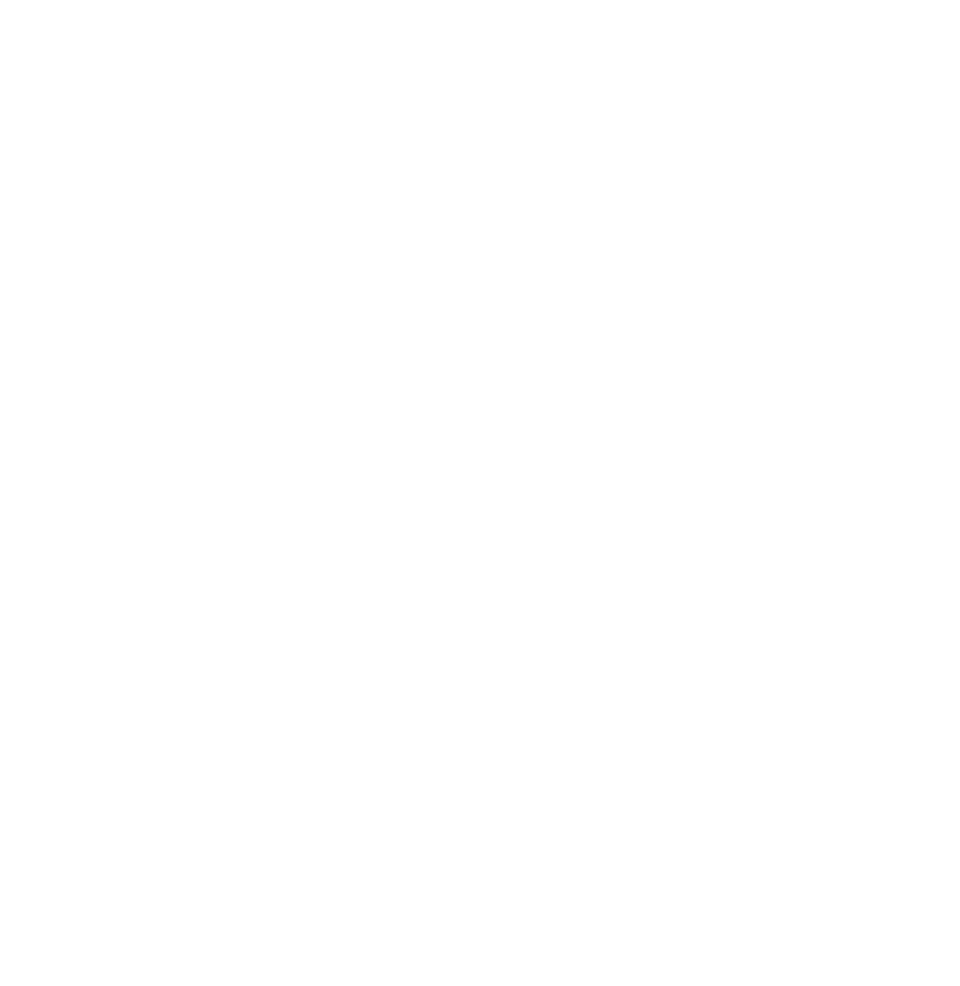
Main features
This press brake comes in the Easy design. The customer chose to equip it with the E-Reflex Deformation Compensation System to control the bending of the structure thanks to a network of sensors in the machine and hydraulic system. The error is measured and compared with the position of the crosshead and the oil pressure, allowing the actual height at which the punch is located to be calculated, regardless of the deformations.
CNC and software
The CNC is the Delem DA-69S, with Delem Profile-S 3D offline software.
The DA-69S offers 2D and 3D programming including automatic bend sequence calculation and collision detection. Full machine configuration in 3D with multiple tool stations providing real feedback on feasibility and product handling. Highly effective control algorithms optimise the machine cycle and minimise set-up times.
The customer also chose to set up the press brake with the Tele-Link remote service function.
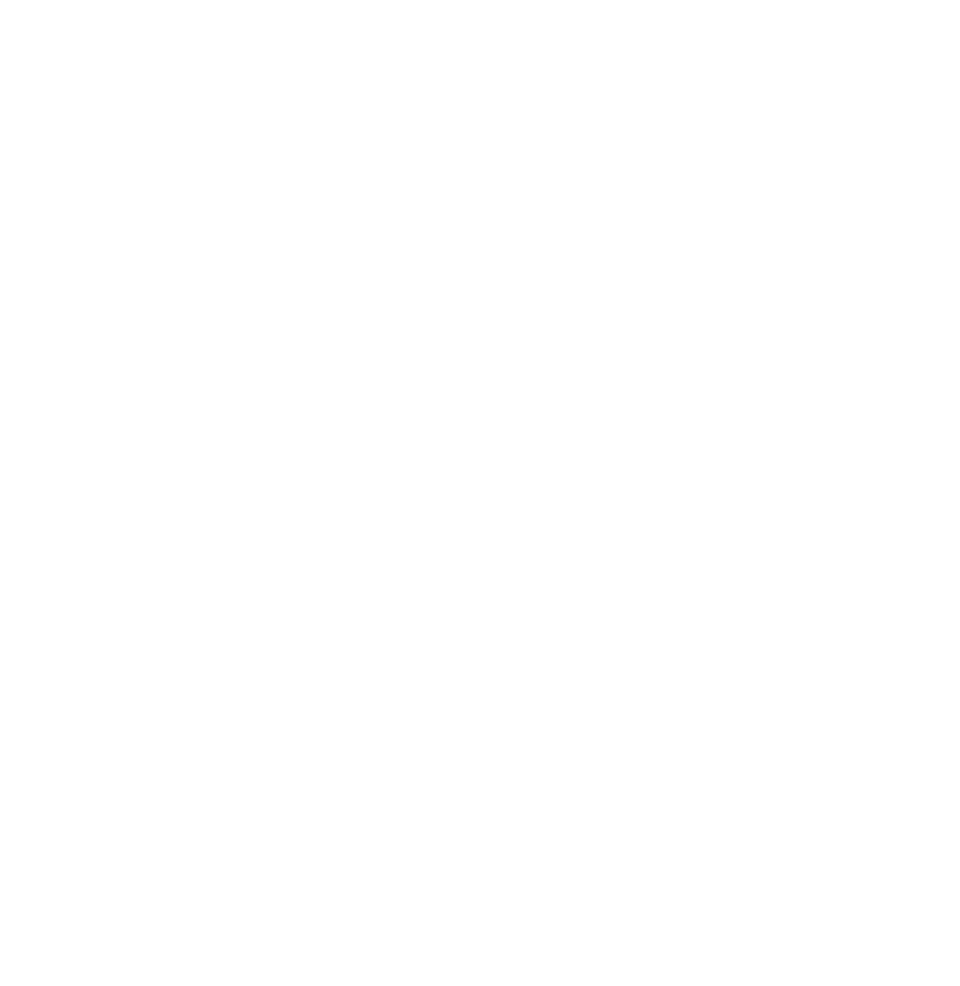
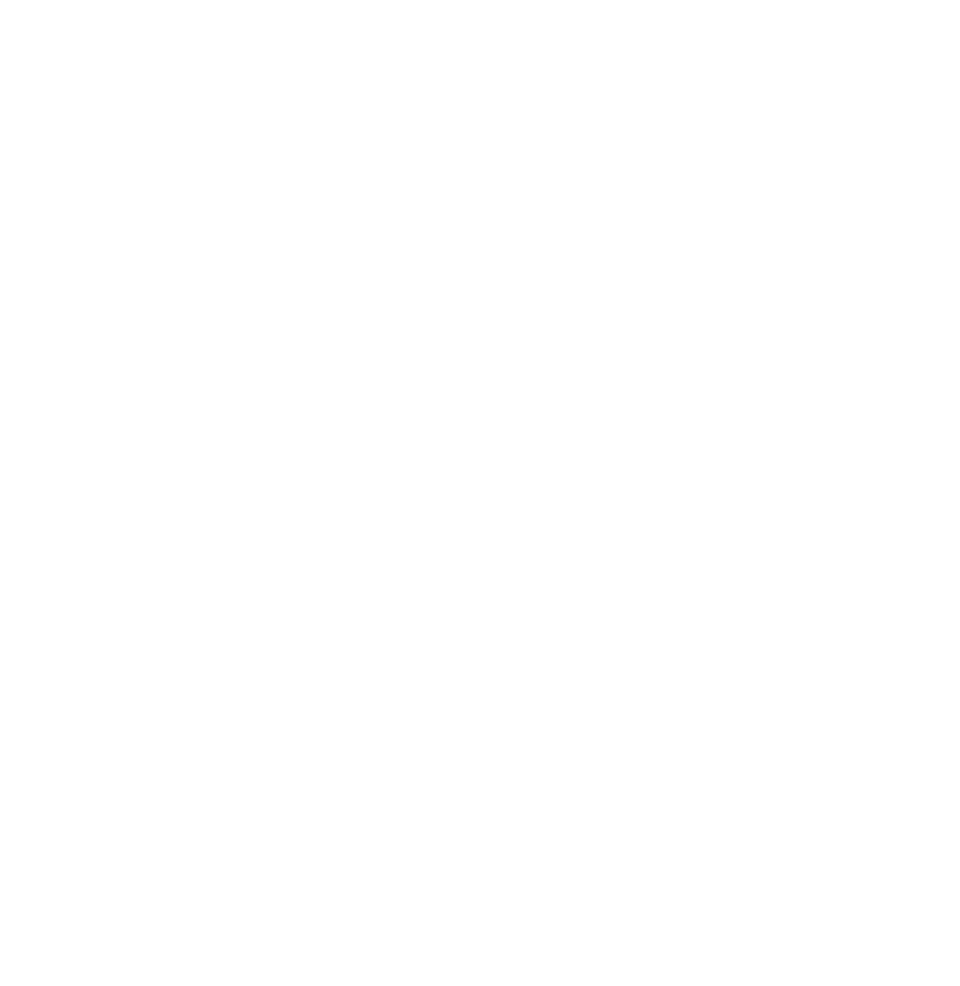
Backgauge
The CNC-controlled 5-axis backgauge (X-R-Z1-Z2-X6) offers enhanced versatility over the traditional two standard axes, thanks to the addition of the Z1 and Z2 axes. These additions allow greater flexibility when machining different parts, allowing the lateral movement of references to easily handle materials of different lengths or work on multiple stations.
It also has an additional stop on a register reference.
Clamping system
The customer chose to configure this machine with quick-release, self-aligning Toolever lever intermediates with a height of 100 mm.
Thanks to the tool-free lever operation, these intermediates save a great deal of time compared to conventional screw clamps.
- 100 mm height: no program changes required.
- Front centring wedges: intermediate contact without gaps.
- Double clamping with front clamping for mounting inverted tools.
- Opening and closing without special tools, just an ordinary spanner or screwdriver.
- Tools remain in a secure position even with the locks open.
- Self-aligning: during closing, the punches are lifted and pushed against the intermediate, eliminating the need for preliminary bending.
- They also support segmented punches up to 10 mm.
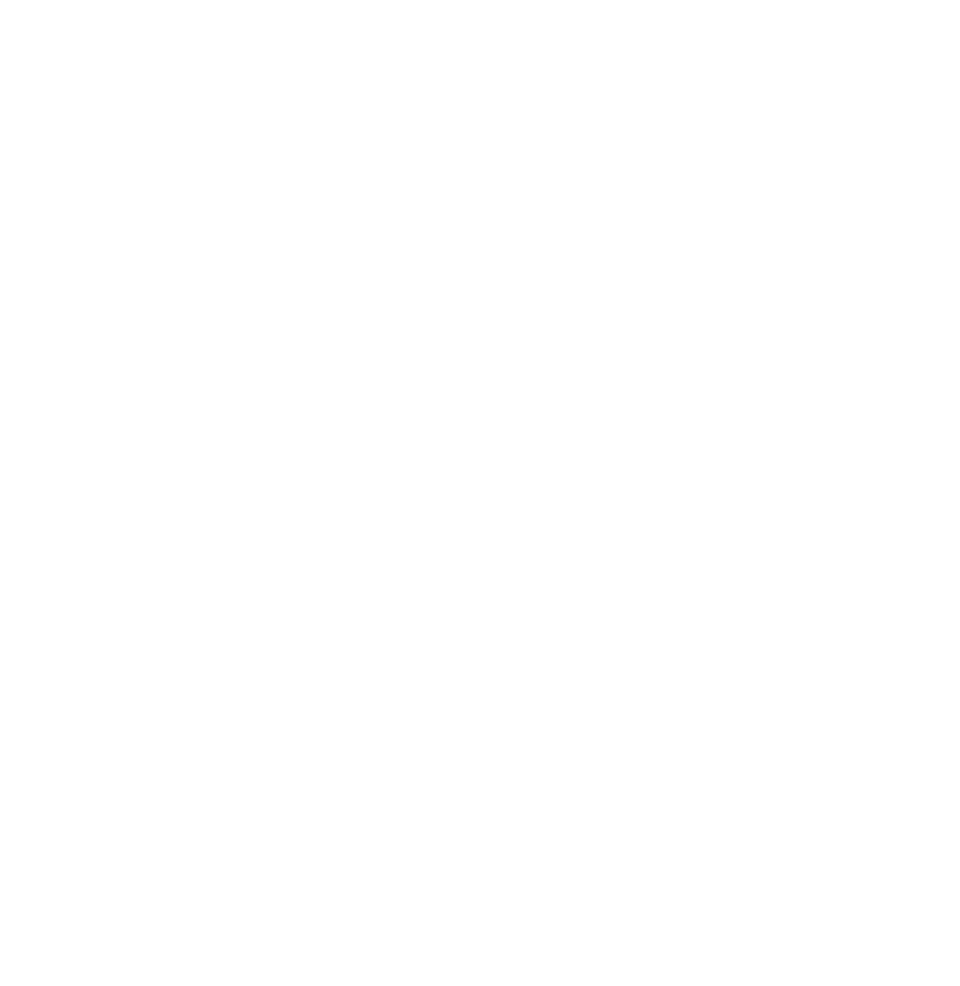
Other systems and accessories
F.D.M.’s X-press 80/2000 also features:
- 2 sliding front supports
- DSP-AP laser safety system with PLC
- 1 standard footpedal
- LED lighting of the working area
- Industry 4.0 package
- ECO energy-saving package