Material
Sheet metal is an anisotropic material, i.e. its properties are not the same in all directions. As all press brake operators worth their salt know, its behaviour changes depending on the direction of rolling. It is therefore useful to cut all the pieces in the same direction, or to divide them into pieces cut parallel to the fiber and perpendicular to the fiber. Nesting with variable orientation is not recommended. We may save sheet metal by fitting an extra piece in the sheet, but we risk wasting parts and time because we don’t get the right angle when bending.
It is also useful to divide the pieces according to the area. The internal tensions of the sheet change between the centre and the edges, due to the stresses introduced by the rolling.
Do not mix pieces cut from different batches of sheet metal or different packs. The inevitable differences between one casting and another mean variable hardness and elasticity, which can affect the final result.
In these cases, a real-time angle control system and adaptive crowning can help us obtain constant angles even if the pieces have been cut in a different direction.
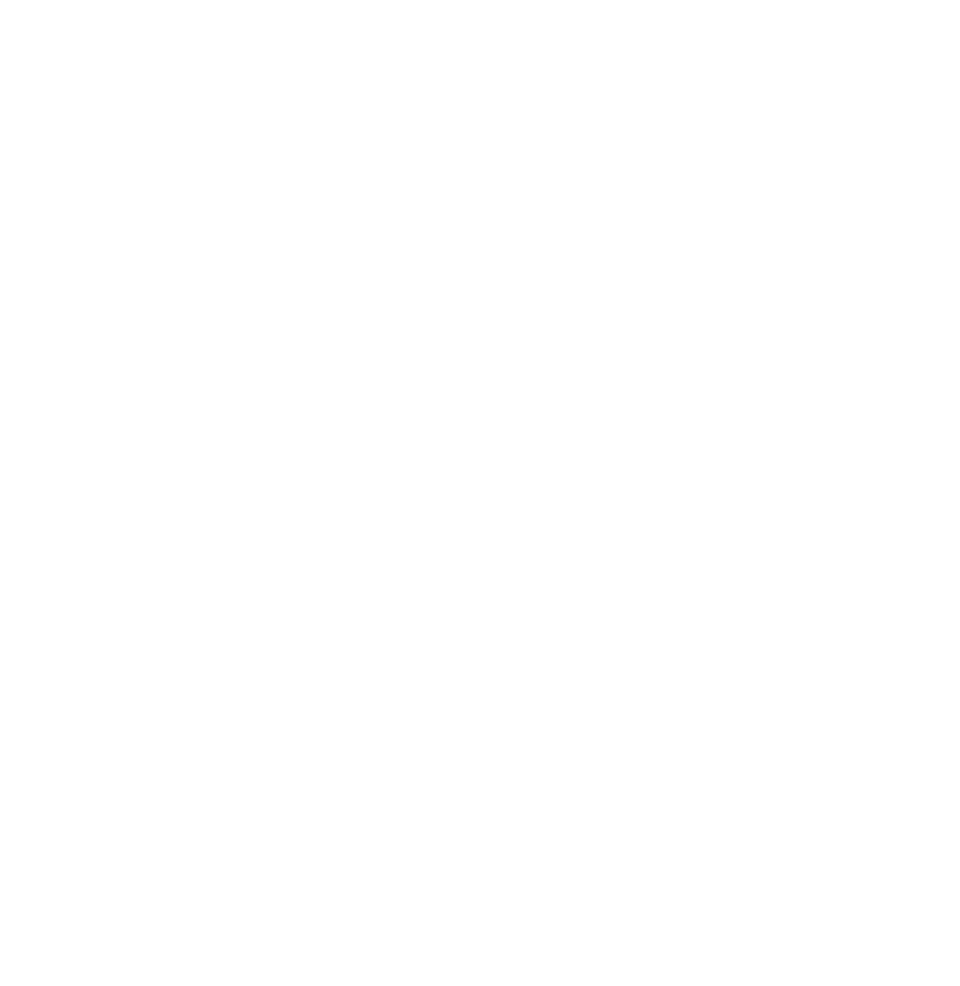
Micro joints
In certain cases, especially with small pieces, it is mandatory to leave the so-called microjunctions, in order to prevent the cut pieces from falling into the bed or from tipping over, with the risk of collision with the cutting head. These microjunctions leave small spikes on the edge, which can make it difficult to properly rest (G) on the backgauge fingers. If possible, put microjunctions where they do not cause difficulties (H).
Alignment jigs
If your press brake does not have the X5 and X6 axes for oblique bends, or if your part (A) has an irregular shape that makes it difficult to rest it safely, you can have your laser operator cut a piece of the scrap (D) and attach it to the backgauge stops (C). In this way we place the piece on the opposite shape and be sure to have an optimal alignment with the bending axis (B).
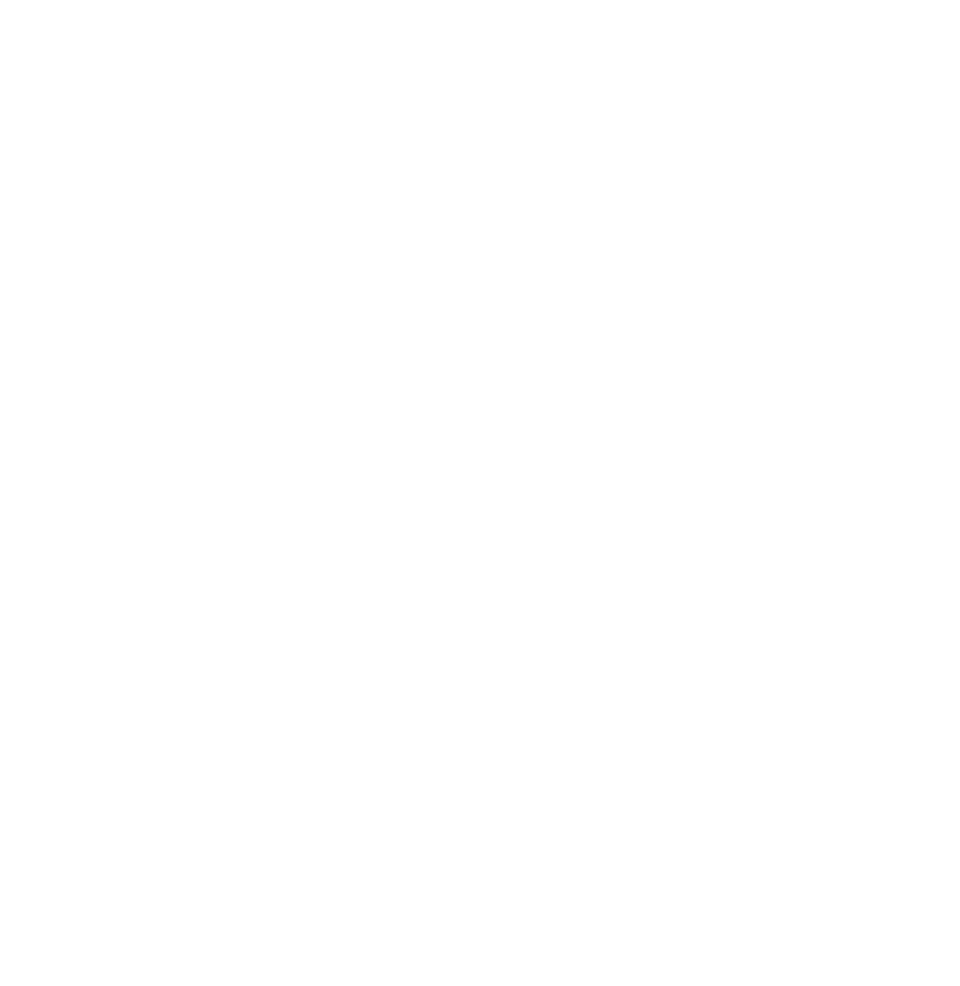
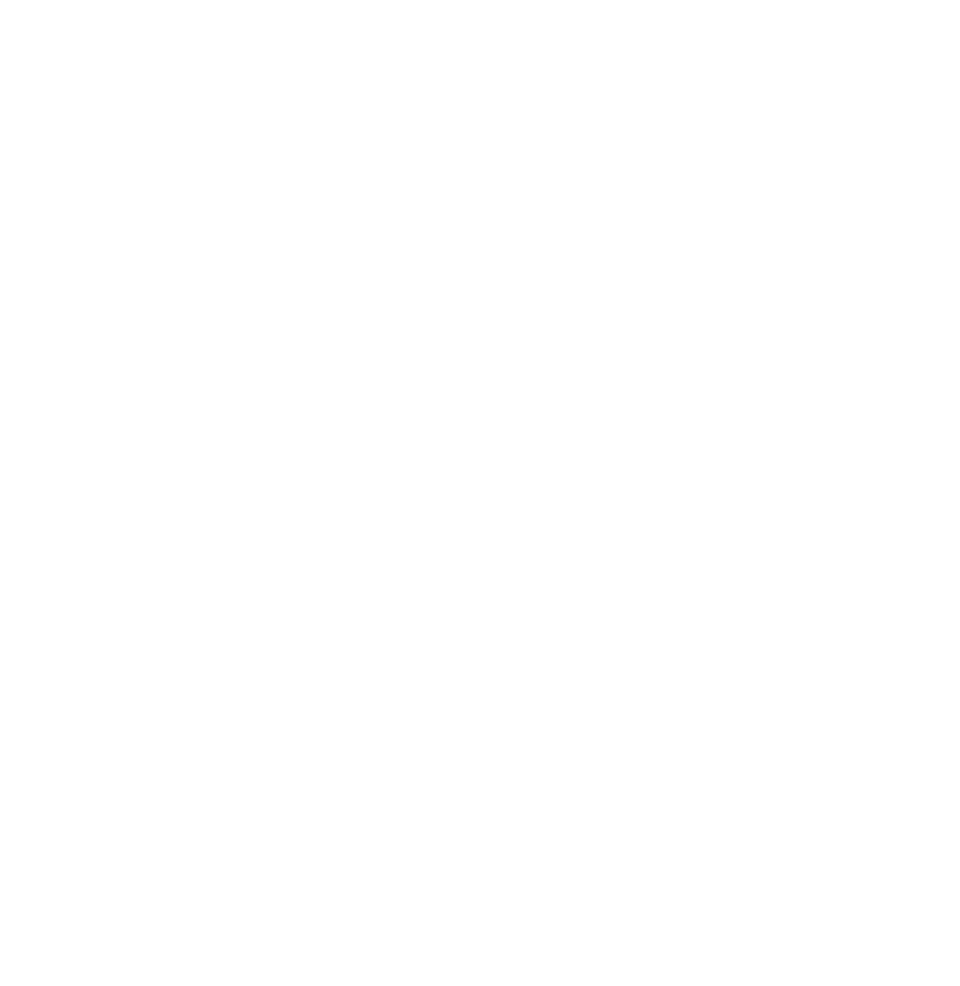
Bending lines
Here, too, we can partially make up for the lack of the relative X axes by marking the bending lines with the laser. If it is not possible to trace the surface, we can have marks placed on the edges (F). They should preferably be outwards rather than inwards to avoid cracking. Should you be forced to use inward-facing marks, avoid sharp notches (E). A LaserLine device can help us positioning the part correctly on the bending line.
Handling
Unloading the pieces from the bed keeping them well stacked and in order helps a lot with the bending, and also allows you to reduce damage such as distorted or scratched pieces, especially with delicate finishes and materials.
Count the pieces before handing over to bending. It may seem trivial, but with large lots a piece or two may easily missing, especially if they are small. Stopping and resuming cutting later may also cause you to lose count. Less time is wasted on cutting a missing piece on the fly with the drawing still in the machine and the sheet still on the bed, rather than having to do so maybe days later with the risk of no longer having sheet available.
Check the piece: before sending an entire lot to bending, make sure that it corresponds to the one indicated on the order sheet or in the technical drawing, to avoid problems and setbacks.
Split orders and associate each order with its drawing or worksheet, without heaping all the drawings together or, worse still, without any drawing at all.
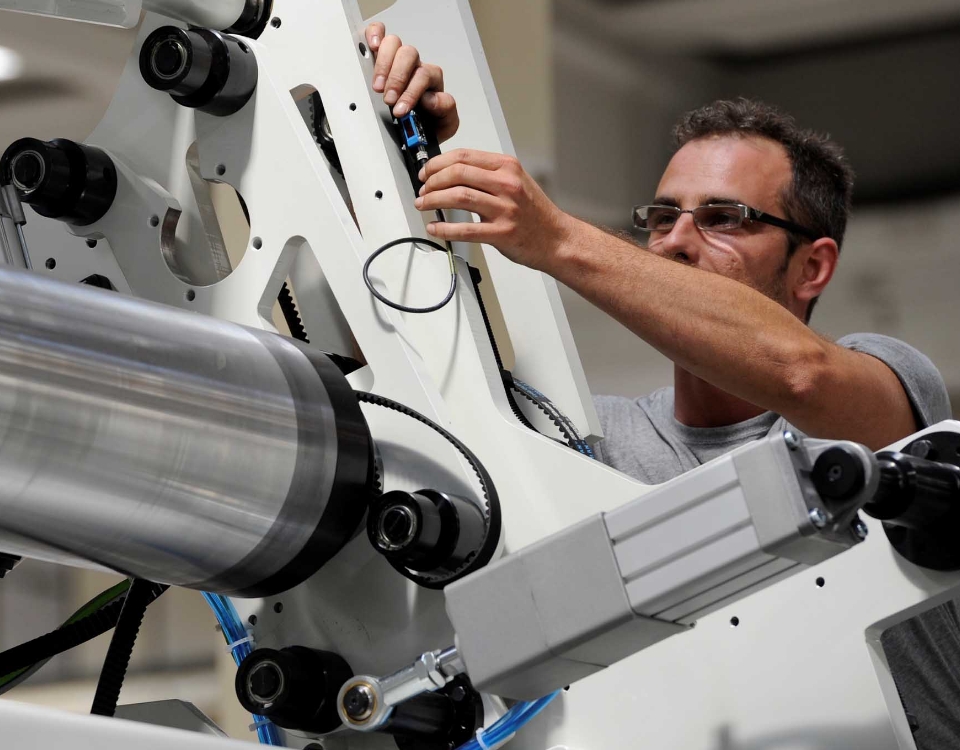
Design
Correctly calculate the bend deduction and the correct flat length to be cut according to the material and tools. Here it is essential to discuss with the press brake operator, and to calculate the specific K-factor of that bend, doing preliminary tests. We have provided a tool to calculate bend allowance, bend deduction, and the K-factor. You can find them on www.gasparini.com in the Calculators section.
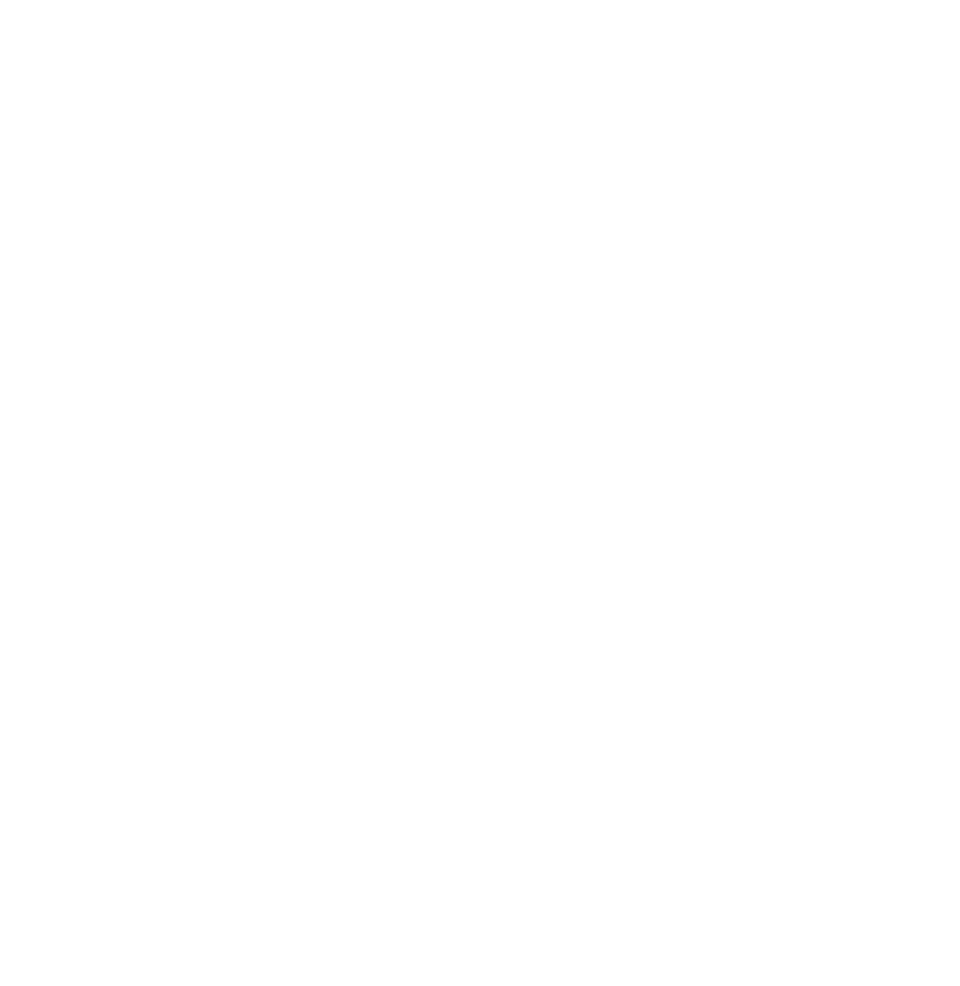
Insert the necessary bend reliefs into the drawing to avoid cracks and tears. Maintain adequate distances (at least the bend radius plus 2 times the thickness) between the bend line and holes, ridges, louvers, threads, etc. Don’t forget corner reliefs.
Take into account the need for over-bending to compensate for springback. If we have a flange that comes into contact with another part of the piece, we must take into account that to get to the desired angle we will have to bend to a more closed angle, with the risk of colliding.