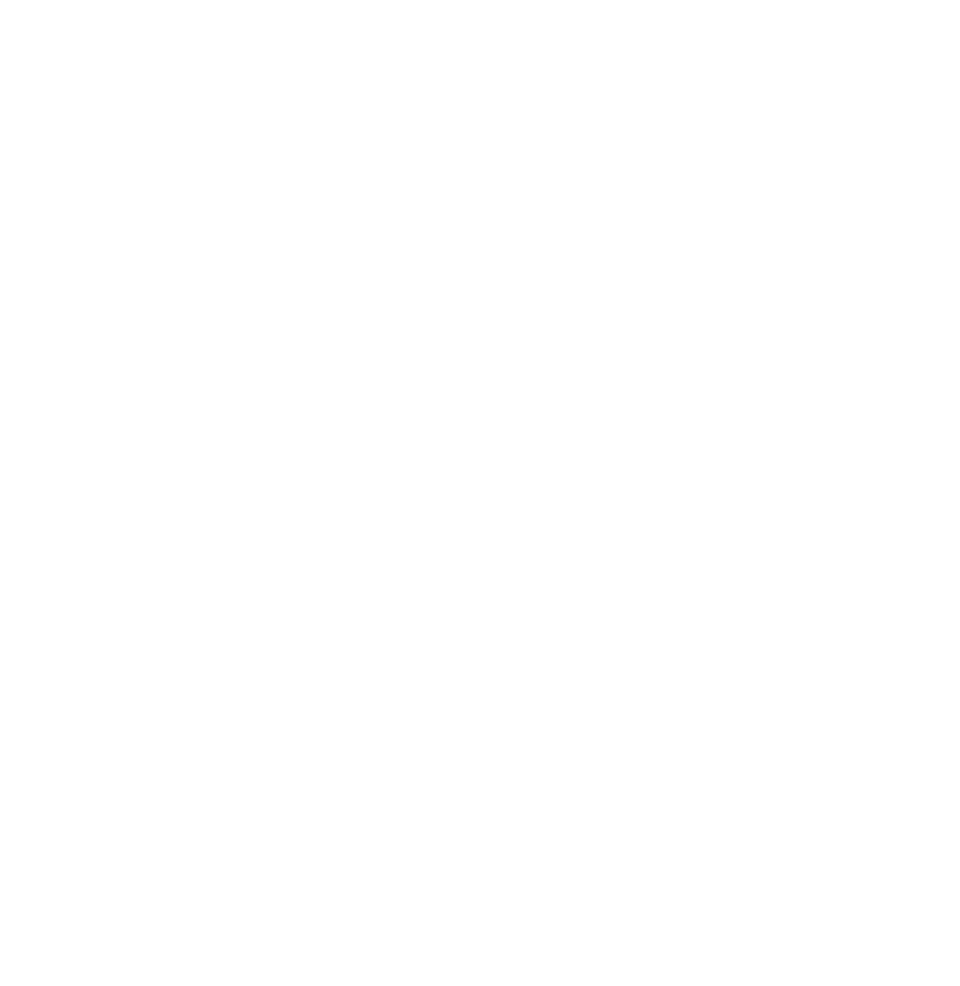
E-Reflex Deformation Compensation System
The E-Reflex system is designed to automatically compensate for bending of the side frames of the press brake during the entire bending process. Using a network of sensors, E-Reflex detects and measures structural deformations in real time, comparing this information with the position of the crosshead and the oil pressure. This makes it possible to precisely calculate the actual position of the punch, while keeping the bending angle constant, regardless of the variables of length, thickness or characteristics of the processed material.
CNC & Software
The CNC is the Delem DA-66S, with Delem Profile Lite SL 2D offline software.
DA-66S features:
- High resolution 24’ touch screen (16:9)
- 3D visualisation of bending sequence
- 2D programming
- DXF file import
- 3D visualisation of offline programme
- Offline software included: Profile-SL
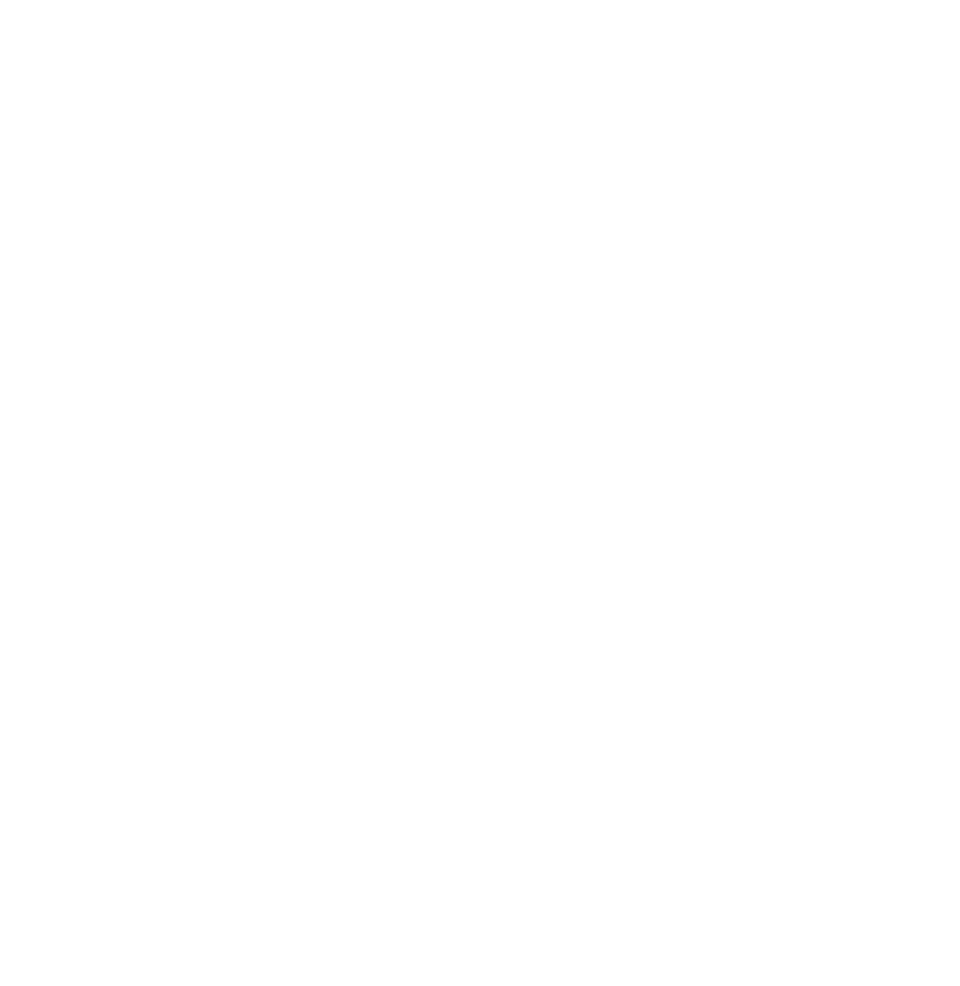
Iris Plus safety laser system
This press brake is equipped with the Iris Plus laser safety system, which uses a two-dimensional die sensor to monitor the entire area around the punch tip. With an optical resolution of only 2 mm, the system allows the speed change point to be positioned 0 mm from the sheet metal, significantly improving productivity. This results in a faster bending cycle, saving up to 3 seconds per bend.
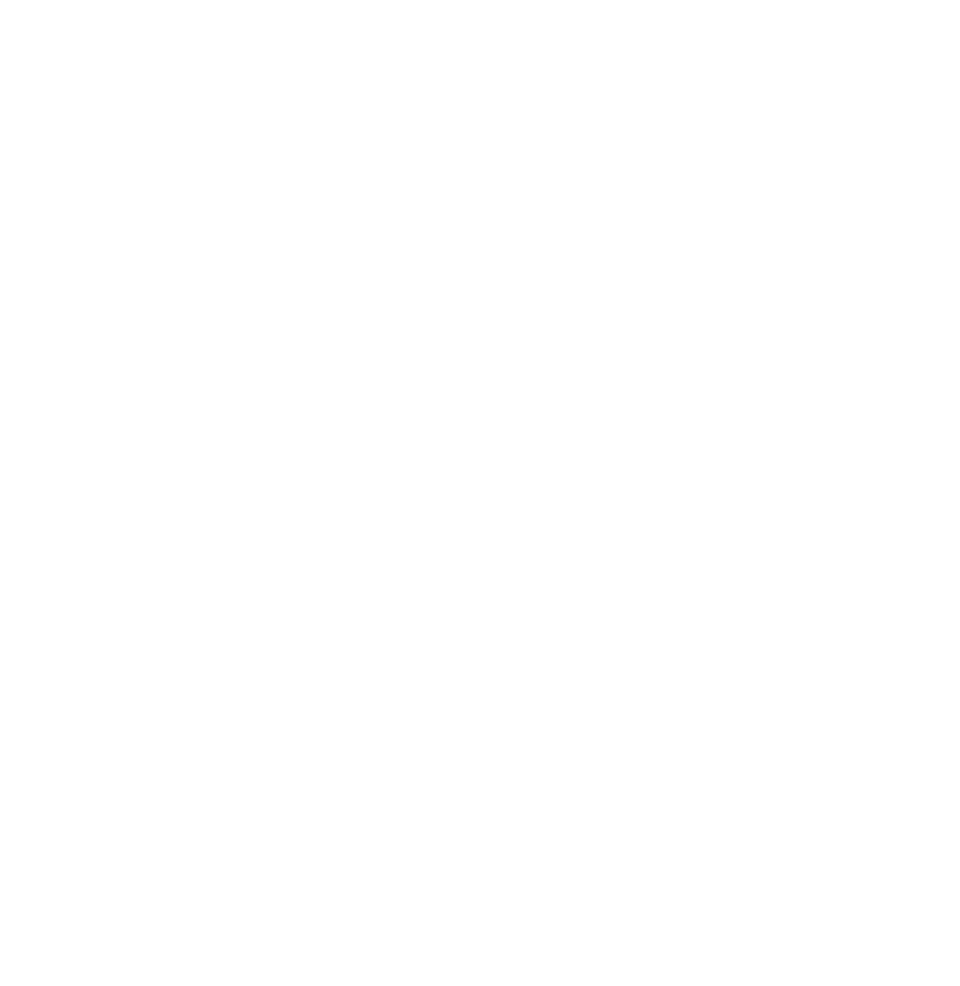
Clamping system
The Gasparini AirSlide pneumatic upper clamping system, with a height of 110 mm, is designed for European tools and uses an internal compressed air distribution system. This allows components to be freely positioned along the crossbar, without the need for piping or tools. Elements can be added or removed in any configuration, keeping the airtightness intact.
In addition, AirSlide elements are self-aligning: the punches are raised and positioned automatically. Thanks to the front centring wedges, the punches can be brought closer together, remaining stable even with the clamp open and supporting the use of segmented tools. The bottom clamping is also pneumatic, making the set-up process quick and intuitive.
Backgauge
The backgauge is configured on 5 axes (X-R-Z1-Z2-X6) fully CNC-controlled, with an additional stop for precision positioning.
The system is also equipped with two retractable sheet supports, designed to support even the thinnest sheet metal, ensuring undamaged surfaces without scratches.
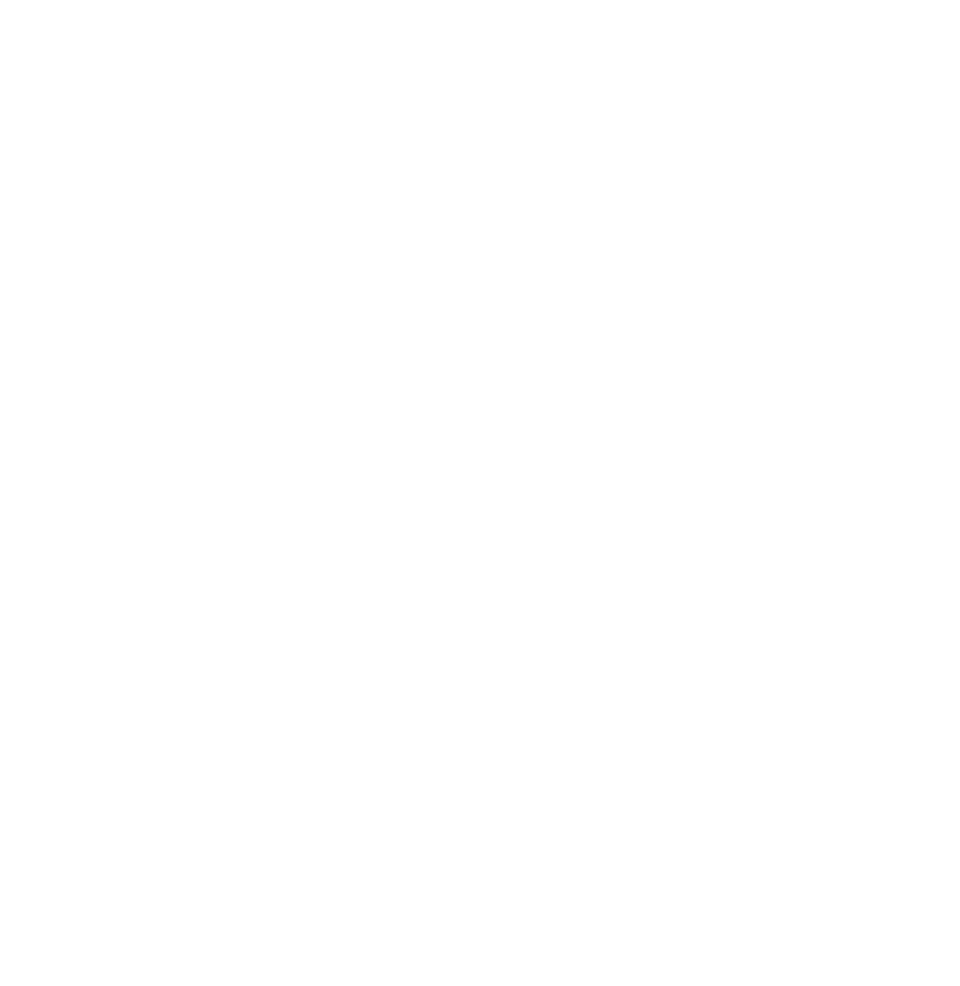
Other systems and accessories
In addition, this X-press 165/3000 has been equipped with:
- ECO energy-saving system
- 2 sliding front supports
- 1 sliding Lazer Safe wireless footpedal
- Tele-Link remote assistance
- LED work area lighting
- GPS4 mechanical set-up
- Drive bar for tool positioning