service function and the Industry 4.0 package.
It was equipped with the CNC ESA S 660 W, with 3D visualisation. This CNC consists of an integrated Windows PC and a 19″ LCD HD Multitouch super-screen and can manage machines with up to 64 axes.
Customisation of the press requested by the company
The safety system installed is of the Laser DSP-AP type, which generates a visible laser beam conforming to EN12622. The beam protects the operator from the danger of crushing between punch and die.
This device allows the speed change point to be lowered by up to 4 mm from the plate. The result is that the upper cross beam moves at high speed for longer, limiting to a minimum the part of the bending sequence where the speed is reduced.
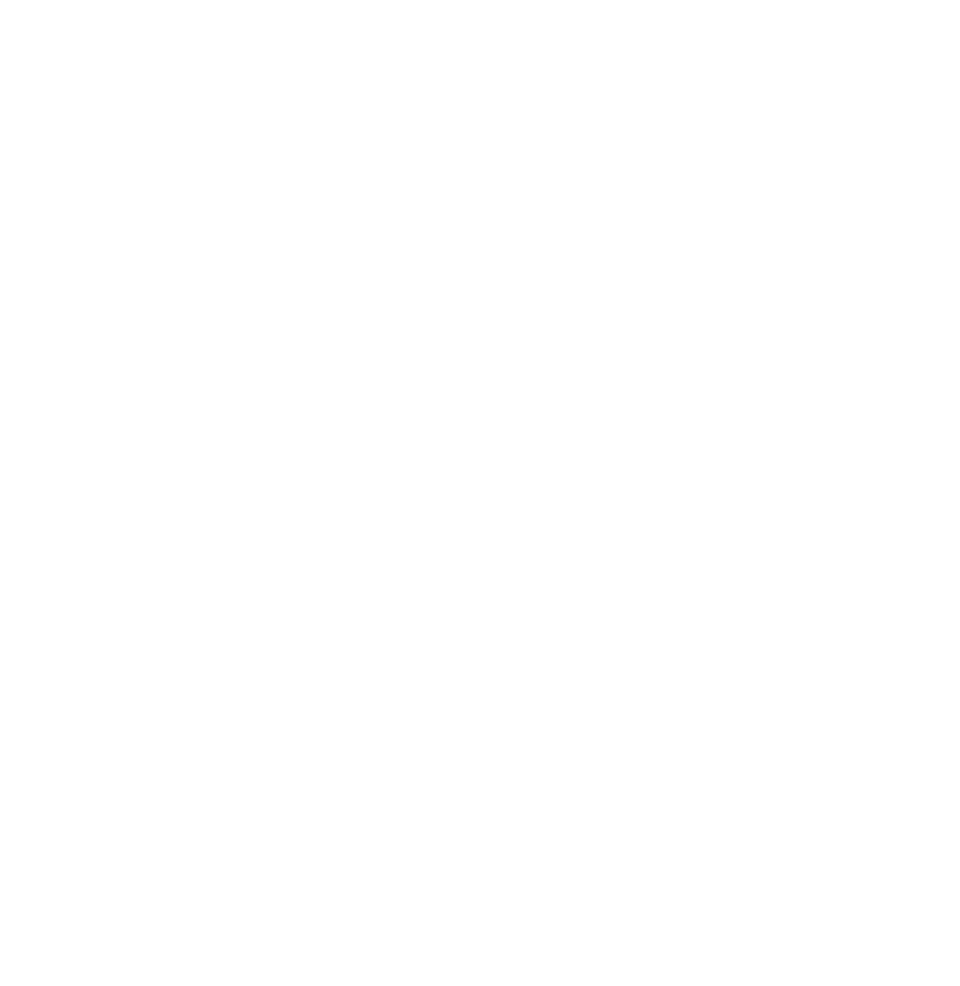
The customer chose to add:
- two standard front supports
- a standard footboard
- LED lighting of the working area