Customised colour
One of the distinguishing features of this press brake is its colour. At the customer’s request, a colour representative of his corporate identity was used, replacing the classic Gasparini blue and giving the machine a truly personalised and unique touch.
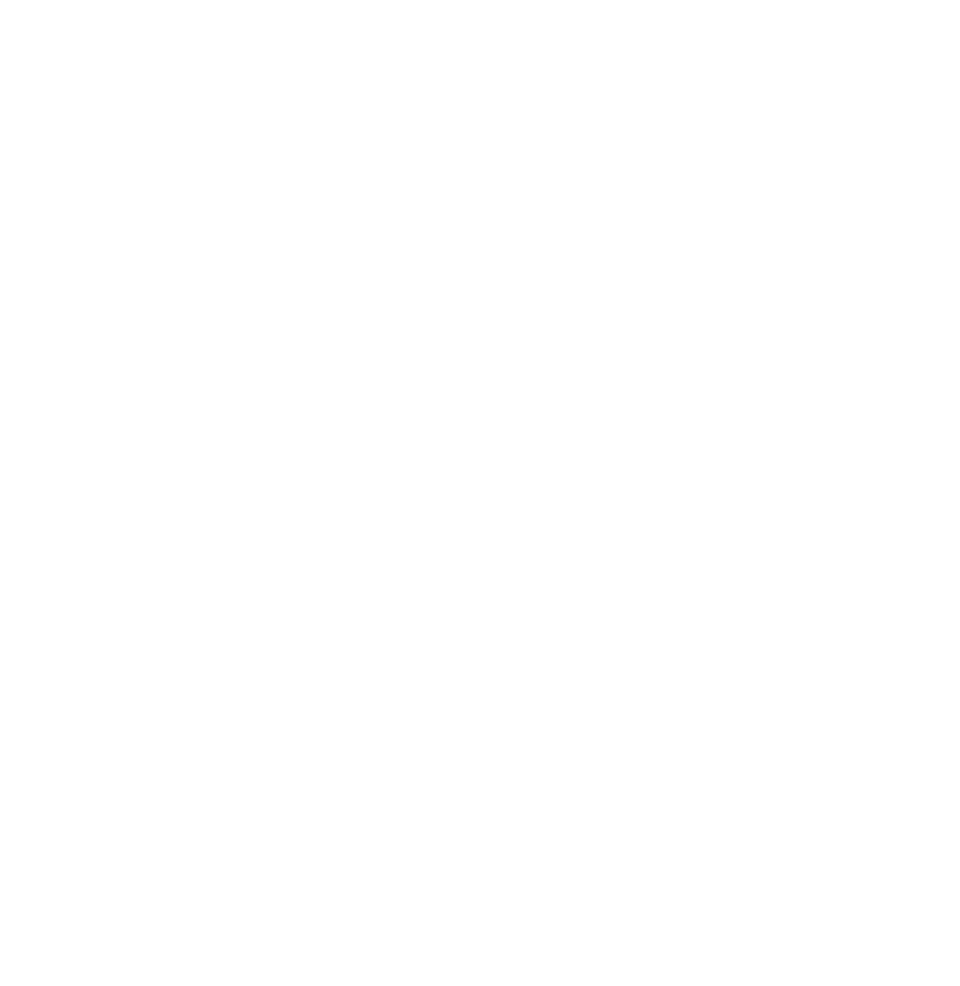
E-Reflex Deformation Compensation System
The E-Reflex system automatically compensates for bending of the press brake side frames during the bending process. Through a network of sensors, E-Reflex detects and measures structural deformations, comparing the data with the beam position and oil pressure. In this way, the actual punch position can be calculated in real time, guaranteeing angle constancy regardless of length, thickness, or sheet characteristics.
Gasparini Adaptive Crowning System
Sheet metal properties can vary unpredictably, causing deformations that make precise bending complex. To compensate for the bending of the upper beam and maintain a constant angle along the profile, Gasparini developed the adaptive bending system. Using two precision sensors, the system detects the deformation of the upper beam in real time and automatically adjusts the position of the die, keeping the beams perfectly parallel. This guarantees precise and repeatable angles, regardless of sheet metal characteristics or material variations.
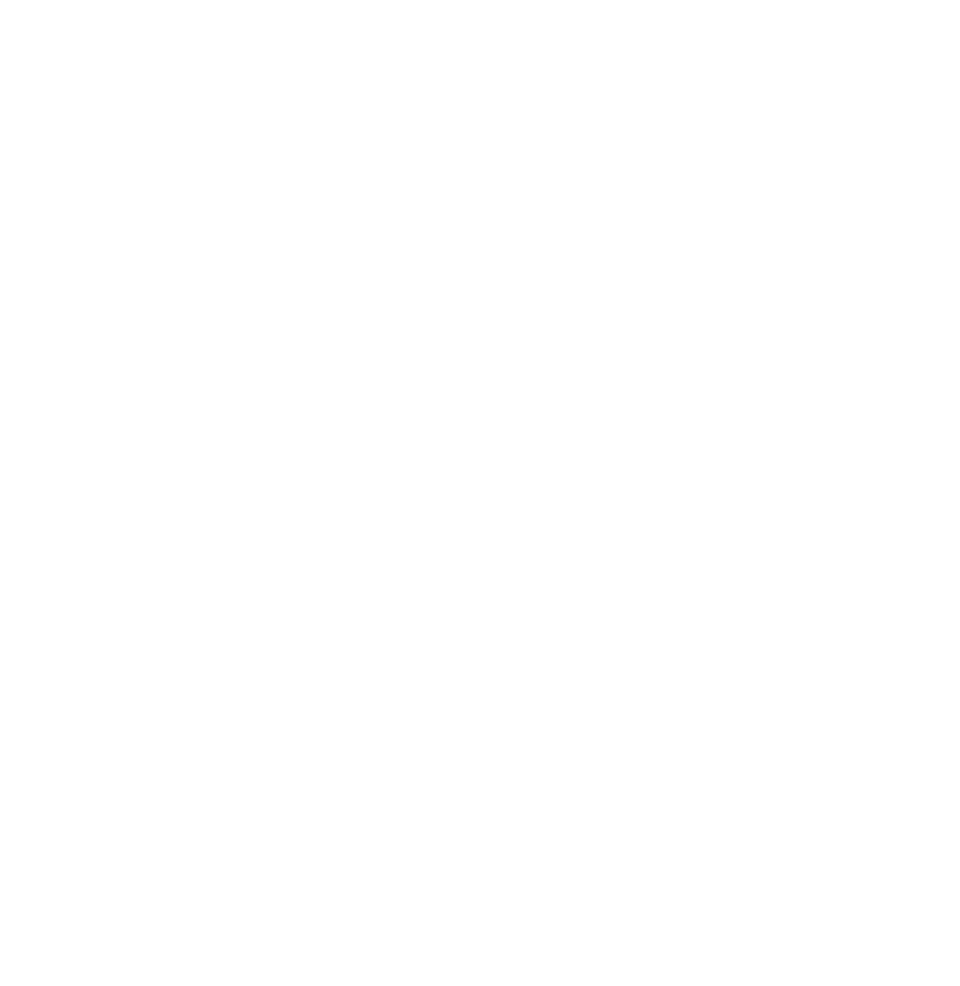
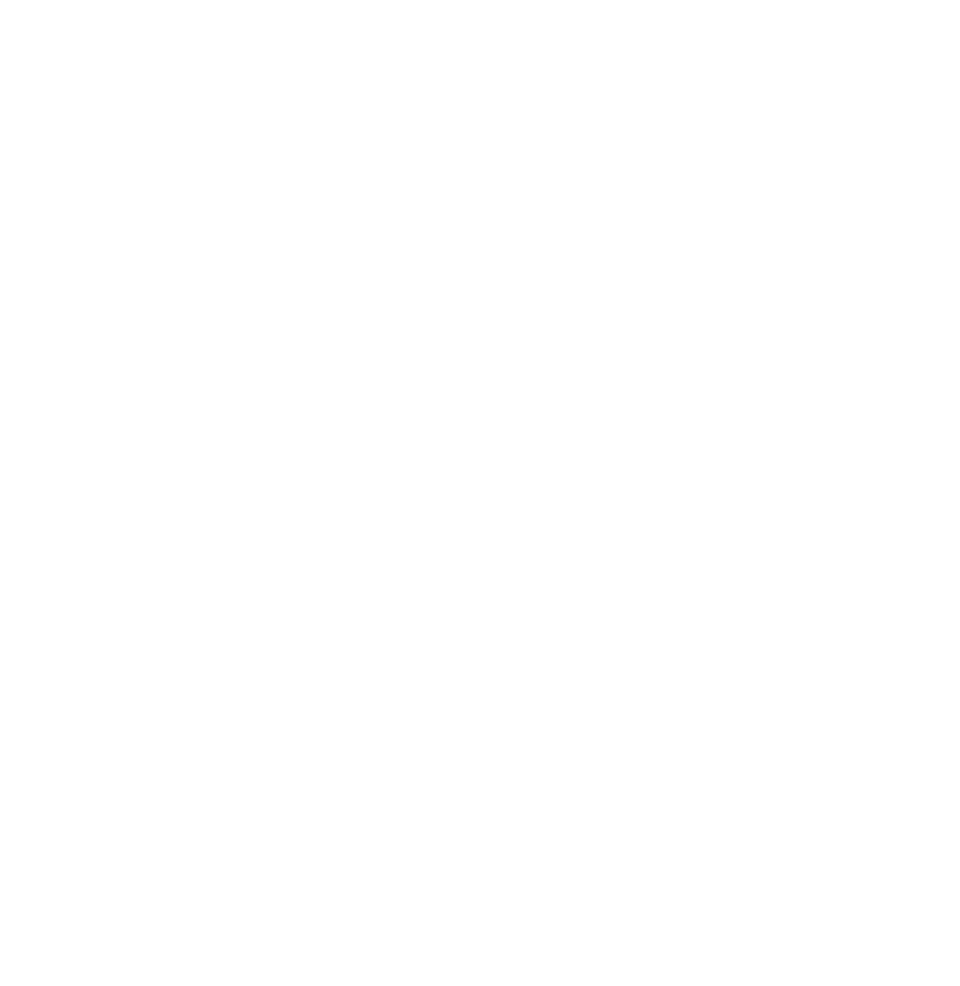
Mobile desk with double monitor
The customer opted for a mobile desk equipped with dual monitors, with a configuration designed to maximise productivity. The first monitor is dedicated to the Delem DA-69S CNC, equipped with Delem Profile-S 3D offline software, which allows advanced programming in both 2D and 3D, with automatic bending sequence calculation and collision detection. The machine’s 3D configuration, complete with multiple tool stations, provides accurate feedback on product feasibility and handling.
The second monitor acts as a support and can be connected to enterprise devices or other control tools, facilitating real-time production monitoring and management. Thanks to advanced control algorithms, the DA-69S optimises the work cycle and minimises setup times, improving operational efficiency.
Backgauge
The backgauge is configured on 5 axes (X-R-Z1-Z2-X6) fully controlled by the CNC, with an additional stop for precision positioning.
The backgauges include an integrated anti-collision safety system, which intervenes in the event of violent impacts: if the reference is struck with force, the device releases it to prevent damage or loss of position. In such cases, the operator can quickly restore the references to their original position.
The system is also equipped with two retractile back supports, designed to support even the thinnest sheets, ensuring undamaged surfaces without scratches.
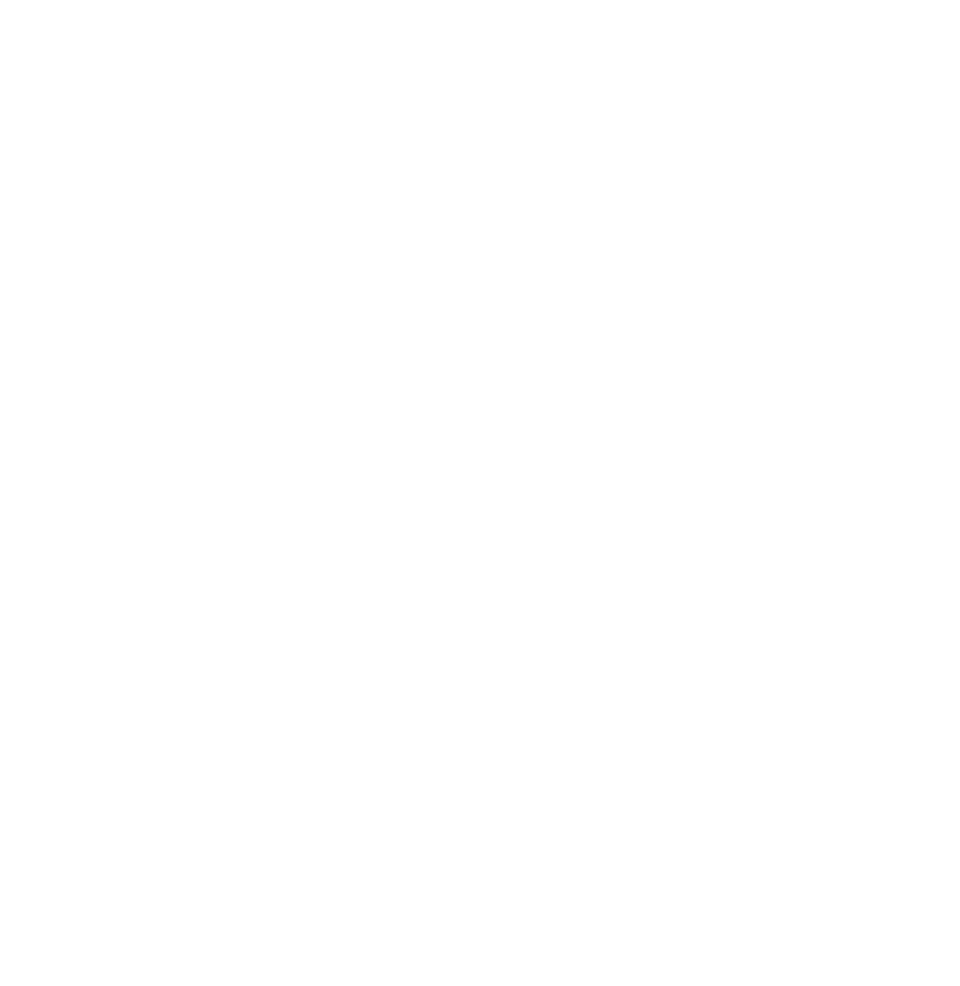
Drive bar
The Drive Bar is a coloured LED light bar, controlled directly from the CNC, ideal for press brakes with multiple work stations. This system is designed to:
- Guide the operator in the correct positioning of the tools, according to the bending programme
- Support the operator in moving to the next station and accurately positioning the workpiece, particularly useful in multi-station setups
The blue light indicates the area for tool assembly, while the green light indicates the position for workpiece insertion.
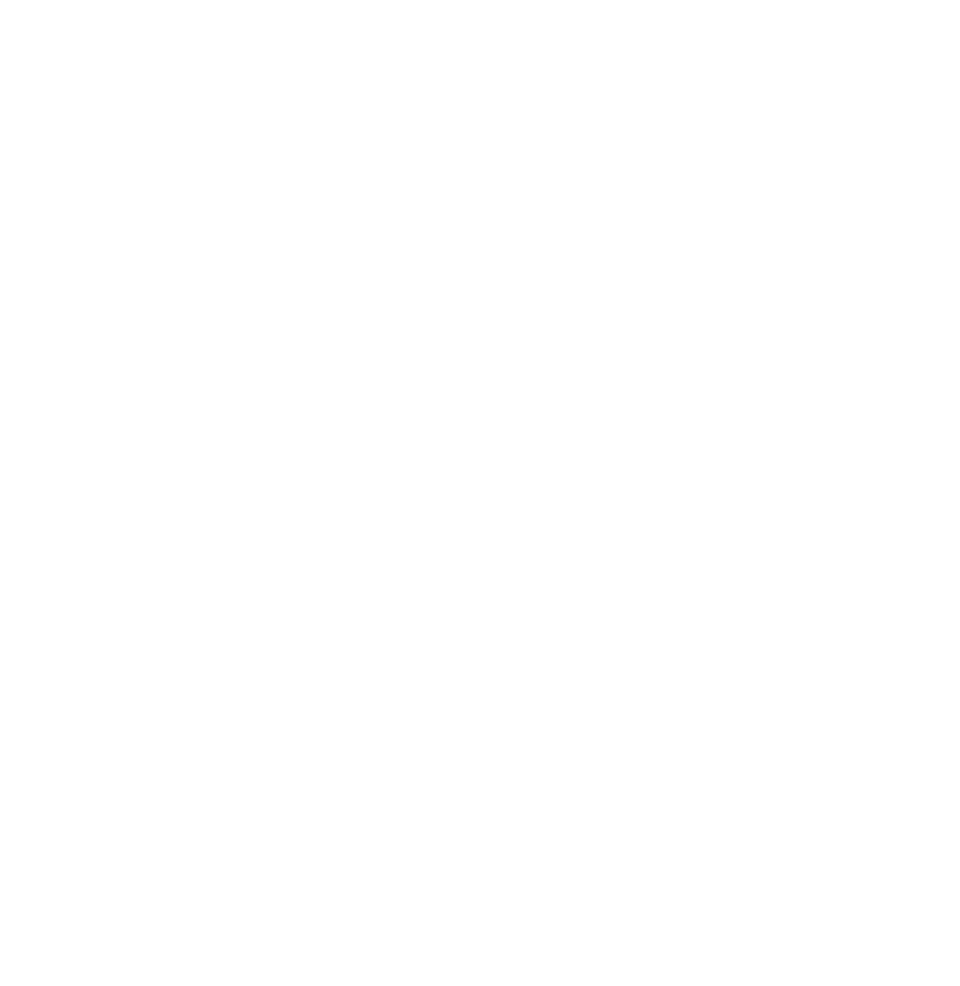
Safety system
Clamping system
The top clamping system is the pneumatic Gasparini AirSlide, with a height of 110 mm for European-type tools. This system utilises an internal distribution of compressed air, allowing components to be positioned along the beam freely and without the need for pipes or tools. Components can be added or removed in any configuration without compromising integrity or causing air leaks.
What’s more, AirSlide elements are self-aligning: the punches lift and position correctly automatically. Thanks to the frontal centring wedges, the punches can be brought closer together and remain stable even with the clamping open, supporting the use of segmented tools. The bottom clamping is also pneumatic, ensuring a quick and intuitive set-up process.
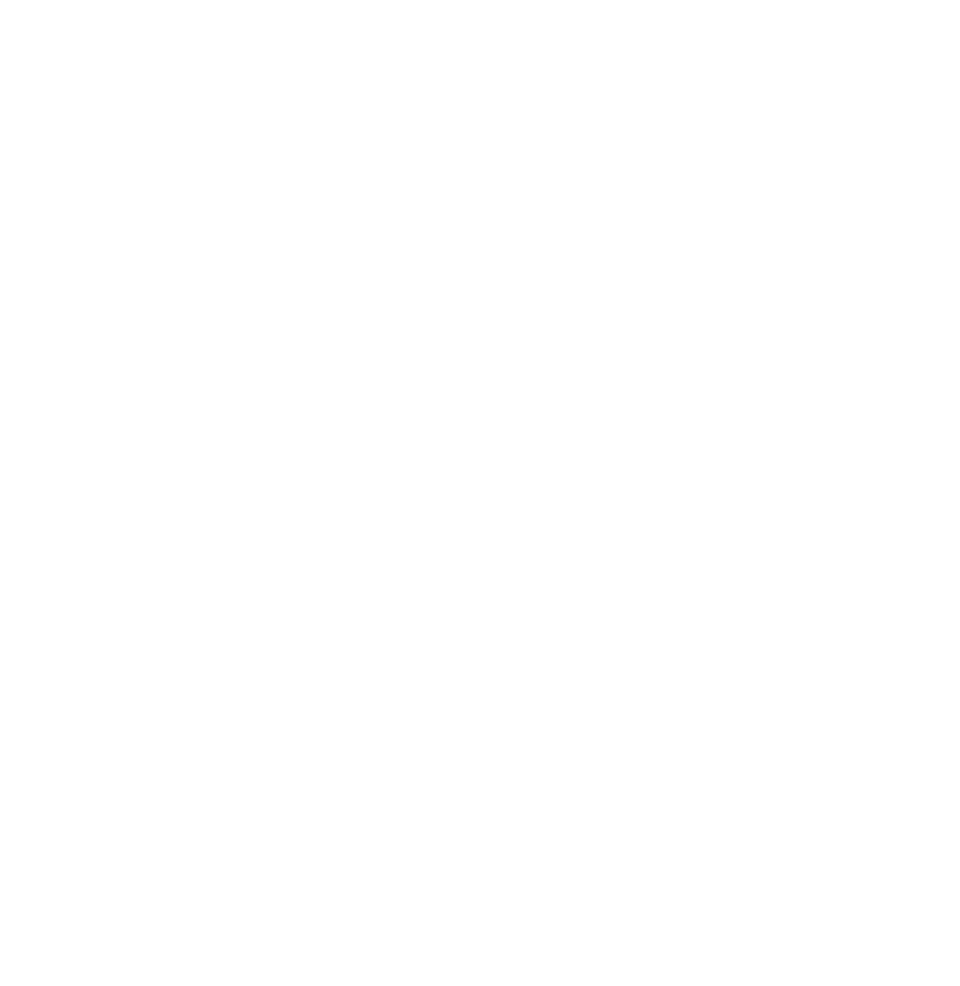
Other systems and accessories
In addition, this 165/3000 press brake is designed and manufactured with:
- Stand-By energy-saving system
- 2 sliding front supports
- 1 standard footpedal
- 1 additional footpedal
- Provision for Tele-Link remote assistance
- LED work area lighting
- Mechanical preparation for front sheet lifter
- Industry 4.0 package